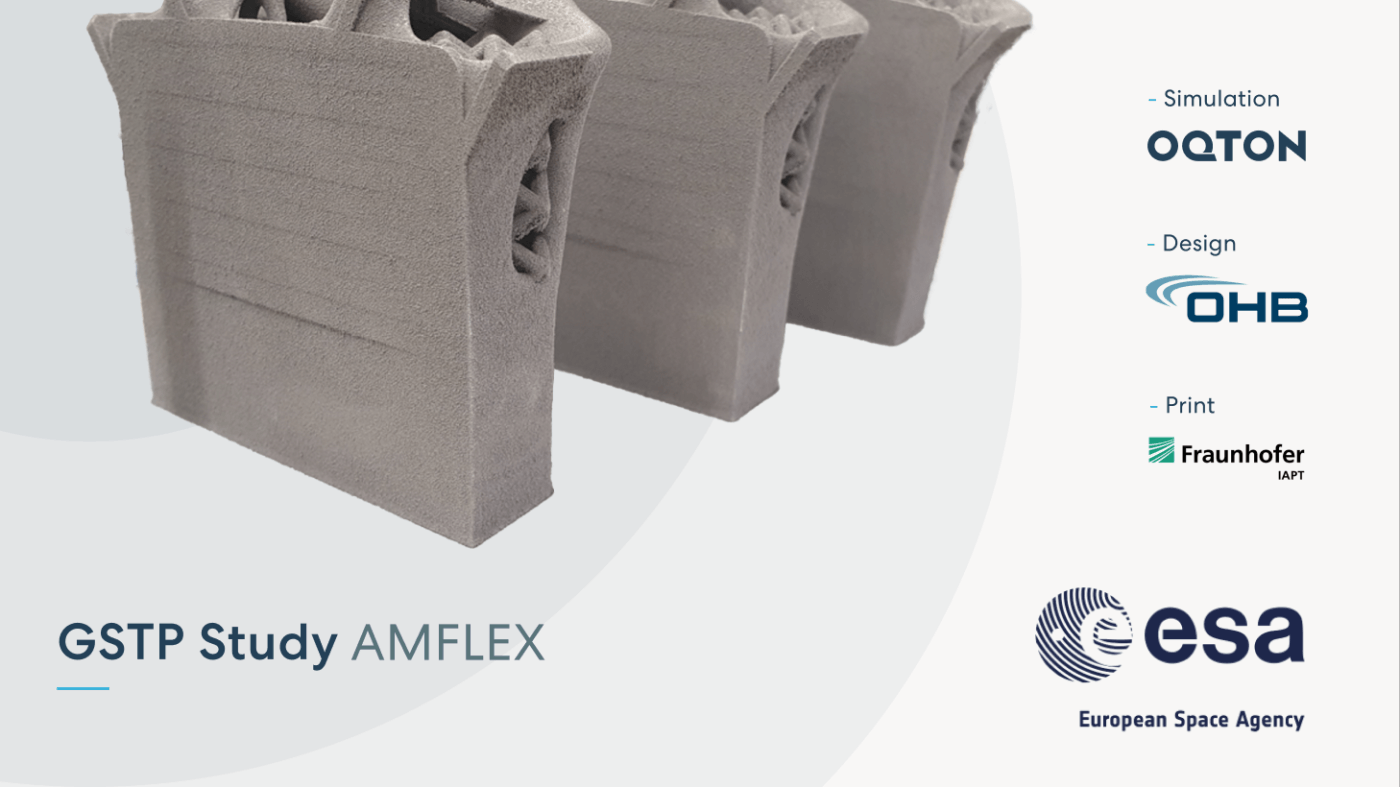
欧洲航天器专家与 Oqton 合作改进应力收缩线预测技术并减少计算时间
发布时间:2023/07/11
- 访问量:
【概要描述】
在欧洲航天工业中,政府和私人机构通过工程独创性和开拓精神正在努力实现一个共同目标——太空技术的进步。增材制造为该领域提供了许多优势,系统集成商已经使用它来生产优化的零件,甚至火箭内的大型部件。
然而,在航空航天领域推广增材制造技术,仍然需要克服工艺难题和零件特定的难点。 Oqton 的金属增材制造仿真技术帮助制造商能够预测称为应力收缩线的微变形位置和严重程度,从而使推动行业向前迈了结实、稳住的一小步。
除了增材制造零件的宏观过程引起的变形之外,其表面上还可能出现细小的水平变形。这种现象没有正式名称,但通常被称为收缩线或应力收缩线。
在欧洲航天局资助的一个项目中,Oqton、OHB SE 和 Fraunhofer IAPT 之间的合作改进了增材制造的收缩线预测。
如果制造商知道线条将出现在哪里,通过设计优化、工艺改进则可以避免或改善此问题,比如,修改设计以防止形成收缩线或将其重新远离关键点的位置。这些调整中的任何一个都将通过消除不必要的打印迭代,从而减少时间和节约材料。
Oqton 的
增材制造工艺仿真专家团队
与欧洲航天工业系统集成商 OHB SE 和增材制造技术研究机构 Fraunhofer IAPT 合作,在欧洲航天局(欧空局)资助的一个项目中改进了收缩线预测技术。
OHB System AG 是 OHB SE 的子公司,致力于探索航天器和卫星的新技术。他们七年前开始从事增材制造工作,并在外部供应链的支持下迅速在该领域积累了深厚的经验。
OHB 是 AMFLEX 的主要合作伙伴,该项目旨在开发和改进 3D 打印挠性部件的设计和制造工艺。 AMFLEX 是 ESA 通用支持技术计划(GSTP 合同号 4000138069/22/NL/KML)的一部分,该计划通过开发未来太空任务所需的技术、专业知识和能力,将工程概念转化为可用产品。
收缩线在光学机械零件中尤其成问题,它们会引起表面误差,从而导致零件质量严重下降。由于 OHB 正在开发用于光学仪器的 3D 打印镜子,因此这是一个通过过程模拟解决问题的好机会。
“该项目的首要任务之一是找出 Oqton 的模拟技术需要进行哪些改进,以便我们将光学仪器安装在轻薄、3D 打印零件上,”增材制造的 Marco Mulser OHB System AG 的协调员解释道。 “其次,我们希望 Oqton 实现这些增强功能并用在实际零件上进行测试。”
OHB 计划将 Oqton 的收缩线预测技术纳入他们将作为 AMFLEX 一部分创建的光机械组件的设计中。 Mulser 补充道:“我们将使用 Oqton 的打印模拟来预先计算收缩线,以适应镜子的设计,并将收缩线放置在对光学性能影响轻微的地方。”
