
三维扫描技术是如何简化增材制造工艺的质量控制?
发布时间:2023/09/20
- 访问量:
【概要描述】 增材制造通常称为3D打印,因其独特的生产复杂形状的能力而非常有用,其性能优于传统制造的产品。不需要像冲压、锻造和成型那样的工具,也不会像大多数减材工艺那样浪费材料。许多单独的组件可以打印为一个整体,从而简化了生产、组装和检查。增材制造零件可以使用多种材料生产,这些材料的强度、耐用性和性能与传统制造的零件相匹配。
使用从粉末床熔融到粘合剂喷射再到还原聚合增材制造的一系列技术,由聚合物、树脂和金属等材料逐层成型产品。与小批量和迭代设计应用中的注塑成型和 CNC 加工相比,由于其速度快且相对简单,它已成为快速原型制作的标准方法。
过去十年,增材制造开始取代传统制造进行全面生产,这给制造专业人士带来了新的挑战。在生产制造中更广泛地采用增材制造的障碍之一是复杂增材制造部件的质量控制和零件检验
质量控制在制造中的重要性
质量控制对于确保零件和产品符合规格并按预期运行至关重要。这对于保持制造操作的一致性和可重复性也至关重要。
如果没有可靠的质量控制措施,制造企业将不愿意大批量生产增材制造的零件,这可能会危及他们的声誉。对于航空航天、汽车和医疗等自然适用增材制造的行业尤其如此。这些行业都受到严格监管,但也能从高复杂性、多品种、小批量零件的高效生产中获益最多。
然而,精确的质量控制取决于评估功能、可靠性和安全性等因素的标准化方法。增材制造的这些标准本质上很难建立,因为增材制造技术之间的制造过程差异很大。支撑结构和成型板的去除、热通量、残留的粉末或树脂、后处理和其他因素都给质量控制人员带来了新的挑战。
此外,增材制造领域的快速创新使得监管机构和标准组织争先恐后地掌握新兴材料和方法的领先地位。ASTM 和 ISO 合作制定了各种已发布的标准,涵盖增材制造应用、设计、材料、工艺、术语和测试方法。但在许多情况下,仍然需要恢复到增材制造之前制定的旧标准。
考虑到所有这些,增材制造检查员只能使用 GD&T 的轮廓标注来分析复杂的表面,这需要收集高密度的表面测量结果。传统的检测工具(接触式/CMM)使这个过程非常耗时。但随着 3D 扫描仪的精度不断提高,这些测量变得更加方便。
为什么传统的质量控制方法对增材制造提出挑战
增材制造的检查标准在较新的应用中建立得较少,而在较旧的应用中则更加充实。
例如,在医疗保健领域,对于为特定患者定制 3D 打印的部件(例如植入物或假体),检查方法更加成熟,因为这些是最早的商业增材制造应用之一。具有高度有机解剖区域的零件可以进行 3D 扫描,并与成型文件进行比较,其中可以应用统计方法与特征控制相结合。与精密加工相比,人体的公差也相当宽松,因此扫描的采用发生得更早。
了解为什么传统测量工具难以在增材制造中采用也很重要。这些手动工具(如卡尺和物理量规套件)使用起来非常简单,并且非常精确,但它们一次只能测量一个几何特征(例如尺寸、形状或角度),并且不会以数字方式捕获数据。这使得它们使用起来既耗时又费力,而且通常不太适合依赖高效数字工作流程蓬勃发展的增材制造。
另一种常见的检查和质量保证方法是破坏性测试,其中包括各种疲劳、断裂和机械测试。破坏性测试昂贵、缓慢且浪费。它也可能无法揭示涉及多个制造步骤的复杂 3D 打印零件失败的根本原因。
例如,金属 3D 打印零件可能涉及打印、热处理、支撑去除、板去除和精加工。其中任何一项都可以改变零件的形状和性能。除非您知道问题发生在哪里,否则当问题是后续步骤造成的时,破坏性机械测试可能会导致您浪费大量时间来尝试调整打印过程。如有必要,破坏性测试可用于验证机器/材料组合与测试优惠券,但应避免用于最终使用零件。
