
复合材料工具2.0的FDM设计指南(二)
发布时间:2023/04/24
- 访问量:
【概要描述】 第4节-后处理和零件制造
FDM工具的最终表面粗糙度由几何结构、层厚度和构建方向驱动。如前所述,竣工FDM复合材料工具具有固有的孔隙率和表面光洁度,这对于生产大多数应用的复合材料零件来说是不可接受的。对工具进行后处理可获得所需的表面光洁度并提供真空完整性。
可以使用多种方法来改善工具的表面粗糙度,包括手动磨损、介质喷砂和翻滚,所有这些方法都有优点和缺点。目前满足表面光洁度要求并提供真空完整性的最佳实践是手动磨损,然后使用环氧树脂密封剂。工具使用双作用轨道砂光机手动打磨,砂纸粒度从120到800不等,逐渐变细。工具密封由两部分环氧树脂完成或者环氧薄膜粘合剂,尽管根据应用,也可以使用其他材料(例如,粘合剂背衬的FEP薄膜和类似材料)。
制备和密封FDM复合材料工具的最合适材料和方法将由应用决定。有关迄今为止使用的最常见密封材料的其他信息,请参阅以下小节。
环氧树脂密封剂
密封FDM工具最常见的方法是使用环氧树脂密封剂。这些材料几乎适用于所有的工具形状,并为表面装袋提供所需的真空完整性。有许多环氧树脂材料可以有效工作。应选择能够承受所需固化温度以及工具预期寿命的材料。还应评估它们与所选FDM材料的兼容性(如附着力)。
Stratasys主要使用来自BJB Enterprises的TC-1614两部分环氧树脂。它在室温下具有理想的低粘度,在工具表面上均匀分布,同时也渗透到工具材料层中。然而,工具寿命评估的热循环表明,TC-1614和其他常见的环氧树脂通常在350°F(177°C)的含氧环境中经过大约30次固化循环后会氧化和分解。信封装袋和/或在惰性环境中固化应显著延长用高温环氧树脂密封的工具的寿命。评估更适合在350°F(177°C)固化温度正在进行中;结果将在随后的设计指南发布中提供。
使用两部分环氧树脂(如TC-1614)密封工具的程序见附录B。
使用环氧薄膜粘合剂也可以有效地进行工具密封(使用无支撑薄膜以避免在研磨/抛光过程中暴露载体材料)。同样,许多材料选项将发挥作用,包括3M公司的AF-163和AF-555。也可以考虑替代材料,并应根据承受连续暴露于所需固化温度的能力以及与所选FDM材料的兼容性进行评估。与环氧树脂浆料相比,薄膜粘合剂的主要优点是易于应用和确保均匀覆盖。
背胶膜
背胶FEP(和类似的)薄膜提供了环氧树脂密封材料的替代品。多年来,航空航天原始设备制造商一直使用Airtech的Tooltec CS5和Toolwright 5等薄膜,为传统材料和工艺制成的工具提供有效的铺层和脱模表面。这种薄膜最适合于具有最小和逐渐复杂轮廓的相对简单和平坦的工具形状,因为它们表现出最小的伸长率。FEP薄膜在损失之前也被限制在相对较低体积的零件上
由于刻痕、撕裂和对工具的粘附而产生的有效性。它们最理想的一个应用是维修工具,因为它们可以在没有任何工具打磨的情况下使用,而且维修工具的零件体积往往是个位数。请注意,用背胶膜密封的工具必须采用信封装袋,因为除非与其他密封方法相结合,否则对此类薄膜进行表面装袋是无效的。
表面光洁度结果
下图4-1显示了竣工FDM表面的最终表面光洁度,用无砂涂的背胶膜(Tooltec CS5)密封的工具,手动砂涂后用背胶膜密封的工具和用环氧树脂密封的手动磨损工具。复合材料刀具最常见的表面光洁度要求也显示出来进行比较(64µin(1.6µm),Ra)。可以看出,用于密封FDM复合材料工具的常用方法产生的表面光洁度比典型要求要平滑得多。
图4-1:常见FDM后处理技术产生的表面粗糙度。
第5节-工具寿命和特性数据
在设计指南开发过程中进行了广泛的测试和表征,以验证FDM复合材料工具的性能。测试包括对溶剂暴露、放气(以验证是否缺乏潜在污染物)、水分暴露、精度和热稳定性的评估,以及对工具寿命的初步评估。以下小节提供了评估总结和主要结果。所有测试都是在ULTEM 1010树脂中生产的工具或测试试样上进行的。
精度和热稳定性
为了评估准确性和稳定性,在热循环前后对多种工具进行了评估。生产了三种工具设计,构建风格(外壳与稀疏)和尺寸各不相同,共有五种变体(见图5-1)。这些工具被送往外部检查机构进行精确的3D扫描。使用具有SLP 300激光头(来自laser Design)的Platinum FaroArm(来自FARO Technologies)。使用PolyWorks View 3D计量将扫描数据与每个工具变体的CAD模型进行比较软件(来自Innovametric)。
用于该评估的复合工具在初始3D图像之前进行了后处理(研磨)。之所以选择这种配置,是因为几乎所有FDM复合材料工具都将经过这样的准备,从而使后处理工具的准确性成为最相关的数据。尽管操作员之间的后处理可能存在一些可变性,但材料的总量发现在磨损过程中去除的相当小(使用标准最佳实践),并且不代表总体尺寸变化的显著部分。
如上所述,工具在暴露于高温下之前进行扫描,然后进行热循环。对于循环,将工具真空装袋(信封装袋方案),加热至350°F(177°C),在全真空下保持温度两小时(最低),然后在两次循环之间降低至150°F(66°C)以下,总共连续10次烤箱循环。
3D扫描仪的精度为±0.0015英寸(0.0381 mm),FaroArm的精度也为±0.00115英寸(0.0381mm),总精度为±0.003英寸(0.076 mm)。此限制适用于扫描并与原始CAD数据进行比较的工具。为了将循环后的刀具几何结构与循环前的扫描数据进行比较,必须将精度汇总或“叠加”,从而导致精度限制为±0.006英寸(0.152 mm)
图5-1:用于热稳定性测试的工具设计(显示为打磨,但未密封)。
精度和热稳定性-结果
评估的代表性数据集如图5-2至5-5所示,用于打印示例工具和原始CAD模型数据之间的比较(无热循环)。如图5-2所示,扫描数据显示,外壳式工具的面积与模型相差约0.019英寸(0.482 mm),超过92%的工具在±0.015英寸(0.381 mm)范围内。对于这个特定的例子,超过该值的大部分区域都在EOP之外。作为参考,主题工具的尺寸约为14.5 x 10.5 x 4英寸(368.3 x 266.7 x 101.6毫米)。
对于与上述相同的示例工具几何结构,但以稀疏构建样式设计和打印,数据显示该工具的面积与模型的差异约为0.018英寸(0.457毫米),如图5-3所示。对于该工具,超过90%的工具在±0.015英寸(0.381 mm)范围内,同样,可以看出,变化较大的大多数区域位于EOP之外,并集中在工具的垂直面上。
图5-2:无人机风扇叶片工具(外壳式)的3D扫描数据,带有与原始CAD模型(无热循环)。尺寸单位为英寸。
图5-3:无人机风扇叶片工具(稀疏型)的3D扫描数据,带有与原始CAD模型(无热循环)的颜色图比较。尺寸单位为英寸。