收缩线本质上代表凹口或尖锐的凹槽。在快速模拟中很难准确地捕捉宏观和微观层面上促成其形成的不同机制,但我们知道它们会降低零件的尺寸精度,并且是潜在的故障点。铝和铜——航空航天应用中使用的两种主要材料——特别容易发生这种类型的变形。
变形在金属增材制造中很常见,现有的仿真工具(例如 Oqton 的 Amphyon 和 3DXpert)可以很好地预测和补偿它们。然而,由于收缩线的尺寸较大,用标准方法更难处理。
通常的解决方案是在后处理过程中进行打磨、抛光,但这会带来巨大的额外成本,有时需要牺牲零件的功能性才能解决收缩线问题。
AMFLEX 联盟在之前项目中的零件的一部分上测试了收缩线模拟。他们模拟了打印平台上同一部件的三个不同方向,发现改变角度可以有效减少收缩线的影响。 IAPT 打印的测试部件与模拟预测有着令人印象深刻的相似之处。
改变打印平台上零件的角度可以减少收缩线的影响
减少计算时间
作为 AMFLEX 项目的一部分,Oqton 团队还减少了模拟算法内核 Amphyon 的计算时间,显着提高了效率。
在过程模拟中,通过将复杂对象划分为更小的部分来创建称为有限元网格。网格的数量决定了模拟的计算量。
有时,零件的体积很大,例如 10,000 cm3,但厚度却只有 0.4 毫米。将整个零件划分为边长为 0.4 毫米的有限元,将导致在过程模拟的每个阶段需要求解超过 1.56 亿个有限元和超过 4.68 亿个方程。模拟此类数值问题需要大量的计算工作和时间。
为了确保快速模拟,网格内有限元的总数应尽可能小,单元数应尽可能大。另一方面,零件的某些区域(例如薄壁)需要更小的单元来保留高度的细节和精度。
有限元网格通常组合不同尺寸的元素。这种自适应网格划分是模拟中的标准程序,并且从一开始就在 Oqton 的模拟引擎中实现。 Oqton 团队在 AMFLEX 期间取得的成果是增强了网格生成的适应性。
目标始终是在计算工作量和模拟精度之间取得平衡。我们希望进行高度详细的计算,这将改善流程结果,并在设计迭代和流程准备期间节省尽可能多的时间。
Oqton 在 LPBF 制造的测试部件上应用了这种新方法,取得了令人印象深刻的结果。在第一次测试中,与之前使用的自适应方法相比,改进的网格划分功能将单元数量从 63 万个减少到 42 万个,计算时间惊人地减少了 40%。
Oqton 减少了模拟内核 Amphyon 的计算时间
Next
计算时间的缩短和收缩线预测的改进将在 AMFLEX 项目的下一阶段发挥重要作用。 OHB 和项目合作伙伴 Fraunhofer IAPT 将使用它来设计用于航天器仪器的新型光学机械组件。
“AMFLEX 中要开发的镜子是测试模拟技术的绝佳候选者。它既具有精致的结构,例如集成安装特征上的薄壁,可以使用标准网格参数制成,也具有粗片段,其中粗网格可能更合适。这种组合将使计算时间大大缩短。”Mulser 总结道。
源文摘自:Opton
欧洲航天器专家与 Oqton 合作改进应力收缩线预测技术并减少计算时间
【概要描述】