为什么3D扫描对于增材制造有意义
增材制造的零件通常具有高度的工程复杂性,无论是复杂的晶格、陀螺仪、填充物还是拓扑优化。这就是增材制造的全部目的——创新地利用这些只能通过增材方式生产的非常规形状和结构。
这正 3D 扫描成为 3D 打印理想质量控制机制的原因,因为它的功能与增材制造零件的性质非常契合。其中一些关键应用包括:
全形态采集
如果没有 3D 扫描,就不可能看到零件或产品的全貌。比较图 1 中的两幅图像,很明显,1,000 个数据点(通过传统方式仍然需要相对较长的时间来获取)看起来远不如具有超过 900 万个数据点的完整 3D 扫描清晰。就精确度而言,3D 扫描提供的高保真数据采集是无法比拟的。
非接触式捕捉
许多增材制造零件涉及不应触摸的薄结构或柔软表面,因为它们可能变形,或者有特定的清洁度要求。在这些情况下,光学 3D 扫描比其他方法具有另一个优势
数字保留和归档
通过 3D 扫描进行的全形态采集与增材制造中常见的数字工作流程配合良好。它允许制造企业根据需要保留受检零件的完整数字副本,即使在运输和使用之后也是如此。例如,这可以为未来了解零件磨损和疲劳带来回报。
流道设计
例如,通过 3D CT 扫描捕获整体形状,设计人员和工程师可以检查铸造模型的喷射应用是否不仅可以成型内部通道和枢轴喷嘴,还可以清理这些通道。在这种情况下,破坏性测试也是一种选择,但选择的任何单个横截面都可能导致误报或误报。另一方面,使用 CT 系统进行 3D 扫描可以查看零件的所有横截面。
晶格检查
通过使用 3D CT 扫描,设计人员可以执行晶格检查,以确保节点和带正确放置、晶格位于零件的正确区域以及配合表面针对应用正确交互。
成型体积检查
在许多情况下,测量成型中的任何单个产品可能会给您对该成型期间发生的情况产生不同的印象。通过 3D 扫描进行成型体积检查,您可以检查所有零件,以了解哪些零件的偏差和翘曲风险最高。从此时起,您可以相应地修改零件的成型样式。3D 扫描还可以在后处理过程的每个步骤中存档您的零件,以跟踪整个过程中的所有几何变化。
增材制造的质量控制和检测解决方案
在增材制造中实施用于质量控制和检查的 3D 扫描需要两个组件:扫描仪和能够管理数据的软件应用程序。就光学 3D 扫描技术而言,主要用于 AM 检测的两种类型是激光线探针和结构光扫描仪。
激光扫描
激光三角测量通过测量投射到物体表面的激光束的变形来捕获物体。一个或多个激光源将非常小的点投射到表面上,并且一台或多台摄像机记录这些点的位置。
激光线点和相机之间的角度是预先确定的,以便计算 3D 三角测量。当激光线穿过物体表面时,动态计算会在 3D 空间中记录这些点。这种方法可产生准确、高分辨率的扫描,并且当物体反光和/或黑暗且有光泽时最有效。
通常将激光器安装在由外部系统(激光器或光学跟踪器)跟踪的移动平台(传统或便携式 CMM)上,或者保持激光器固定并让零件在传送带或转盘上在其下方移动。
结构光扫描
结构光扫描一般使用一台投光器和多个相机。它与激光三角测量类似,但它测量投影在表面上的条纹图案或网格的变形。
通常,蓝色 LED 或激光照射 DLP 芯片以产生交替的明暗区域,称为条纹图案。当图案在表面上移动时,相机会收集有关已知图案变化的数据,并对距离进行三角测量以创建点云。
考虑到经常使用的机载摄像头的分辨率,结构光可以创建密集的点云,在锐利的边缘上具有丰富的细节。