图5-4和5-5显示了10次热循环后上述两种工具的扫描数据。可以看出,尺寸变化可以忽略不计,特别是考虑到±0.006英寸(0.152毫米)的精度限制。对于外壳工具,超过95%的工具表面在该限制范围内,对于稀疏工具,超过90%。计划对工具精度进行进一步调查,包括使用更精确的检测设备(如CMM),并将包括在未来的设计指南中。用于评估的工具正在进行额外的热循环。此外,特别是对于稀疏刀具,扫描数据显示刀具末端垂直表面的大部分变化。这是合法的变化,还是与扫描设备的限制有关,尚待验证。
图5-4:热循环后无人机风扇叶片工具(外壳式)的3D扫描数据,与3D的颜色图比较循环之前扫描相同工具的数据。尺寸单位为英寸。
图5-5:热循环后无人机风扇叶片工具(稀疏型)的3D扫描数据,与循环前相同工具的3D扫描结果进行颜色图比较。尺寸单位为英寸
高温机械财产
下图显示了在临界高温下进行机械测试的数据。图5-6显示了在不同温度下ZX方向上构建的样品压缩载荷的应力-应变曲线。该数据集由密苏里科技大学航空航天制造技术中心(CAMT)生成。根据ASTM D695进行压缩试验。
图5-7显示了在平面、边缘和垂直方向打印的样品在不同临界温度下的弯曲模量数据。根据ASTM D790程序A在外部实验室进行测试。图表显示,在350°F(177°C)的固化温度下,ULTEM 1010树脂的硬度降低了20-30%,这取决于印刷方向。
图5-6:ULTEM 1010树脂在不同温度下的应力-应变关系
图5-7:不同方向的临界温度下的弯曲模量。
水分敏感性
随着时间的推移,许多聚合物材料以不同的速率在一定程度上吸收水分。根据制造商(SABIC)的说法,ULTEM 1010树脂在75°F/50%RH(24°C/50%RH)下饱和时将吸收0.7%。由于水分可能对复合材料层压板的质量有害,因此进行了相对初步的测试,以确保可以通过基本的预防措施来防止这种不利影响。
为了确保饱和和“最坏情况”的暴露场景,将四个工具(外壳和稀疏结构各两个)放置在140°F/90%RH(60°C/90%)的湿度室中两周。调节后,随后将两个工具在250°F(121°C)下干燥4小时。然后在每个工具上生产八层准各向同性碳/环氧树脂层压板。固化后对层压板进行目视检查,然后切片进行显微镜检查,以检查孔隙率、分层、起泡和其他水分诱导效应的迹象。主要目的是证明即使在最恶劣的气候下,如果水分吸收成为一个令人担忧的问题,使用前烘干工具足以防止对固化零件产生不利影响。事实上,大多数处于正常使用状态的工具都可能存储在远没有测试过的环境那么恶劣的环境中。
正如预期的那样,水分暴露测试表明,使用前干燥的工具(在250°F(121°C)下4小时)可以生产出质量合格的层压板(没有明显的孔隙率或其他明显问题)。
溶剂暴露
对ULTEM 1010树脂试样(未密封)进行溶剂暴露测试,以验证其与复合材料制造设施中使用的最常见溶剂——异丙醇(IPA)、丙酮和甲乙酮(MEK)——的一般兼容性。在正常操作过程中,大多数复合材料工具只会短暂暴露于此类溶剂中,例如在零件制造前擦拭干净。为了证明总体兼容性,对溶剂洒在工具上并在相当于一个周末(约48小时)的时间内无人注意的情况进行了评估,以代表可能的最坏情况。将试样置于ULTEM 1010树脂中,然后将其浸入溶剂中48小时。暴露后,将样品从溶剂中取出,并在250°F(121°C)下烘干两小时,以确保残留溶剂蒸发。弯曲强度(三点弯曲设置)根据ASTM D 790测定,并与基线数据(无溶剂暴露)进行比较。
干燥后,暴露试样的弯曲强度恢复到相对于基准试样的完全强度,这证实了如果溶剂从工具中蒸发,最终性能不会受到影响。在实际制造使用过程中,工具通常只会短暂地暴露在少量溶剂中,在这种情况下,预计不会发生性能变化。工具也将密封在最有可能暴露于溶剂的表面,这将增加额外的保护和安全级别。
工具寿命
对非金属工具的使用寿命有一个全面的了解是至关重要的,特别是对于生产工具的考虑,或者对于原型之外的任何大量零件来说。由于所涉及的时间和资源,通过实验获得信息也是具有挑战性的。在建立初步基线的过程中,收集了实际(经验)和分析数据。
对于经验测试,遵循了前面描述的精度和热稳定性测试的基本方法,但扩展到了更多的热循环。测试了两种主要的外壳式和稀疏式结构中构建的单一工具几何结构(无人机风扇叶片)(工具如图5-1所示)。工具在350°F(177°F)、全真空、仅烤箱下循环30、60和90次,然后进行评估(检查和3D扫描)和层压板制造(八层、准各向同性碳/环氧树脂),随后进行检查。
对于分析部分,使用动态力学分析(DMA)来评估弯曲试样(三点弯曲配置)的蠕变。在100 psi(689 kPa)
复合材料工具2.0的FDM设计指南(二)
【概要描述】 第4节-后处理和零件制造
FDM工具的最终表面粗糙度由几何结构、层厚度和构建方向驱动。如前所述,竣工FDM复合材料工具具有固有的孔隙率和表面光洁度,这对于生产大多数应用的复合材料零件来说是不可接受的。对工具进行后处理可获得所需的表面光洁度并提供真空完整性。
可以使用多种方法来改善工具的表面粗糙度,包括手动磨损、介质喷砂和翻滚,所有这些方法都有优点和缺点。目前满足表面光洁度要求并提供真空完整性的最佳实践是手动磨损,然后使用环氧树脂密封剂。工具使用双作用轨道砂光机手动打磨,砂纸粒度从120到800不等,逐渐变细。工具密封由两部分环氧树脂完成或者环氧薄膜粘合剂,尽管根据应用,也可以使用其他材料(例如,粘合剂背衬的FEP薄膜和类似材料)。
制备和密封FDM复合材料工具的最合适材料和方法将由应用决定。有关迄今为止使用的最常见密封材料的其他信息,请参阅以下小节。
环氧树脂密封剂
密封FDM工具最常见的方法是使用环氧树脂密封剂。这些材料几乎适用于所有的工具形状,并为表面装袋提供所需的真空完整性。有许多环氧树脂材料可以有效工作。应选择能够承受所需固化温度以及工具预期寿命的材料。还应评估它们与所选FDM材料的兼容性(如附着力)。
Stratasys主要使用来自BJB Enterprises的TC-1614两部分环氧树脂。它在室温下具有理想的低粘度,在工具表面上均匀分布,同时也渗透到工具材料层中。然而,工具寿命评估的热循环表明,TC-1614和其他常见的环氧树脂通常在350°F(177°C)的含氧环境中经过大约30次固化循环后会氧化和分解。信封装袋和/或在惰性环境中固化应显著延长用高温环氧树脂密封的工具的寿命。评估更适合在350°F(177°C)固化温度正在进行中;结果将在随后的设计指南发布中提供。
使用两部分环氧树脂(如TC-1614)密封工具的程序见附录B。
使用环氧薄膜粘合剂也可以有效地进行工具密封(使用无支撑薄膜以避免在研磨/抛光过程中暴露载体材料)。同样,许多材料选项将发挥作用,包括3M公司的AF-163和AF-555。也可以考虑替代材料,并应根据承受连续暴露于所需固化温度的能力以及与所选FDM材料的兼容性进行评估。与环氧树脂浆料相比,薄膜粘合剂的主要优点是易于应用和确保均匀覆盖。
背胶膜