在欧洲航天工业中,政府和私人机构通过工程独创性和开拓精神正在努力实现一个共同目标——太空技术的进步。增材制造为该领域提供了许多优势,系统集成商已经使用它来生产优化的零件,甚至火箭内的大型部件。
然而,在航空航天领域推广增材制造技术,仍然需要克服工艺难题和零件特定的难点。 Oqton 的金属增材制造仿真技术帮助制造商能够预测称为应力收缩线的微变形位置和严重程度,从而使推动行业向前迈了结实、稳住的一小步。
除了增材制造零件的宏观过程引起的变形之外,其表面上还可能出现细小的水平变形。这种现象没有正式名称,但通常被称为收缩线或应力收缩线。
在欧洲航天局资助的一个项目中,Oqton、OHB SE 和 Fraunhofer IAPT 之间的合作改进了增材制造的收缩线预测。
如果制造商知道线条将出现在哪里,通过设计优化、工艺改进则可以避免或改善此问题,比如,修改设计以防止形成收缩线或将其重新远离关键点的位置。这些调整中的任何一个都将通过消除不必要的打印迭代,从而减少时间和节约材料。
Oqton 的
增材制造工艺仿真专家团队
与欧洲航天工业系统集成商 OHB SE 和增材制造技术研究机构 Fraunhofer IAPT 合作,在欧洲航天局(欧空局)资助的一个项目中改进了收缩线预测技术。
OHB System AG 是 OHB SE 的子公司,致力于探索航天器和卫星的新技术。他们七年前开始从事增材制造工作,并在外部供应链的支持下迅速在该领域积累了深厚的经验。
OHB 是 AMFLEX 的主要合作伙伴,该项目旨在开发和改进 3D 打印挠性部件的设计和制造工艺。 AMFLEX 是 ESA 通用支持技术计划(GSTP 合同号 4000138069/22/NL/KML)的一部分,该计划通过开发未来太空任务所需的技术、专业知识和能力,将工程概念转化为可用产品。
收缩线在光学机械零件中尤其成问题,它们会引起表面误差,从而导致零件质量严重下降。由于 OHB 正在开发用于光学仪器的 3D 打印镜子,因此这是一个通过过程模拟解决问题的好机会。
“该项目的首要任务之一是找出 Oqton 的模拟技术需要进行哪些改进,以便我们将光学仪器安装在轻薄、3D 打印零件上,”增材制造的 Marco Mulser OHB System AG 的协调员解释道。 “其次,我们希望 Oqton 实现这些增强功能并用在实际零件上进行测试。”
OHB 计划将 Oqton 的收缩线预测技术纳入他们将作为 AMFLEX 一部分创建的光机械组件的设计中。 Mulser 补充道:“我们将使用 Oqton 的打印模拟来预先计算收缩线,以适应镜子的设计,并将收缩线放置在对光学性能影响轻微的地方。”
收缩线本质上代表凹口或尖锐的凹槽。在快速模拟中很难准确地捕捉宏观和微观层面上促成其形成的不同机制,但我们知道它们会降低零件的尺寸精度,并且是潜在的故障点。铝和铜——航空航天应用中使用的两种主要材料——特别容易发生这种类型的变形。
变形在金属增材制造中很常见,现有的仿真工具(例如 Oqton 的 Amphyon 和 3DXpert)可以很好地预测和补偿它们。然而,由于收缩线的尺寸较大,用标准方法更难处理。