CT扫描
计算机断层扫描 (CT) 扫描仪是 3D 扫描的第三种选择。CT 扫描可生成产品内部细节的完整视图,并且数据是数字化的,这两者都对 3D 打印零件有帮助。具体来说,CT 扫描可以实现通道设计和晶格检查,这两者都需要有关零件内部的数据。从历史上看,CT 扫描仪一直非常昂贵,尽管某些型号的价格已经下降。
用于增材制造的质量控制和检测软件
然而,使用扫描仪收集数据只是第一步。软件对于以有意义且可靠的方式处理数据至关重要。扫描软件将点云叠加到 CAD 或 STL 参考数据上,以提取比较点和测量结果。
扫描软件选项包括:
1、传统的接触式检测软件旨在与坐标测量机和其他接触式方法配合使用,非接触式扫描是新发展的技术
2、专为 3D 扫描设计的扫描原生检测软件
与传统 CMM 软件相比,扫描原生软件具有一些重要优势,因为它专为现代高分辨率 3D 扫描而成型。这些软件有这些功能:
1、更快、更轻松地处理大型数据集
2、通过用于噪声过滤和几何拟合的扫描本机算法实现高精度
3、通过横截面、边界、曲线、轮廓和虚拟边缘比较来检测偏差
4、通过自动识别 3D 扫描中的特征并智能过滤数据来加速 GD&T 计算
5、创建包含完整测量历史记录及其趋势的数字档案
例如Geomagic Control X是 Oqton 的扫描原生计量软件。它与任何光学扫描仪或便携式 CMM 臂集成,收集和分析非常大的数据集,并自动执行重复和复杂的任务,因此用户只需很少或没有培训即可获得准确的结果。对于许多增材制造企业来说,它是质量控制和检测中 3D 扫描的理想起点。
为高效的增材制造质量控制和检查做好准备
无论您采取什么方式,用于质量控制和检查的 3D 扫描都是增材制造从原型设计到大规模生产的关键一步。通过简化检查流程,3D 扫描可帮助制造企业节省时间、更轻松地执行高级分析并更准确地检测问题。
最重要的是,高保真 3D 检测为增材制造企业提供了数据,以建立复杂零件的质量控制标准,并确保这些零件满足性能和合规性期望,即使是最苛刻和高度监管的行业。
三维扫描技术是如何简化增材制造工艺的质量控制?
【概要描述】 增材制造通常称为3D打印,因其独特的生产复杂形状的能力而非常有用,其性能优于传统制造的产品。不需要像冲压、锻造和成型那样的工具,也不会像大多数减材工艺那样浪费材料。许多单独的组件可以打印为一个整体,从而简化了生产、组装和检查。增材制造零件可以使用多种材料生产,这些材料的强度、耐用性和性能与传统制造的零件相匹配。
使用从粉末床熔融到粘合剂喷射再到还原聚合增材制造的一系列技术,由聚合物、树脂和金属等材料逐层成型产品。与小批量和迭代设计应用中的注塑成型和 CNC 加工相比,由于其速度快且相对简单,它已成为快速原型制作的标准方法。
过去十年,增材制造开始取代传统制造进行全面生产,这给制造专业人士带来了新的挑战。在生产制造中更广泛地采用增材制造的障碍之一是复杂增材制造部件的质量控制和零件检验
质量控制在制造中的重要性
质量控制对于确保零件和产品符合规格并按预期运行至关重要。这对于保持制造操作的一致性和可重复性也至关重要。
如果没有可靠的质量控制措施,制造企业将不愿意大批量生产增材制造的零件,这可能会危及他们的声誉。对于航空航天、汽车和医疗等自然适用增材制造的行业尤其如此。这些行业都受到严格监管,但也能从高复杂性、多品种、小批量零件的高效生产中获益最多。