背胶FEP(和类似的)薄膜提供了环氧树脂密封材料的替代品。多年来,航空航天原始设备制造商一直使用Airtech的Tooltec CS5和Toolwright 5等薄膜,为传统材料和工艺制成的工具提供有效的铺层和脱模表面。这种薄膜最适合于具有最小和逐渐复杂轮廓的相对简单和平坦的工具形状,因为它们表现出最小的伸长率。FEP薄膜在损失之前也被限制在相对较低体积的零件上
由于刻痕、撕裂和对工具的粘附而产生的有效性。它们最理想的一个应用是维修工具,因为它们可以在没有任何工具打磨的情况下使用,而且维修工具的零件体积往往是个位数。请注意,用背胶膜密封的工具必须采用信封装袋,因为除非与其他密封方法相结合,否则对此类薄膜进行表面装袋是无效的。
表面光洁度结果
下图4-1显示了竣工FDM表面的最终表面光洁度,用无砂涂的背胶膜(Tooltec CS5)密封的工具,手动砂涂后用背胶膜密封的工具和用环氧树脂密封的手动磨损工具。复合材料刀具最常见的表面光洁度要求也显示出来进行比较(64µin(1.6µm),Ra)。可以看出,用于密封FDM复合材料工具的常用方法产生的表面光洁度比典型要求要平滑得多。
图4-1:常见FDM后处理技术产生的表面粗糙度。
第5节-工具寿命和特性数据
在设计指南开发过程中进行了广泛的测试和表征,以验证FDM复合材料工具的性能。测试包括对溶剂暴露、放气(以验证是否缺乏潜在污染物)、水分暴露、精度和热稳定性的评估,以及对工具寿命的初步评估。以下小节提供了评估总结和主要结果。所有测试都是在ULTEM 1010树脂中生产的工具或测试试样上进行的。
精度和热稳定性
为了评估准确性和稳定性,在热循环前后对多种工具进行了评估。生产了三种工具设计,构建风格(外壳与稀疏)和尺寸各不相同,共有五种变体(见图5-1)。这些工具被送往外部检查机构进行精确的3D扫描。使用具有SLP 300激光头(来自laser Design)的Platinum FaroArm(来自FARO Technologies)。使用PolyWorks View 3D计量将扫描数据与每个工具变体的CAD模型进行比较软件(来自Innovametric)。
用于该评估的复合工具在初始3D图像之前进行了后处理(研磨)。之所以选择这种配置,是因为几乎所有FDM复合材料工具都将经过这样的准备,从而使后处理工具的准确性成为最相关的数据。尽管操作员之间的后处理可能存在一些可变性,但材料的总量发现在磨损过程中去除的相当小(使用标准最佳实践),并且不代表总体尺寸变化的显著部分。
如上所述,工具在暴露于高温下之前进行扫描,然后进行热循环。对于循环,将工具真空装袋(信封装袋方案),加热至350°F(177°C),在全真空下保持温度两小时(最低),然后在两次循环之间降低至150°F(66°C)以下,总共连续10次烤箱循环。
3D扫描仪的精度为±0.0015英寸(0.0381 mm),FaroArm的精度也为±0.00115英寸(0.0381mm),总精度为±0.003英寸(0.076 mm)。此限制适用于扫描并与原始CAD数据进行比较的工具。为了将循环后的刀具几何结构与循环前的扫描数据进行比较,必须将精度汇总或“叠加”,从而导致精度限制为±0.006英寸(0.152 mm)
图5-1:用于热稳定性测试的工具设计(显示为打磨,但未密封)。
精度和热稳定性-结果
评估的代表性数据集如图5-2至5-5所示,用于打印示例工具和原始CAD模型数据之间的比较(无热循环)。如图5-2所示,扫描数据显示,外壳式工具的面积与模型相差约0.019英寸(0.482 mm),超过92%的工具在±0.015英寸(0.381 mm)范围内。对于这个特定的例子,超过该值的大部分区域都在EOP之外。作为参考,主题工具的尺寸约为14.5 x 10.5 x 4英寸(368.3 x 266.7 x 101.6毫米)。
对于与上述相同的示例工具几何结构,但以稀疏构建样式设计和打印,数据显示该工具的面积与模型的差异约为0.018英寸(0.457毫米),如图5-3所示。对于该工具,超过90%的工具在±0.015英寸(0.381 mm)范围内,同样,可以看出,变化较大的大多数区域位于EOP之外,并集中在工具的垂直面上。
图5-2:无人机风扇叶片工具(外壳式)的3D扫描数据,带有与原始CAD模型(无热循环)。尺寸单位为英寸。
图5-3:无人机风扇叶片工具(稀疏型)的3D扫描数据,带有与原始CAD模型(无热循环)的颜色图比较。尺寸单位为英寸。
图5-4和5-5显示了10次热循环后上述两种工具的扫描数据。可以看出,尺寸变化可以忽略不计,特别是考虑到±0.006英寸(0.152毫米)的精度限制。对于外壳工具,超过95%的工具表面在该限制范围内,对于稀疏工具,超过90%。计划对工具精度进行进一步调查,包括使用更精确的检测设备(如CMM),并将包括在未来的设计指南中。用于评估的工具正在进行额外的热循环。此外,特别是对于稀疏刀具,扫描数据显示刀具末端垂直表面的大部分变化。这是合法的变化,还是与扫描设备的限制有关,尚待验证。
图5-4:热循环后无人机风扇叶片工具(外壳式)的3D扫描数据,与3D的颜色图比较循环之前扫描相同工具的数据。尺寸单位为英寸。
图5-5:热循环后无人机风扇叶片工具(稀疏型)的3D扫描数据,与循环前相同工具的3D扫描结果进行颜色图比较。尺寸单位为英寸
高温机械财产
下图显示了在临界高温下进行机械测试的数据。图5-6显示了在不同温度下ZX方向上构建的样品压缩载荷的应力-应变曲线。该数据集由密苏里科技大学航空航天制造技术中心(CAMT)生成。根据ASTM D695进行压缩试验。
图5-7显示了在平面、边缘和垂直方向打印的样品在不同临界温度下的弯曲模量数据。根据ASTM D790程序A在外部实验室进行测试。图表显示,在350°F(177°C)的固化温度下,ULTEM 1010树脂的硬度降低了20-30%,这取决于印刷方向。
图5-6:ULTEM 1010树脂在不同温度下的应力-应变关系
图5-7:不同方向的临界温度下的弯曲模量。
水分敏感性
随着时间的推移,许多聚合物材料以不同的速率在一定程度上吸收水分。根据制造商(SABIC)的说法,ULTEM 1010树脂在75°F/50%RH(24°C/50%RH)下饱和时将吸收0.7%。由于水分可能对复合材料层压板的质量有害,因此进行了相对初步的测试,以确保可以通过基本的预防措施来防止这种不利影响。
为了确保饱和和“最坏情况”的暴露场景,将四个工具(外壳和稀疏结构各两个)放置在140°F/90%RH(60°C/90%)的湿度室中两周。调节后,随后将两个工具在250°F(121°C)下干燥4小时。然后在每个工具上生产八层准各向同性碳/环氧树脂层压板。固化后对层压板进行目视检查,然后切片进行显微镜检查,以检查孔隙率、分层、起泡和其他水分诱导效应的迹象。主要目的是证明即使在最恶劣的气候下,如果水分吸收成为一个令人担忧的问题,使用前烘干工具足以防止对固化零件产生不利影响。事实上,大多数处于正常使用状态的工具都可能存储在远没有测试过的环境那么恶劣的环境中。