通常的解决方案是在后处理过程中进行打磨、抛光,但这会带来巨大的额外成本,有时需要牺牲零件的功能性才能解决收缩线问题。
AMFLEX 联盟在之前项目中的零件的一部分上测试了收缩线模拟。他们模拟了打印平台上同一部件的三个不同方向,发现改变角度可以有效减少收缩线的影响。 IAPT 打印的测试部件与模拟预测有着令人印象深刻的相似之处。
改变打印平台上零件的角度可以减少收缩线的影响
减少计算时间
作为 AMFLEX 项目的一部分,Oqton 团队还减少了模拟算法内核 Amphyon 的计算时间,显着提高了效率。
在过程模拟中,通过将复杂对象划分为更小的部分来创建称为有限元网格。网格的数量决定了模拟的计算量。
有时,零件的体积很大,例如 10,000 cm3,但厚度却只有 0.4 毫米。将整个零件划分为边长为 0.4 毫米的有限元,将导致在过程模拟的每个阶段需要求解超过 1.56 亿个有限元和超过 4.68 亿个方程。模拟此类数值问题需要大量的计算工作和时间。
为了确保快速模拟,网格内有限元的总数应尽可能小,单元数应尽可能大。另一方面,零件的某些区域(例如薄壁)需要更小的单元来保留高度的细节和精度。
有限元网格通常组合不同尺寸的元素。这种自适应网格划分是模拟中的标准程序,并且从一开始就在 Oqton 的模拟引擎中实现。 Oqton 团队在 AMFLEX 期间取得的成果是增强了网格生成的适应性。
目标始终是在计算工作量和模拟精度之间取得平衡。我们希望进行高度详细的计算,这将改善流程结果,并在设计迭代和流程准备期间节省尽可能多的时间。
Oqton 在 LPBF 制造的测试部件上应用了这种新方法,取得了令人印象深刻的结果。在第一次测试中,与之前使用的自适应方法相比,改进的网格划分功能将单元数量从 63 万个减少到 42 万个,计算时间惊人地减少了 40%。
Oqton 减少了模拟内核 Amphyon 的计算时间
Next
计算时间的缩短和收缩线预测的改进将在 AMFLEX 项目的下一阶段发挥重要作用。 OHB 和项目合作伙伴 Fraunhofer IAPT 将使用它来设计用于航天器仪器的新型光学机械组件。
“AMFLEX 中要开发的镜子是测试模拟技术的绝佳候选者。它既具有精致的结构,例如集成安装特征上的薄壁,可以使用标准网格参数制成,也具有粗片段,其中粗网格可能更合适。这种组合将使计算时间大大缩短。”Mulser 总结道。
源文摘自:Opton
- 分类: 产业应用
- 发布时间:2023-07-11 15:15
- 访问量:
在欧洲航天工业中,政府和私人机构通过工程独创性和开拓精神正在努力实现一个共同目标——太空技术的进步。增材制造为该领域提供了许多优势,系统集成商已经使用它来生产优化的零件,甚至火箭内的大型部件。
然而,在航空航天领域推广增材制造技术,仍然需要克服工艺难题和零件特定的难点。 Oqton 的金属增材制造仿真技术帮助制造商能够预测称为应力收缩线的微变形位置和严重程度,从而使推动行业向前迈了结实、稳住的一小步。