然而,精确的质量控制取决于评估功能、可靠性和安全性等因素的标准化方法。增材制造的这些标准本质上很难建立,因为增材制造技术之间的制造过程差异很大。支撑结构和成型板的去除、热通量、残留的粉末或树脂、后处理和其他因素都给质量控制人员带来了新的挑战。
此外,增材制造领域的快速创新使得监管机构和标准组织争先恐后地掌握新兴材料和方法的领先地位。ASTM 和 ISO 合作制定了各种已发布的标准,涵盖增材制造应用、设计、材料、工艺、术语和测试方法。但在许多情况下,仍然需要恢复到增材制造之前制定的旧标准。
考虑到所有这些,增材制造检查员只能使用 GD&T 的轮廓标注来分析复杂的表面,这需要收集高密度的表面测量结果。传统的检测工具(接触式/CMM)使这个过程非常耗时。但随着 3D 扫描仪的精度不断提高,这些测量变得更加方便。
为什么传统的质量控制方法对增材制造提出挑战
增材制造的检查标准在较新的应用中建立得较少,而在较旧的应用中则更加充实。
例如,在医疗保健领域,对于为特定患者定制 3D 打印的部件(例如植入物或假体),检查方法更加成熟,因为这些是最早的商业增材制造应用之一。具有高度有机解剖区域的零件可以进行 3D 扫描,并与成型文件进行比较,其中可以应用统计方法与特征控制相结合。与精密加工相比,人体的公差也相当宽松,因此扫描的采用发生得更早。
了解为什么传统测量工具难以在增材制造中采用也很重要。这些手动工具(如卡尺和物理量规套件)使用起来非常简单,并且非常精确,但它们一次只能测量一个几何特征(例如尺寸、形状或角度),并且不会以数字方式捕获数据。这使得它们使用起来既耗时又费力,而且通常不太适合依赖高效数字工作流程蓬勃发展的增材制造。
另一种常见的检查和质量保证方法是破坏性测试,其中包括各种疲劳、断裂和机械测试。破坏性测试昂贵、缓慢且浪费。它也可能无法揭示涉及多个制造步骤的复杂 3D 打印零件失败的根本原因。
例如,金属 3D 打印零件可能涉及打印、热处理、支撑去除、板去除和精加工。其中任何一项都可以改变零件的形状和性能。除非您知道问题发生在哪里,否则当问题是后续步骤造成的时,破坏性机械测试可能会导致您浪费大量时间来尝试调整打印过程。如有必要,破坏性测试可用于验证机器/材料组合与测试优惠券,但应避免用于最终使用零件。
为什么3D扫描对于增材制造有意义
增材制造的零件通常具有高度的工程复杂性,无论是复杂的晶格、陀螺仪、填充物还是拓扑优化。这就是增材制造的全部目的——创新地利用这些只能通过增材方式生产的非常规形状和结构。
这正 3D 扫描成为 3D 打印理想质量控制机制的原因,因为它的功能与增材制造零件的性质非常契合。其中一些关键应用包括:
全形态采集
如果没有 3D 扫描,就不可能看到零件或产品的全貌。比较图 1 中的两幅图像,很明显,1,000 个数据点(通过传统方式仍然需要相对较长的时间来获取)看起来远不如具有超过 900 万个数据点的完整 3D 扫描清晰。就精确度而言,3D 扫描提供的高保真数据采集是无法比拟的。
非接触式捕捉
许多增材制造零件涉及不应触摸的薄结构或柔软表面,因为它们可能变形,或者有特定的清洁度要求。在这些情况下,光学 3D 扫描比其他方法具有另一个优势
数字保留和归档
通过 3D 扫描进行的全形态采集与增材制造中常见的数字工作流程配合良好。它允许制造企业根据需要保留受检零件的完整数字副本,即使在运输和使用之后也是如此。例如,这可以为未来了解零件磨损和疲劳带来回报。
流道设计
例如,通过 3D CT 扫描捕获整体形状,设计人员和工程师可以检查铸造模型的喷射应用是否不仅可以成型内部通道和枢轴喷嘴,还可以清理这些通道。在这种情况下,破坏性测试也是一种选择,但选择的任何单个横截面都可能导致误报或误报。另一方面,使用 CT 系统进行 3D 扫描可以查看零件的所有横截面。