正如预期的那样,水分暴露测试表明,使用前干燥的工具(在250°F(121°C)下4小时)可以生产出质量合格的层压板(没有明显的孔隙率或其他明显问题)。
溶剂暴露
对ULTEM 1010树脂试样(未密封)进行溶剂暴露测试,以验证其与复合材料制造设施中使用的最常见溶剂——异丙醇(IPA)、丙酮和甲乙酮(MEK)——的一般兼容性。在正常操作过程中,大多数复合材料工具只会短暂暴露于此类溶剂中,例如在零件制造前擦拭干净。为了证明总体兼容性,对溶剂洒在工具上并在相当于一个周末(约48小时)的时间内无人注意的情况进行了评估,以代表可能的最坏情况。将试样置于ULTEM 1010树脂中,然后将其浸入溶剂中48小时。暴露后,将样品从溶剂中取出,并在250°F(121°C)下烘干两小时,以确保残留溶剂蒸发。弯曲强度(三点弯曲设置)根据ASTM D 790测定,并与基线数据(无溶剂暴露)进行比较。
干燥后,暴露试样的弯曲强度恢复到相对于基准试样的完全强度,这证实了如果溶剂从工具中蒸发,最终性能不会受到影响。在实际制造使用过程中,工具通常只会短暂地暴露在少量溶剂中,在这种情况下,预计不会发生性能变化。工具也将密封在最有可能暴露于溶剂的表面,这将增加额外的保护和安全级别。
工具寿命
对非金属工具的使用寿命有一个全面的了解是至关重要的,特别是对于生产工具的考虑,或者对于原型之外的任何大量零件来说。由于所涉及的时间和资源,通过实验获得信息也是具有挑战性的。在建立初步基线的过程中,收集了实际(经验)和分析数据。
对于经验测试,遵循了前面描述的精度和热稳定性测试的基本方法,但扩展到了更多的热循环。测试了两种主要的外壳式和稀疏式结构中构建的单一工具几何结构(无人机风扇叶片)(工具如图5-1所示)。工具在350°F(177°F)、全真空、仅烤箱下循环30、60和90次,然后进行评估(检查和3D扫描)和层压板制造(八层、准各向同性碳/环氧树脂),随后进行检查。
对于分析部分,使用动态力学分析(DMA)来评估弯曲试样(三点弯曲配置)的蠕变。在100 psi(689 kPa)
- 分类: 售后技术支持
- 发布时间:2023-04-24 14:14
- 访问量:
第4节-后处理和零件制造
FDM工具的最终表面粗糙度由几何结构、层厚度和构建方向驱动。如前所述,竣工FDM复合材料工具具有固有的孔隙率和表面光洁度,这对于生产大多数应用的复合材料零件来说是不可接受的。对工具进行后处理可获得所需的表面光洁度并提供真空完整性。
可以使用多种方法来改善工具的表面粗糙度,包括手动磨损、介质喷砂和翻滚,所有这些方法都有优点和缺点。目前满足表面光洁度要求并提供真空完整性的最佳实践是手动磨损,然后使用环氧树脂密封剂。工具使用双作用轨道砂光机手动打磨,砂纸粒度从120到800不等,逐渐变细。工具密封由两部分环氧树脂完成或者环氧薄膜粘合剂,尽管根据应用,也可以使用其他材料(例如,粘合剂背衬的FEP薄膜和类似材料)。
准备和密封FDM复合材料工具的最合适材料和方法将由应用决定。有关迄今为止使用的最常见密封材料的其他信息,请参阅以下小节。
环氧树脂密封剂
密封FDM工具最常见的方法是使用环氧树脂密封剂。这些材料几乎适用于所有的工具形状,并为表面装袋提供所需的真空完整性。有许多环氧树脂材料可以有效工作。应选择能够承受所需固化温度以及工具预期寿命的材料。还应评估它们与所选FDM材料的兼容性(如附着力)。
Stratasys主要使用来自BJB Enterprises的TC-1614两部分环氧树脂。它在室温下具有理想的低粘度,在工具表面上均匀分布,同时也渗透到工具材料层中。然而,工具寿命评估的热循环表明,TC-1614和其他常见的环氧树脂通常在350°F(177°C)的含氧环境中经过大约30次固化循环后会氧化和分解。信封装袋和/或在惰性环境中固化应显著延长用高温环氧树脂密封的工具的寿命。评估更适合在350°F(177°C)固化温度正在进行中;结果将在随后的设计指南发布中提供。
使用两部分环氧树脂(如TC-1614)密封工具的程序见附录B。
使用环氧薄膜粘合剂也可以有效地进行工具密封(使用无支撑薄膜以避免在研磨/抛光过程中暴露载体材料)。同样,许多材料选项将发挥作用,包括3M公司的AF-163和AF-555。也可以考虑替代材料,并应根据承受连续暴露于所需固化温度的能力以及与所选FDM材料的兼容性进行评估。与环氧树脂浆料相比,薄膜粘合剂的主要优点是易于应用和确保均匀覆盖。
背胶膜
背胶FEP(和类似的)薄膜提供了环氧树脂密封材料的替代品。多年来,航空航天原始设备制造商一直使用Airtech的Tooltec CS5和Toolwright 5等薄膜,为传统材料和工艺制成的工具提供有效的铺层和脱模表面。这种薄膜最适合于具有最小和逐渐复杂轮廓的相对简单和平坦的工具形状,因为它们表现出最小的伸长率。FEP薄膜在损失之前也被限制在相对较低体积的零件上
由于刻痕、撕裂和对工具的粘附而产生的有效性。它们最理想的一个应用是维修工具,因为它们可以在没有任何工具打磨的情况下使用,而且维修工具的零件体积往往是个位数。请注意,用背胶膜密封的工具必须采用信封装袋,因为除非与其他密封方法相结合,否则对此类薄膜进行表面装袋是无效的。
表面光洁度结果
下图4-1显示了竣工FDM表面的最终表面光洁度,用无砂涂的背胶膜(Tooltec CS5)密封的工具,手动砂涂后用背胶膜密封的工具和用环氧树脂密封的手动磨损工具。复合材料刀具最常见的表面光洁度要求也显示出来进行比较(64µin(1.6µm),Ra)。可以看出,用于密封FDM复合材料工具的常用方法产生的表面光洁度比典型要求要平滑得多。
图4-1:常见FDM后处理技术产生的表面粗糙度。
第5节-工具寿命和特性数据
在设计指南开发过程中进行了广泛的测试和表征,以验证FDM复合材料工具的性能。测试包括对溶剂暴露、放气(以验证是否缺乏潜在污染物)、水分暴露、精度和热稳定性的评估,以及对工具寿命的初步评估。以下小节提供了评估总结和主要结果。所有测试都是在ULTEM 1010树脂中生产的工具或测试试样上进行的。
精度和热稳定性
为了评估准确性和稳定性,在热循环前后对多种工具进行了评估。生产了三种工具设计,构建风格(外壳与稀疏)和尺寸各不相同,共有五种变体(见图5-1)。这些工具被送往外部检查机构进行精确的3D扫描。使用具有SLP 300激光头(来自laser Design)的Platinum FaroArm(来自FARO Technologies)。使用PolyWorks View 3D计量将扫描数据与每个工具变体的CAD模型进行比较软件(来自Innovametric)。
用于该评估的复合工具在初始3D图像之前进行了后处理(研磨)。之所以选择这种配置,是因为几乎所有FDM复合材料工具都将经过这样的准备,从而使后处理工具的准确性成为最相关的数据。尽管操作员之间的后处理可能存在一些可变性,但材料的总量发现在磨损过程中去除的相当小(使用标准最佳实践),并且不代表总体尺寸变化的显著部分。