除了增材制造零件的宏观过程引起的变形之外,其表面上还可能出现细小的水平变形。这种现象没有正式名称,但通常被称为收缩线或应力收缩线。
在欧洲航天局资助的一个项目中,Oqton、OHB SE 和 Fraunhofer IAPT 之间的合作改进了增材制造的收缩线预测。
如果制造商知道线条将出现在哪里,通过设计优化、工艺改进则可以避免或改善此问题,比如,修改设计以防止形成收缩线或将其重新远离关键点的位置。这些调整中的任何一个都将通过消除不必要的打印迭代,从而减少时间和节约材料。
Oqton 的增材制造工艺仿真专家团队与欧洲航天工业系统集成商 OHB SE 和增材制造技术研究机构 Fraunhofer IAPT 合作,在欧洲航天局(欧空局)资助的一个项目中改进了收缩线预测技术。
OHB System AG 是 OHB SE 的子公司,致力于探索航天器和卫星的新技术。他们七年前开始从事增材制造工作,并在外部供应链的支持下迅速在该领域积累了深厚的经验。
OHB 是 AMFLEX 的主要合作伙伴,该项目旨在开发和改进 3D 打印挠性部件的设计和制造工艺。 AMFLEX 是 ESA 通用支持技术计划(GSTP 合同号 4000138069/22/NL/KML)的一部分,该计划通过开发未来太空任务所需的技术、专业知识和能力,将工程概念转化为可用产品。
收缩线在光学机械零件中尤其成问题,它们会引起表面误差,从而导致零件质量严重下降。由于 OHB 正在开发用于光学仪器的 3D 打印镜子,因此这是一个通过过程模拟解决问题的好机会。
“该项目的首要任务之一是找出 Oqton 的模拟技术需要进行哪些改进,以便我们将光学仪器安装在轻薄、3D 打印零件上,”增材制造的 Marco Mulser OHB System AG 的协调员解释道。 “其次,我们希望 Oqton 实现这些增强功能并用在实际零件上进行测试。”
OHB 计划将 Oqton 的收缩线预测技术纳入他们将作为 AMFLEX 一部分创建的光机械组件的设计中。 Mulser 补充道:“我们将使用 Oqton 的打印模拟来预先计算收缩线,以适应镜子的设计,并将收缩线放置在对光学性能影响轻微的地方。”
收缩线本质上代表凹口或尖锐的凹槽。在快速模拟中很难准确地捕捉宏观和微观层面上促成其形成的不同机制,但我们知道它们会降低零件的尺寸精度,并且是潜在的故障点。铝和铜——航空航天应用中使用的两种主要材料——特别容易发生这种类型的变形。
变形在金属增材制造中很常见,现有的仿真工具(例如 Oqton 的 Amphyon 和 3DXpert)可以很好地预测和补偿它们。然而,由于收缩线的尺寸较大,用标准方法更难处理。
通常的解决方案是在后处理过程中进行打磨、抛光,但这会带来巨大的额外成本,有时需要牺牲零件的功能性才能解决收缩线问题。
AMFLEX 联盟在之前项目中的零件的一部分上测试了收缩线模拟。他们模拟了打印平台上同一部件的三个不同方向,发现改变角度可以有效减少收缩线的影响。 IAPT 打印的测试部件与模拟预测有着令人印象深刻的相似之处。