晶格检查
通过使用 3D CT 扫描,设计人员可以执行晶格检查,以确保节点和带正确放置、晶格位于零件的正确区域以及配合表面针对应用正确交互。
成型体积检查
在许多情况下,测量成型中的任何单个产品可能会给您对该成型期间发生的情况产生不同的印象。通过 3D 扫描进行成型体积检查,您可以检查所有零件,以了解哪些零件的偏差和翘曲风险最高。从此时起,您可以相应地修改零件的成型样式。3D 扫描还可以在后处理过程的每个步骤中存档您的零件,以跟踪整个过程中的所有几何变化。
增材制造的质量控制和检测解决方案
在增材制造中实施用于质量控制和检查的 3D 扫描需要两个组件:扫描仪和能够管理数据的软件应用程序。就光学 3D 扫描技术而言,主要用于 AM 检测的两种类型是激光线探针和结构光扫描仪。
激光扫描
激光三角测量通过测量投射到物体表面的激光束的变形来捕获物体。一个或多个激光源将非常小的点投射到表面上,并且一台或多台摄像机记录这些点的位置。
激光线点和相机之间的角度是预先确定的,以便计算 3D 三角测量。当激光线穿过物体表面时,动态计算会在 3D 空间中记录这些点。这种方法可产生准确、高分辨率的扫描,并且当物体反光和/或黑暗且有光泽时最有效。
通常将激光器安装在由外部系统(激光器或光学跟踪器)跟踪的移动平台(传统或便携式 CMM)上,或者保持激光器固定并让零件在传送带或转盘上在其下方移动。
结构光扫描
结构光扫描一般使用一台投光器和多个相机。它与激光三角测量类似,但它测量投影在表面上的条纹图案或网格的变形。
通常,蓝色 LED 或激光照射 DLP 芯片以产生交替的明暗区域,称为条纹图案。当图案在表面上移动时,相机会收集有关已知图案变化的数据,并对距离进行三角测量以创建点云。
考虑到经常使用的机载摄像头的分辨率,结构光可以创建密集的点云,在锐利的边缘上具有丰富的细节。
CT扫描
计算机断层扫描 (CT) 扫描仪是 3D 扫描的第三种选择。CT 扫描可生成产品内部细节的完整视图,并且数据是数字化的,这两者都对 3D 打印零件有帮助。具体来说,CT 扫描可以实现通道设计和晶格检查,这两者都需要有关零件内部的数据。从历史上看,CT 扫描仪一直非常昂贵,尽管某些型号的价格已经下降。
用于增材制造的质量控制和检测软件
然而,使用扫描仪收集数据只是第一步。软件对于以有意义且可靠的方式处理数据至关重要。扫描软件将点云叠加到 CAD 或 STL 参考数据上,以提取比较点和测量结果。
扫描软件选项包括:
1、传统的接触式检测软件旨在与坐标测量机和其他接触式方法配合使用,非接触式扫描是新发展的技术
2、专为 3D 扫描设计的扫描原生检测软件
与传统 CMM 软件相比,扫描原生软件具有一些重要优势,因为它专为现代高分辨率 3D 扫描而成型。这些软件有这些功能:
1、更快、更轻松地处理大型数据集
2、通过用于噪声过滤和几何拟合的扫描本机算法实现高精度
3、通过横截面、边界、曲线、轮廓和虚拟边缘比较来检测偏差
4、通过自动识别 3D 扫描中的特征并智能过滤数据来加速 GD&T 计算
5、创建包含完整测量历史记录及其趋势的数字档案
例如Geomagic Control X是 Oqton 的扫描原生计量软件。它与任何光学扫描仪或便携式 CMM 臂集成,收集和分析非常大的数据集,并自动执行重复和复杂的任务,因此用户只需很少或没有培训即可获得准确的结果。对于许多增材制造企业来说,它是质量控制和检测中 3D 扫描的理想起点。