如上所述,工具在暴露于高温下之前进行扫描,然后进行热循环。对于循环,将工具真空装袋(信封装袋方案),加热至350°F(177°C),在全真空下保持温度两小时(最低),然后在两次循环之间降低至150°F(66°C)以下,总共连续10次烤箱循环。
3D扫描仪的精度为±0.0015英寸(0.0381 mm),FaroArm的精度也为±0.00115英寸(0.0381mm),总精度为±0.003英寸(0.076 mm)。此限制适用于扫描并与原始CAD数据进行比较的工具。为了将循环后的刀具几何结构与循环前的扫描数据进行比较,必须将精度汇总或“叠加”,从而导致精度限制为±0.006英寸(0.152 mm)
图5-1:用于热稳定性测试的工具设计(显示为打磨,但未密封)。
精度和热稳定性-结果
评估的代表性数据集如图5-2至5-5所示,用于打印示例工具和原始CAD模型数据之间的比较(无热循环)。如图5-2所示,扫描数据显示,外壳式工具的面积与模型相差约0.019英寸(0.482 mm),超过92%的工具在±0.015英寸(0.381 mm)范围内。对于这个特定的例子,超过该值的大部分区域都在EOP之外。作为参考,主题工具的尺寸约为14.5 x 10.5 x 4英寸(368.3 x 266.7 x 101.6毫米)。
对于与上述相同的示例工具几何结构,但以稀疏构建样式设计和打印,数据显示该工具的面积与模型的差异约为0.018英寸(0.457毫米),如图5-3所示。对于该工具,超过90%的工具在±0.015英寸(0.381 mm)范围内,同样,可以看出,变化较大的大多数区域位于EOP之外,并集中在工具的垂直面上。
图5-2:无人机风扇叶片工具(外壳式)的3D扫描数据,带有与原始CAD模型(无热循环)。尺寸单位为英寸。
图5-3:无人机风扇叶片工具(稀疏型)的3D扫描数据,带有与原始CAD模型(无热循环)的颜色图比较。尺寸单位为英寸。
图5-4和5-5显示了10次热循环后上述两种工具的扫描数据。可以看出,尺寸变化可以忽略不计,特别是考虑到±0.006英寸(0.152毫米)的精度限制。对于外壳工具,超过95%的工具表面在该限制范围内,对于稀疏工具,超过90%。计划对工具精度进行进一步调查,包括使用更精确的检测设备(如CMM),并将包括在未来的设计指南中。用于评估的工具正在进行额外的热循环。此外,特别是对于稀疏刀具,扫描数据显示刀具末端垂直表面的大部分变化。这是合法的变化,还是与扫描设备的限制有关,尚待验证。
图5-4:热循环后无人机风扇叶片工具(外壳式)的3D扫描数据,与3D的颜色图比较循环之前扫描相同工具的数据。尺寸单位为英寸。
图5-5:热循环后无人机风扇叶片工具(稀疏型)的3D扫描数据,与循环前相同工具的3D扫描结果进行颜色图比较。尺寸单位为英寸
高温机械财产
下图显示了在临界高温下进行机械测试的数据。图5-6显示了在不同温度下ZX方向上构建的样品压缩载荷的应力-应变曲线。该数据集由密苏里科技大学航空航天制造技术中心(CAMT)生成。根据ASTM D695进行压缩试验。
图5-7显示了在平面、边缘和垂直方向打印的样品在不同临界温度下的弯曲模量数据。根据ASTM D790程序A在外部实验室进行测试。图表显示,在350°F(177°C)的固化温度下,ULTEM 1010树脂的硬度降低了20-30%,这取决于印刷方向。
图5-6:ULTEM 1010树脂在不同温度下的应力-应变关系
图5-7:不同方向的临界温度下的弯曲模量。
水分敏感性
随着时间的推移,许多聚合物材料以不同的速率在一定程度上吸收水分。根据制造商(SABIC)的说法,ULTEM 1010树脂在75°F/50%RH(24°C/50%RH)下饱和时将吸收0.7%。由于水分可能对复合材料层压板的质量有害,因此进行了相对初步的测试,以确保可以通过基本的预防措施来防止这种不利影响。
为了确保饱和和“最坏情况”的暴露场景,将四个工具(外壳和稀疏结构各两个)放置在140°F/90%RH(60°C/90%)的湿度室中两周。调节后,随后将两个工具在250°F(121°C)下干燥4小时。然后在每个工具上生产八层准各向同性碳/环氧树脂层压板。固化后对层压板进行目视检查,然后切片进行显微镜检查,以检查孔隙率、分层、起泡和其他水分诱导效应的迹象。主要目的是证明即使在最恶劣的气候下,如果水分吸收成为一个令人担忧的问题,使用前烘干工具足以防止对固化零件产生不利影响。事实上,大多数处于正常使用状态的工具都可能存储在远没有测试过的环境那么恶劣的环境中。
正如预期的那样,水分暴露测试表明,使用前干燥的工具(在250°F(121°C)下4小时)可以生产出质量合格的层压板(没有明显的孔隙率或其他明显问题)。
溶剂暴露
对ULTEM 1010树脂试样(未密封)进行溶剂暴露测试,以验证其与复合材料制造设施中使用的最常见溶剂——异丙醇(IPA)、丙酮和甲乙酮(MEK)——的一般兼容性。在正常操作过程中,大多数复合材料工具只会短暂暴露于此类溶剂中,例如在零件制造前擦拭干净。为了证明总体兼容性,对溶剂洒在工具上并在相当于一个周末(约48小时)的时间内无人注意的情况进行了评估,以代表可能的最坏情况。将试样置于ULTEM 1010树脂中,然后将其浸入溶剂中48小时。暴露后,将样品从溶剂中取出,并在250°F(121°C)下烘干两小时,以确保残留溶剂蒸发。弯曲强度(三点弯曲设置)根据ASTM D 790测定,并与基线数据(无溶剂暴露)进行比较。
干燥后,暴露试样的弯曲强度恢复到相对于基准试样的完全强度,这证实了如果溶剂从工具中蒸发,最终性能不会受到影响。在实际制造使用过程中,工具通常只会短暂地暴露在少量溶剂中,在这种情况下,预计不会发生性能变化。工具也将密封在最有可能暴露于溶剂的表面,这将增加额外的保护和安全级别。
工具寿命
对非金属工具的使用寿命有一个全面的了解是至关重要的,特别是对于生产工具的考虑,或者对于原型之外的任何大量零件来说。由于所涉及的时间和资源,通过实验获得信息也是具有挑战性的。在建立初步基线的过程中,收集了实际(经验)和分析数据。
对于经验测试,遵循了前面描述的精度和热稳定性测试的基本方法,但扩展到了更多的热循环。测试了两种主要的外壳式和稀疏式结构中构建的单一工具几何结构(无人机风扇叶片)(工具如图5-1所示)。工具在350°F(177°F)、全真空、仅烤箱下循环30、60和90次,然后进行评估(检查和3D扫描)和层压板制造(八层、准各向同性碳/环氧树脂),随后进行检查。