改变打印平台上零件的角度可以减少收缩线的影响
减少计算时间
作为 AMFLEX 项目的一部分,Oqton 团队还减少了模拟算法内核 Amphyon 的计算时间,显着提高了效率。
在过程模拟中,通过将复杂对象划分为更小的部分来创建称为有限元网格。网格的数量决定了模拟的计算量。
有时,零件的体积很大,例如 10,000 cm3,但厚度却只有 0.4 毫米。将整个零件划分为边长为 0.4 毫米的有限元,将导致在过程模拟的每个阶段需要求解超过 1.56 亿个有限元和超过 4.68 亿个方程。模拟此类数值问题需要大量的计算工作和时间。
为了确保快速模拟,网格内有限元的总数应尽可能小,单元数应尽可能大。另一方面,零件的某些区域(例如薄壁)需要更小的单元来保留高度的细节和精度。
有限元网格通常组合不同尺寸的元素。这种自适应网格划分是模拟中的标准程序,并且从一开始就在 Oqton 的模拟引擎中实现。 Oqton 团队在 AMFLEX 期间取得的成果是增强了网格生成的适应性。
目标始终是在计算工作量和模拟精度之间取得平衡。我们希望进行高度详细的计算,这将改善流程结果,并在设计迭代和流程准备期间节省尽可能多的时间。
Oqton 在 LPBF 制造的测试部件上应用了这种新方法,取得了令人印象深刻的结果。在第一次测试中,与之前使用的自适应方法相比,改进的网格划分功能将单元数量从 63 万个减少到 42 万个,计算时间惊人地减少了 40%。
Oqton 减少了模拟内核 Amphyon 的计算时间
Next
计算时间的缩短和收缩线预测的改进将在 AMFLEX 项目的下一阶段发挥重要作用。 OHB 和项目合作伙伴 Fraunhofer IAPT 将使用它来设计用于航天器仪器的新型光学机械组件。
“AMFLEX 中要开发的镜子是测试模拟技术的绝佳候选者。它既具有精致的结构,例如集成安装特征上的薄壁,可以使用标准网格参数制成,也具有粗片段,其中粗网格可能更合适。这种组合将使计算时间大大缩短。”Mulser 总结道。
源文摘自:Opton
扫二维码用手机看
最新消息
ZEISS 三维扫描仪 | 3D打印 普立得科技
普立得科技成立于2004年,专注于工业级3D打印机与三维扫描,同时我们也是ZEISS GOM代理商,并提供3D打印及扫描的代工整合服务,特此加值整合相关软体,包含拓扑优化设计 、医疗影像分析、逆向工程 、3D检测等,期望推进积层制造的使用习惯为生产带来更多价值。





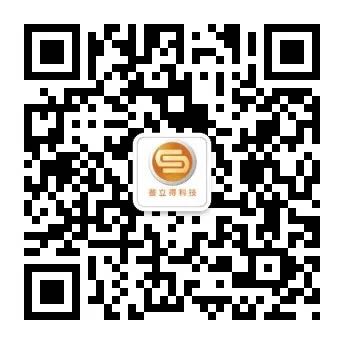
微信公众号
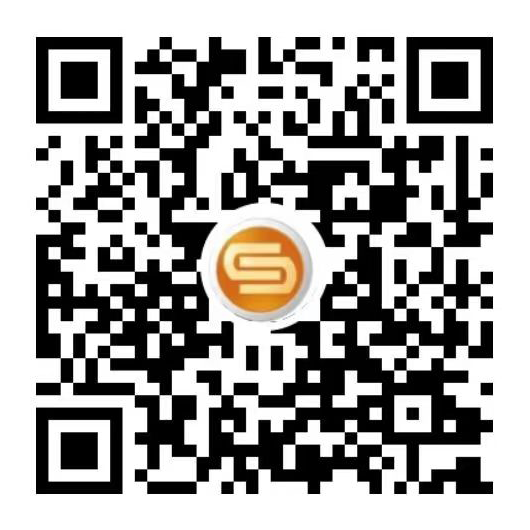
视频号
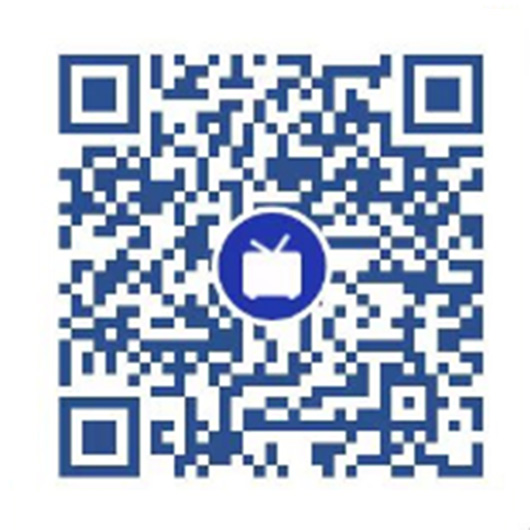
哔哩哔哩
您有什么疑问,或想咨询我们的产品与服务,请留下信息,我们会及时与您联系!
© 2021 普立得科技有限公司 All Rights Reserved 粤ICP备19059200号