为高效的增材制造质量控制和检查做好准备
无论您采取什么方式,用于质量控制和检查的 3D 扫描都是增材制造从原型设计到大规模生产的关键一步。通过简化检查流程,3D 扫描可帮助制造企业节省时间、更轻松地执行高级分析并更准确地检测问题。
最重要的是,高保真 3D 检测为增材制造企业提供了数据,以建立复杂零件的质量控制标准,并确保这些零件满足性能和合规性期望,即使是最苛刻和高度监管的行业。
- 分类: 教育训练
- 发布时间:2023-09-20 13:54
- 访问量:
增材制造通常称为3D打印,因其独特的生产复杂形状的能力而非常有用,其性能优于传统制造的产品。不需要像冲压、锻造和成型那样的工具,也不会像大多数减材工艺那样浪费材料。许多单独的组件可以打印为一个整体,从而简化了生产、组装和检查。增材制造零件可以使用多种材料生产,这些材料的强度、耐用性和性能与传统制造的零件相匹配。
使用从粉末床熔融到粘合剂喷射再到还原聚合增材制造的一系列技术,由聚合物、树脂和金属等材料逐层成型产品。与小批量和迭代设计应用中的注塑成型和 CNC 加工相比,由于其速度快且相对简单,它已成为快速原型制作的标准方法。
过去十年,增材制造开始取代传统制造进行全面生产,这给制造专业人士带来了新的挑战。在生产制造中更广泛地采用增材制造的障碍之一是复杂增材制造部件的质量控制和零件检验
质量控制在制造中的重要性
质量控制对于确保零件和产品符合规格并按预期运行至关重要。这对于保持制造操作的一致性和可重复性也至关重要。
如果没有可靠的质量控制措施,制造企业将不愿意大批量生产增材制造的零件,这可能会危及他们的声誉。对于航空航天、汽车和医疗等自然适用增材制造的行业尤其如此。这些行业都受到严格监管,但也能从高复杂性、多品种、小批量零件的高效生产中获益最多。
然而,精确的质量控制取决于评估功能、可靠性和安全性等因素的标准化方法。增材制造的这些标准本质上很难建立,因为增材制造技术之间的制造过程差异很大。支撑结构和成型板的去除、热通量、残留的粉末或树脂、后处理和其他因素都给质量控制人员带来了新的挑战。
此外,增材制造领域的快速创新使得监管机构和标准组织争先恐后地掌握新兴材料和方法的领先地位。ASTM 和 ISO 合作制定了各种已发布的标准,涵盖增材制造应用、设计、材料、工艺、术语和测试方法。但在许多情况下,仍然需要恢复到增材制造之前制定的旧标准。
考虑到所有这些,增材制造检查员只能使用 GD&T 的轮廓标注来分析复杂的表面,这需要收集高密度的表面测量结果。传统的检测工具(接触式/CMM)使这个过程非常耗时。但随着 3D 扫描仪的精度不断提高,这些测量变得更加方便。
为什么传统的质量控制方法对增材制造提出挑战
增材制造的检查标准在较新的应用中建立得较少,而在较旧的应用中则更加充实。
例如,在医疗保健领域,对于为特定患者定制 3D 打印的部件(例如植入物或假体),检查方法更加成熟,因为这些是最早的商业增材制造应用之一。具有高度有机解剖区域的零件可以进行 3D 扫描,并与成型文件进行比较,其中可以应用统计方法与特征控制相结合。与精密加工相比,人体的公差也相当宽松,因此扫描的采用发生得更早。
了解为什么传统测量工具难以在增材制造中采用也很重要。这些手动工具(如卡尺和物理量规套件)使用起来非常简单,并且非常精确,但它们一次只能测量一个几何特征(例如尺寸、形状或角度),并且不会以数字方式捕获数据。这使得它们使用起来既耗时又费力,而且通常不太适合依赖高效数字工作流程蓬勃发展的增材制造。