对于分析部分,使用动态力学分析(DMA)来评估弯曲试样(三点弯曲配置)的蠕变。在100 psi(689 kPa)的加载条件下,在多次升高的温度(355°F(179°C)、385°F(196°C)和400°F(204°C))下进行等温测试,然后使用时间-温度叠加(TTS)原理来理解长期行为。TTS的使用基础来自于已证明的原理,即通过沿着时间/频率轴移动曲线,可以将给定温度叠加在不同温度的数据上。请注意,施加在复合材料工具上的大部分载荷本质上不是弯曲的,而是压缩的。因此,评估弯曲财产代表了“最坏情况”的荷载条件,并确保结果是保守的,尽管稍微不太直接适用。对压缩蠕变进行评估是理想的,但在测试时还没有这样的设备。
工具寿命-结果
对于30-90个循环的循环工具的实际评估(仅在烘箱中,仅在真空中),发现用于密封工具的TC-1614两部分环氧材料在大约30个循环时开始分解,并且在60个循环时具有严重的氧化和变色。尽管有证据表明环氧树脂密封剂降解,但层压板是在两个循环水平的工具上制造的,没有任何问题。一个工具也被持续90个循环,但环氧树脂密封剂不再能够持续粘附在工具上,并且在层压板制造过程中被从表面拉出,在该过程中损坏了工具。未密封区域的工具本身有轻微的颜色变化,但没有损坏或退化的迹象。正在对替代密封材料进行评估,以解决这一问题。
对于ULTEM 1010树脂的分析评估,通过DMA测量并使用TTS原理转移到355°F(179°C)的弯曲蠕变数据如图5-8所示,以及355°F下的应力-时间关系(179°C)主曲线。同样,需要注意的是,该数据是在弯曲载荷条件下获得的,预计这将是一个比复合材料模具实际经历的实际循环压缩载荷更苛刻的载荷条件。也就是说,结果支持ULTEM 1010树脂复合材料工具能够在原型制作卷的要求。失效时的弯曲应变为测定为3.5%,根据ASTM D790进行测试。选择应变极限,例如因为在355°F(179°C)和100 psi(689 kPa)下暴露超过200小时后,预计不会出现0.5%
图5-8:ULTEM 1010树脂试样的弯曲蠕变数据——仅使用TTS(顶部)和355°F(179°C)数据(底部)转移到355°F。
ULTEM 1010树脂能够在更苛刻的加载条件下(弯曲)进行相当于数十次高温高压高压釜循环的性能,可能超过100次循环。当然,使用较低的压力和/或较低的温度固化循环只会延长可用寿命。该数据还表明,对于在仅真空袋循环中产生的相对较低的负载下使用,工具寿命对于典型的航空航天工业零件体积来说并不是一个重要问题(至少从蠕变引起的工具变形)。经验测试强调了所用特定密封材料的局限性,但支持由ULTEM 1010树脂材料制成的工具的能力。为了更明确地确认长期能力并形成更全面的理解,有必要进行进一步的测试。附加的工具寿命特征仍然是重点。未来的开发数据将包含在后续的设计指南发布中。
工具维修
在正常的制造操作过程中,由于搬运和日常使用造成的轻微工具损坏的可能性相当高。FDM复合工具在工具损坏方面具有几个优点。首先,这些工具的重量往往只相当于同等金属工具的一小部分。由于大多数中等尺寸的工具都不需要起重机和叉车,因此这种重量减轻可以实现更简单的搬运和储存。例如,公工具的重量约为21英寸(533毫米)直径和16英寸身高小于22磅(9.5公斤)。如果确实发生损坏,FDM热塑性塑料可高度修复。这可以通过打印工具的新部分并使用与前面提到的用于连接大型分段工具(如热焊接或结构粘合剂)的相同方法将其连接起来来实现,这取决于损伤的应用和大小。最后,由于FDM工具的成本和交付周期往往明显低于传统工具,在不太可能发生严重损坏的情况下,从成本角度来看,3D打印一个全新的工具通常是可行的。附录D中提供了修理FDM工具的基本程序。
第6节-用例和示例
客户成功案例-达索猎鹰喷气式飞机内饰板
达索猎鹰喷气式飞机是商务航空领域的领导者。通过对技术创新的不懈追求,达索创造了世界上最先进、最高效、最舒适的喷气式飞机。Falcon Jet渴望创新,不断简化供应链,缩短上市时间,并对生产和开发环境做出动态响应,这促使他们寻求新的制造解决方案。FDM解决许多关键痛点的潜力促使Falcon Jet和Stratasys合作,研究FDM工具在中低体积复合材料结构中的操作和经济优势。
Falcon Jet和Stratasys的团队密切合作,为飞机内饰板的复合材料结构重新设计工具,以优化FDM工艺的设计。图6-1和6-2显示了复合材料面板的叠层工具和机加工夹具的显著变化。
图6-1:传统玻璃钢叠层模具视图(顶部)和FDM叠层模具(底部)。
图6-2:传统FRP加工夹具(顶部)和FDM加工夹具(底部)的视图。
面板的叠层模具设计为稀疏型工具,具有暴露的支撑结构(即开口/无盖端),以优化气流并最大限度地减少材料使用,如图6-1所示。尽管在工具中留下了梯形切口,以适应叉车等设备的运输,但FDM工具的重量仅为17磅(7.7公斤),可以很容易地手动运输。Falcon Jet复合材料面板需要在1个大气压(仅真空)下达到250°F(121°C)的中等固化温度,这完全在用于叠层模具的ULTEM 1010树脂的性能范围内,因为它可以轻松承受350°F(177°C)以上的固化循环。
复合材料面板的加工夹具采用与叠层模具相似的风格设计,结合了暴露的内部结构,以减少材料使用。此外,加工夹具采用印刷支架设计,可与CNC加工中心和提升点对接,轻松融入现有工作流程,并采用ASA材料生产,以节省额外成本。
相比之下,用于内部复合材料面板的传统纤维增强聚合物(FRP)铺设工具和机加工夹具各需要10-16周和20-30万美元的采购时间,表6-1。FDM技术证明了将每个工具的交付周期、成本和重量显著减少70-80%或更多的能力。通过使FDM复合材料工装符合中低批量生产的要求,Falcon Jet能够对生产环境中的需求波动和定制做出动态、经济高效的响应。
表6-1*成本包括材料、机器制造时间、硬件以及准备和检查所需的劳动力。
客户成功案例-副翼心轴
在开发创新的下一代复合材料结构时,一家领先的公务机OEM与Stratasys接洽,寻求验证FDM复合材料上置工具的使用。使用ULTEM 1010树脂芯轴,开发并制造了一种正在申请专利的“单次发射”(一体式、单次操作结构)复合副翼的概念验证产品。
副尺寸副翼为全长(~24英寸(610毫米))和厚度,但与生产版本的96英寸(2438毫米)全跨度相比,翼展减小了(~24英尺)(610毫米。叠层工具由7个部分的21个ULTEM 1010树脂心轴段组成。每个部分都有一个主要的中间部分和两个用于组装的短端盖,如图6-3所示。分段是垂直建造的,以最大限度地减少材料使用并优化表面光洁度。在一台Fortus 900毫升上,所有分段的总建造时间都不到六天,使用的材料不到3600美元。(有关更多信息,请参阅表6-2。)心轴也用于制造过程中的专有初始步骤,这对适当的层压板固结和整体尺寸控制至关重要。过程中和最终副翼图像见图6-4和6-5。
通过这种方法,客户利用了ULTEM 1010树脂更高的CTE(相对于传统的工具材料),实现无故障在零件固化和冷却后移除心轴。总体而言,FDM工具提供了增加的功能,同时减少了交付周期和成本。