另一种常见的检查和质量保证方法是破坏性测试,其中包括各种疲劳、断裂和机械测试。破坏性测试昂贵、缓慢且浪费。它也可能无法揭示涉及多个制造步骤的复杂 3D 打印零件失败的根本原因。
例如,金属 3D 打印零件可能涉及打印、热处理、支撑去除、板去除和精加工。其中任何一项都可以改变零件的形状和性能。除非您知道问题发生在哪里,否则当问题是后续步骤造成的时,破坏性机械测试可能会导致您浪费大量时间来尝试调整打印过程。如有必要,破坏性测试可用于验证机器/材料组合与测试优惠券,但应避免用于最终使用零件。
为什么3D扫描对于增材制造有意义
增材制造的零件通常具有高度的工程复杂性,无论是复杂的晶格、陀螺仪、填充物还是拓扑优化。这就是增材制造的全部目的——创新地利用这些只能通过增材方式生产的非常规形状和结构。
这正 3D 扫描成为 3D 打印理想质量控制机制的原因,因为它的功能与增材制造零件的性质非常契合。其中一些关键应用包括:
全形态采集
如果没有 3D 扫描,就不可能看到零件或产品的全貌。比较图 1 中的两幅图像,很明显,1,000 个数据点(通过传统方式仍然需要相对较长的时间来获取)看起来远不如具有超过 900 万个数据点的完整 3D 扫描清晰。就精确度而言,3D 扫描提供的高保真数据采集是无法比拟的。
非接触式捕捉
许多增材制造零件涉及不应触摸的薄结构或柔软表面,因为它们可能变形,或者有特定的清洁度要求。在这些情况下,光学 3D 扫描比其他方法具有另一个优势
数字保留和归档
通过 3D 扫描进行的全形态采集与增材制造中常见的数字工作流程配合良好。它允许制造企业根据需要保留受检零件的完整数字副本,即使在运输和使用之后也是如此。例如,这可以为未来了解零件磨损和疲劳带来回报。
流道设计
例如,通过 3D CT 扫描捕获整体形状,设计人员和工程师可以检查铸造模型的喷射应用是否不仅可以成型内部通道和枢轴喷嘴,还可以清理这些通道。在这种情况下,破坏性测试也是一种选择,但选择的任何单个横截面都可能导致误报或误报。另一方面,使用 CT 系统进行 3D 扫描可以查看零件的所有横截面。
晶格检查
通过使用 3D CT 扫描,设计人员可以执行晶格检查,以确保节点和带正确放置、晶格位于零件的正确区域以及配合表面针对应用正确交互。
成型体积检查
在许多情况下,测量成型中的任何单个产品可能会给您对该成型期间发生的情况产生不同的印象。通过 3D 扫描进行成型体积检查,您可以检查所有零件,以了解哪些零件的偏差和翘曲风险最高。从此时起,您可以相应地修改零件的成型样式。3D 扫描还可以在后处理过程的每个步骤中存档您的零件,以跟踪整个过程中的所有几何变化。
增材制造的质量控制和检测解决方案
在增材制造中实施用于质量控制和检查的 3D 扫描需要两个组件:扫描仪和能够管理数据的软件应用程序。就光学 3D 扫描技术而言,主要用于 AM 检测的两种类型是激光线探针和结构光扫描仪。
激光扫描
激光三角测量通过测量投射到物体表面的激光束的变形来捕获物体。一个或多个激光源将非常小的点投射到表面上,并且一台或多台摄像机记录这些点的位置。
激光线点和相机之间的角度是预先确定的,以便计算 3D 三角测量。当激光线穿过物体表面时,动态计算会在 3D 空间中记录这些点。这种方法可产生准确、高分辨率的扫描,并且当物体反光和/或黑暗且有光泽时最有效。
通常将激光器安装在由外部系统(激光器或光学跟踪器)跟踪的移动平台(传统或便携式 CMM)上,或者保持激光器固定并让零件在传送带或转盘上在其下方移动。