表6-2*基于Fortus 900mc的建造时间和材料(成本在五年内摊销,以65%的利用率运营)。**使用0.020英寸(0.508毫米)的切片高度(在本项目时不可用),可以将构建时间缩短40-50%。由此产生的工具成本约为5600美元。材料使用包括模型和支撑。
图6-3:单发复合副翼示意图(左)和七个芯轴部分的模型(右)。
图6-4:副翼过程中的上篮和最终配置(未显示真空装袋)。
图6-5:最终的单发复合副翼子尺度演示器。
客户成功案例-Aurora Flight Sciences多部件整流罩工具
Aurora Flight Sciences(AFS)是航空和航空研究领域公认的领导者,专门设计和建造专用飞机。AFS和Stratasys合作,在开发和生产多种载人和无人飞机结构的过程中,评估和实施FDM复合工具、辅助制造工具(夹具、夹具、装饰工具等)和飞行部件。一位关键客户要求AFS在很短的时间内为一架经过改装的半人马座飞机设计和生产一个大型腹部吊舱整流罩(约9英尺(2.74米)x 24英寸(0.61米)x 30英寸(0.76米)[L x W x H])。在收到多份传统复合材料工装的外部报价后,AFS向Stratasys寻求支持。
整流罩的尺寸要求对工具设计进行分段,以适应结构Fortus 900立方厘米(36英寸(0.91米)x24英寸(0.61米)x36英寸(0.9一米)[宽x深x高])的舱室。此外,如图6-6所示,最佳尺寸的零件设计会导致陷入工具几何结构(即,在不拆卸或破坏的情况下,固化零件无法从刚性工具中移除)。FDM的灵活性使节段设计成为可能,使工具的关键圆柱形截面在铺设和固化后很容易从零件中脱落。
由于玻璃纤维/环氧树脂整流罩使用低温固化[<200°F(93°C)],不使用高压釜材料,因此该工具内置在PC中以节省成本。PC相对于ULTEM 1010树脂的较高CTE(比PC低40%)的影响由于相对较低的固化温度而减小。部分建筑有两种建筑风格——稀疏和空心外壳。稀疏的部分是在900毫升的Fortus上与Xtend结合建造的™ 500个材料罐【每个罐500英寸³(9194厘米³)的材料】,以减少建造时间和材料更换。建造完成后,用高温膨胀泡沫填充中空部分,以进一步提高工具刚性,同时将成本和制造时间降至最低。
充分利用FDM功能,AFS能够满足客户的要求,因为与传统工具相比,交付周期缩短了60-80%,同时还节省了60-75%的成本(参见表6-3)。除了显著节省成本和时间之外,FDM实现了设计的无故障分割,允许使用陷波工具配置。2015年6月的一篇文章介绍了FDM复合工具的这个例子在《复合材料世界》杂志上(Sara Black,“日益增长的趋势:3D打印航空航天工具,《复合材料世界》,2015年6月22日至31日),也在线:http://www.compositesworld.com/articles/a-growing-trend-3d-printing-of-aerospace-tooling
表6-3*基于使用Stratasys Direct Manufacturing在多台机器上并行构建工具段,展示了使用支持局来管理过剩构建能力的案例。
图6-6:FDM构建后干式装配工具(顶部)和带有固化玻璃纤维/环氧树脂整流罩的工具(底部)。
图6-7:安装在半人马座飞机上的复合材料腹部吊舱整流罩(涂装前后)。
客户成功案例-RockWest复合材料雷达罩
Rock West Composites是一家复合材料产品的全方位服务供应商,提供从初始工程和产品开发到原型设计以及低批量和高批量生产的服务。他们利用各种各样的制造技术,并利用数十年的行业经验,提供定制、经济、高性能的解决方案。
在与Stratasys合作完成各种开发项目后FDM工具的独特交付周期优势,Rock West被一位客户接洽,该客户需要在不到4周的时间内生产一个直径为20英寸(508毫米)的低介电(石英)雷达罩,用于飞行测试。Rock West认识到,该项目的时间紧迫,体积小,是利用FDM独特优势制造雷达罩的绝佳机会。
Stratasys和Rock West密切合作,为雷达罩设计了模具和钻孔导轨。叠层模具由ULTEM 1010树脂制成,用于高温[350°F,(177°C)]固化,钻导由更具成本效益的材料ASA制成。叠层模具采用两英寸(51毫米)厚的外壳和0.5英寸(12.7毫米)稀疏的双重密集填充图案,将外壳和稀疏风格的设计结合在一起,如图6-8所示。增材制造工艺所赋予的设计自由度允许这种设计的优化,这提供了一种刚性结构,也使材料使用和成本最小化。叠层模具和钻孔导向器都在三天内生产完成,使复合材料部件能够在不到四周的时间内生产并安装在飞机上。FDM工具的使用使Rock West能够在严格的时间限制下生产精密产品。图6-9显示了叠层模具和钻孔导轨的视图。
图6-8:FDM叠层模具上的复合部件(白色)视图(琥珀色)。
图6-9:FDM叠层模具视图(左)和ASA钻头导向器视图(右)。
表6-4*假设拥有Fortus 900毫升的原材料和机器运行时间的成本数据。
客户成功案例-Penske比赛团队:高温大师和牺牲心轴
Penske 团队是职业体育史上最成功的球队之一。凭借450多场大赛的胜利,他们有着进步和创新的历史。Penske团队现在正寻求FDM技术来加速开发,实现复合材料结构的动态响应和制造。
Penske 团队需要为即将到来的比赛快速制造一个由碳纤维复合材料制成的燃料探测器本体。燃料探测器主体是一个更大组件的一部分,该组件用于为赛车快速加油,如图6-10所示。传统上,燃料探针主体由铝片金属和管道制成。比赛团队希望改用复合燃料探测器,以便更好地结合反馈传感器,减轻重量,改善化妆品。然而,比赛季节的时间限制很紧,传统复合材料工具方法的交付周期很长,这使得生产复合材料燃料探针主体几乎不可能。Penske团队选择使用FDM技术制造燃料探测器主体的主图案和核心,以大幅减少他们的工具交付时间,并为即将到来的比赛提供生产能力。
图6-10:燃料探针本体视图。
图6-11:初始制造过程中复合材料模具主图案的视图。
表6-5*成本包括材料和机器制造时间,假设拥有Fortus 900mc。
客户成功案例–Swift Engineering,Inc.无人机螺旋桨桨叶压缩成型工具
斯威夫特工程公司(Swift Engineering,Inc.)是赛车运动和航空产品开发与制造领域公认的领导者,在开轮赛车方面有着广泛的血统,在航空航天领域也有着强大的新兴影响力。在为风洞测试开发进度关键硬件的同时,Swift充分利用FDM复合材料工具节省时间的优势,快速生产出一种复杂的匹配模具,用于压缩成型碳纤维增强环氧无人机螺旋桨叶片。
大约14 x 4 x 2英寸(356 x 102 x 51 mm)的半模是使用相对较小的层厚度[0.01英寸(0.25 mm),T14构建尖端]在水平构建方向上构建的,如图6-12所示。由于形状复杂,没有完全适合消除楼梯踏步的构建方向;选择这种方向是为了最大限度地减少支撑材料,同时仍然减少工具大部分区域的台阶。该工具由ULTEM 1010树脂制成,具有所需的耐温性和机械性能。由于时间限制,没有对设计进行重大的增材制造优化设计,这意味着仍有可能进一步减少制造时间和材料使用。如表6-6所示,按照设计,两个半模需要30小时的构建时间。对于后处理,半模被手动研磨并用两部分环氧树脂密封,最终表面光洁度超过16µin(0.4µm)Ra。
图6-12:螺旋桨压缩成型工具:水平构建方向(顶部),匹配的半模(底部)。
该工具已成功用于生产多组螺旋桨叶片,如图6-13所示,用于风洞测试。具体的加工细节是专有的,但碳/环氧树脂叶片在约250°F(121°C)的温度和超过500 psig(3447 kPa)的压力下固化。由此产生的叶片满足所有初始检查要求。风洞测试将用于评估叶片设计的性能,并验证FDM在模具中的使用。
使用FDM技术,Swift Engineering满足了严格的时间表要求其创新产品开发和评估过程的初步技术目标,同时在复杂的压模模具上实现50%以上的成本节约。
图6-13:在ULTEM 1010树脂制成的压模工具上生产的碳/环氧复合材料螺旋桨叶片
表6-6*基于Fortus 900mc的建造时间和材料(机器成本在5年内摊销,以65%的利用率运行)。
客户成功案例-航空航天维修工具
领先的航空航天公司与Stratasys合作,评估并确定ULTEM 1010树脂是一种合格的复合材料维修工具材料。FDM在工具成本方面提供了巨大的优势,对于维修情况来说,最重要的是及时性。一个组织提出了一个崇高的要求,即在工程文件发布后的48小时内生产出维修工具和由此产生的复合材料维修层压材料。FDM是少数能够持续实现这一目标的技术之一,同时提供同样重要的350°F(177°C)固化温度能力。FDM证明了在生产高质量层压板的过程中满足所有要求的能力。
FDM复合材料工具,尤其是ULTEM 1010树脂其特征在于脱气、水分敏感性、溶剂兼容性,以及更多,包括测试面板和常见的维修工具形状,如右侧所示的图像中的形状。
图6-14:常见维修工具几何形状-帽加强件形状
图6-15:复杂轮廓补丁修复工具(顶部,箭头指示稳定器壁)和后处理过程中(底部)。
表6-7*基于使用0.02英寸(0.508 mm)切片高度的Fortus 900mc的制造时间和材料(机器成本在5年内摊销,使用率为65%)。
无人机围板工具
背景:无人机护罩工具是由一家领先的公司开发和使用的航空航天公司生产飞行硬件,主要用于评估FDM工具并与传统金属工具进行比较/对比。对该工具的公模和母模(未显示-评估仍在进行中)变体进行了评估,使其能够灵活控制零件的内模线(IML)或OML表面。
方法:外壳式和稀疏式工具都是在ULTEM 1010中生产的树脂,允许固化温度>350°F(177°C),尽管该应用仅需要250°F(121°C)。生产凸形外壳和稀疏工具是为了进行比较,因为最初认为外壳工具可以节省时间和成本。然而,从下表中可以看出,这种尺寸的工具在成本上几乎没有差异,并且由于较厚的外壳工具表面所需的表面轮廓数量增加,构建时间更长(直线光栅比非线性轮廓挤出得更快)。母工具的生产是为了提供控制零件外部空气动力学表面的能力,并且尺寸稍大,以允许材料叠层。因此,该工具的构建时间和成本略高。所有工具都以垂直方向构建,以最大限度地减少楼梯台阶和支撑材料的消耗。对于后处理,工具被手动研磨并用两部分环氧树脂密封,最终表面光洁度超过16µin(0.4µm)Ra。所得零件(在公型稀疏工具上生产)也如图6-16所示(袋子侧面显示了专有涂层)。
图6-16:ULTEM 1010树脂中的FDM工具(顶部)和产生的零件(中间、底部)。
此外,还创建了一个单独的钻孔和修整工具(图6-17)补充上篮工具。通常,此类工具的打印成本较低材料。在这种情况下,由于工具尺寸小,它们是在ULTEM 1010树脂中以与叠层模具相同的构造生产的。该辅助工具设计用于嵌套在生成的零件上,并使用索引孔来确保精确对齐和最终修剪轮廓。结果-所有工具都在不到3天的时间内完成了制造和后处理,成本低于600美元(每个)。*
*成本基于Fortus 900毫升的建造时间和材料(机器成本在5年内摊销,使用率为65%)。
图6-17:顶部-外壳式围带工具垂直构建方向(顶部);稀疏样式的上篮工具和相应的钻孔和修剪工具(底部)。
无人机舱壁工具
背景:隔板工具是一个基于生产部件的示例工具设计,经过修改以演示本指南中深吃水内螺纹工具的设计。叠层表面代表最终零件的OML,因此尺寸控制对于确保飞机结构内的正确装配和组装至关重要。
方法:由于舱壁工具的形状本身就是刚性的,而且几乎没有考虑到稀疏工具的好处,使用了shell设计。由于工具的凹形和深度,热膨胀是防止固化部件被工具锁定或损坏的重要考虑因素。该工具的固化温度为250°F(121°C)。尽管温度要求较低,但ULTEM 1010树脂是首选材料,因为它提供了FDM材料中最低的CTE。该工具以平面(“水平”)方向构建,具有精细分辨率构建尖端[0.010英寸(0.254 mm)切片高度]。这是该几何图形的最佳构建方向,以最大限度地减少零件内部半径中的阶梯。包括工具的顶部法兰,以辅助零件固化后提取。它们提供了在EOP外部堆放材料的区域,这些材料可在零件拆卸过程中用于杠杆作用,随后进行修剪。然而,有一个折衷方案,即可选法兰确实需要大量的支撑材料,因此值得考虑替代设计,以进一步优化工具。对于后处理,工具被手动研磨并用两部分环氧树脂密封,最终表面光洁度超过16µin(0.4µm)Ra。
结果:适用于250°F(121°C)固化温度的内螺纹工具设计在不到三天的时间内以更低的成本实现、建造和后期处理超过980美元。
*成本基于Fortus 900毫升的建造时间和材料(机器成本在5年内摊销,使用率为65%)。
图6-18:无人机舱壁工具。
图6-19:无人机舱壁工具正在准备使用。
图6-20:水平构建方向(顶部);工具设计横截面(中间);显示锚柱的横截面,用于防止FDM过程中的热变形(底部)。
延伸阅读:
扫二维码用手机看
最新消息
ZEISS 三维扫描仪 | 3D打印 普立得科技
普立得科技成立于2004年,专注于工业级3D打印机与三维扫描,同时我们也是ZEISS GOM代理商,并提供3D打印及扫描的代工整合服务,特此加值整合相关软体,包含拓扑优化设计 、医疗影像分析、逆向工程 、3D检测等,期望推进积层制造的使用习惯为生产带来更多价值。





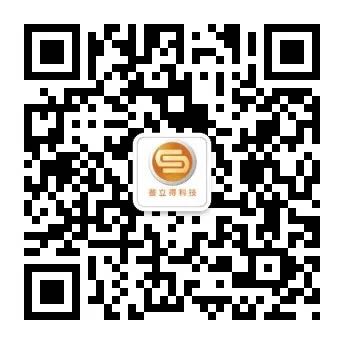
微信公众号
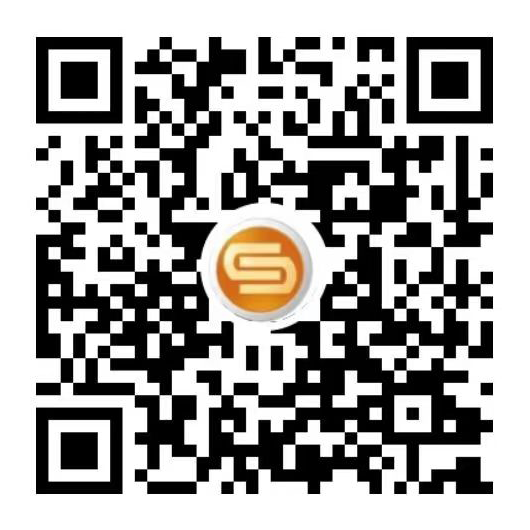
视频号
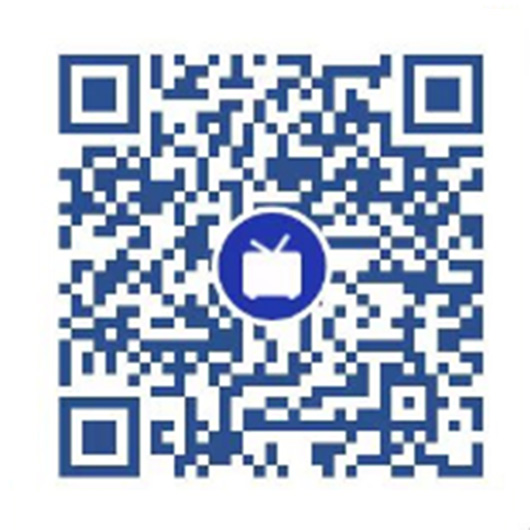
哔哩哔哩
您有什么疑问,或想咨询我们的产品与服务,请留下信息,我们会及时与您联系!
© 2021 普立得科技有限公司 All Rights Reserved 粤ICP备19059200号