结构光扫描
结构光扫描一般使用一台投光器和多个相机。它与激光三角测量类似,但它测量投影在表面上的条纹图案或网格的变形。
通常,蓝色 LED 或激光照射 DLP 芯片以产生交替的明暗区域,称为条纹图案。当图案在表面上移动时,相机会收集有关已知图案变化的数据,并对距离进行三角测量以创建点云。
考虑到经常使用的机载摄像头的分辨率,结构光可以创建密集的点云,在锐利的边缘上具有丰富的细节。
CT扫描
计算机断层扫描 (CT) 扫描仪是 3D 扫描的第三种选择。CT 扫描可生成产品内部细节的完整视图,并且数据是数字化的,这两者都对 3D 打印零件有帮助。具体来说,CT 扫描可以实现通道设计和晶格检查,这两者都需要有关零件内部的数据。从历史上看,CT 扫描仪一直非常昂贵,尽管某些型号的价格已经下降。
用于增材制造的质量控制和检测软件
然而,使用扫描仪收集数据只是第一步。软件对于以有意义且可靠的方式处理数据至关重要。扫描软件将点云叠加到 CAD 或 STL 参考数据上,以提取比较点和测量结果。
扫描软件选项包括:
1、传统的接触式检测软件旨在与坐标测量机和其他接触式方法配合使用,非接触式扫描是新发展的技术
2、专为 3D 扫描设计的扫描原生检测软件
与传统 CMM 软件相比,扫描原生软件具有一些重要优势,因为它专为现代高分辨率 3D 扫描而成型。这些软件有这些功能:
1、更快、更轻松地处理大型数据集
2、通过用于噪声过滤和几何拟合的扫描本机算法实现高精度
3、通过横截面、边界、曲线、轮廓和虚拟边缘比较来检测偏差
4、通过自动识别 3D 扫描中的特征并智能过滤数据来加速 GD&T 计算
5、创建包含完整测量历史记录及其趋势的数字档案
例如Geomagic Control X是 Oqton 的扫描原生计量软件。它与任何光学扫描仪或便携式 CMM 臂集成,收集和分析非常大的数据集,并自动执行重复和复杂的任务,因此用户只需很少或没有培训即可获得准确的结果。对于许多增材制造企业来说,它是质量控制和检测中 3D 扫描的理想起点。
为高效的增材制造质量控制和检查做好准备
无论您采取什么方式,用于质量控制和检查的 3D 扫描都是增材制造从原型设计到大规模生产的关键一步。通过简化检查流程,3D扫描可帮助制造企业节省时间、更轻松地执行高级分析并更准确地检测问题。
最重要的是,高保真3D检测为增材制造企业提供了数据,以建立复杂零件的质量控制标准,并确保这些零件满足性能和合规性期望,即使是最苛刻和高度监管的行业。
扫二维码用手机看
最新消息
ZEISS 三维扫描仪 | 3D打印 普立得科技
普立得科技成立于2004年,专注于工业级3D打印机与三维扫描,同时我们也是ZEISS GOM代理商,并提供3D打印及扫描的代工整合服务,特此加值整合相关软体,包含拓扑优化设计 、医疗影像分析、逆向工程 、3D检测等,期望推进积层制造的使用习惯为生产带来更多价值。





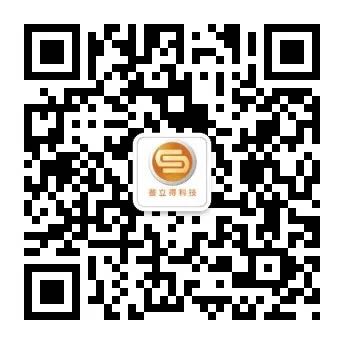
微信公众号
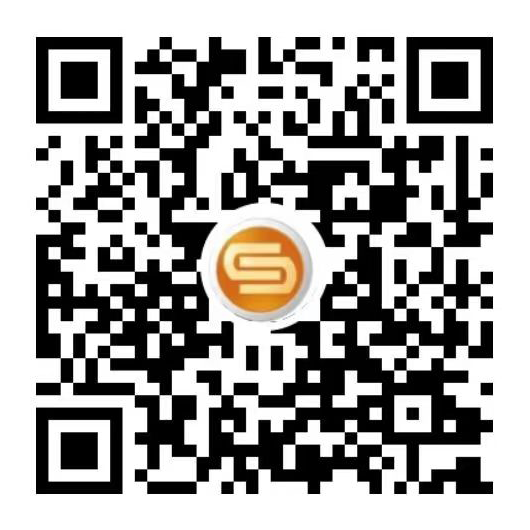
视频号
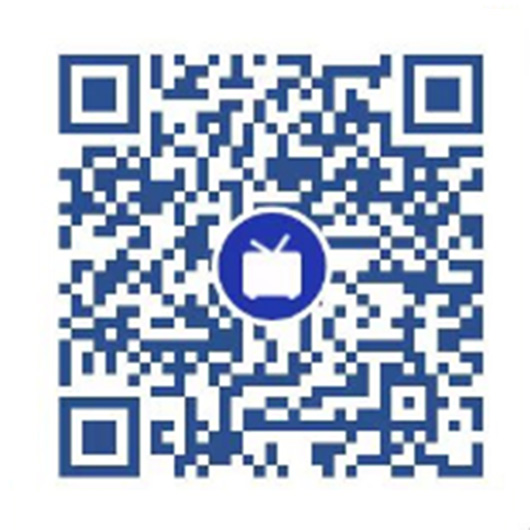
哔哩哔哩
您有什么疑问,或想咨询我们的产品与服务,请留下信息,我们会及时与您联系!
© 2021 普立得科技有限公司 All Rights Reserved 粤ICP备19059200号