产业应用
普立得科技成立于2004年,专注于工业级3D列印与3D扫描逆向工程,并提供3D打印、三维扫描的代工整合服务,同时也代理德国知名品牌Zeiss 三维扫描仪。
普立得科技在台湾地区设有3个区域办事处,大陆地区设有8个区域办事处,截至目前销售超过900套设备。普立得科技的3D打印/3D扫描技术正在改变和加快亚洲地区设计和制造的发展。 3D打印技术的出现是对生产方式的一种革新,客制化的特性能够为复杂设计降低成本,同时也能提供更低成本的零部件,使企业降低成本、获取更高利润。
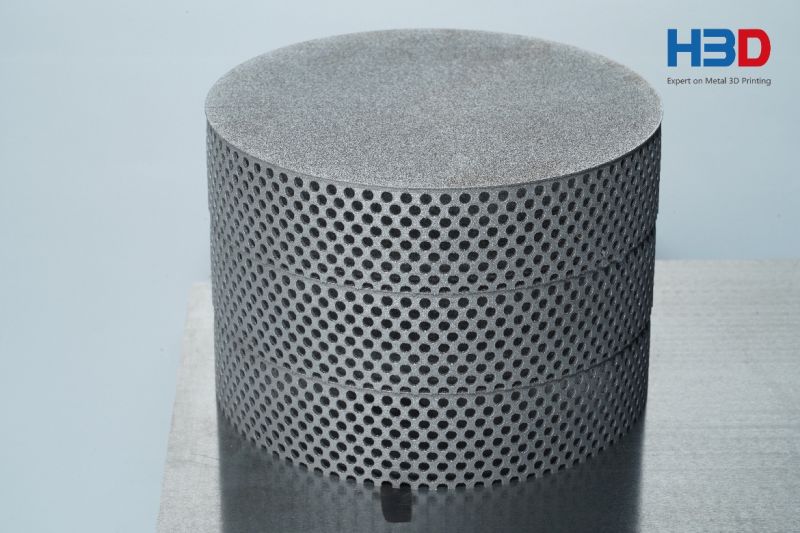
钛无支撑金属3D打印
关于支撑,这里是HBD宣布的另一项突破: 钛无支撑金属3D打印 配置了一个没有任何支柱的零支撑水平面(直径120mm)。
了解更多
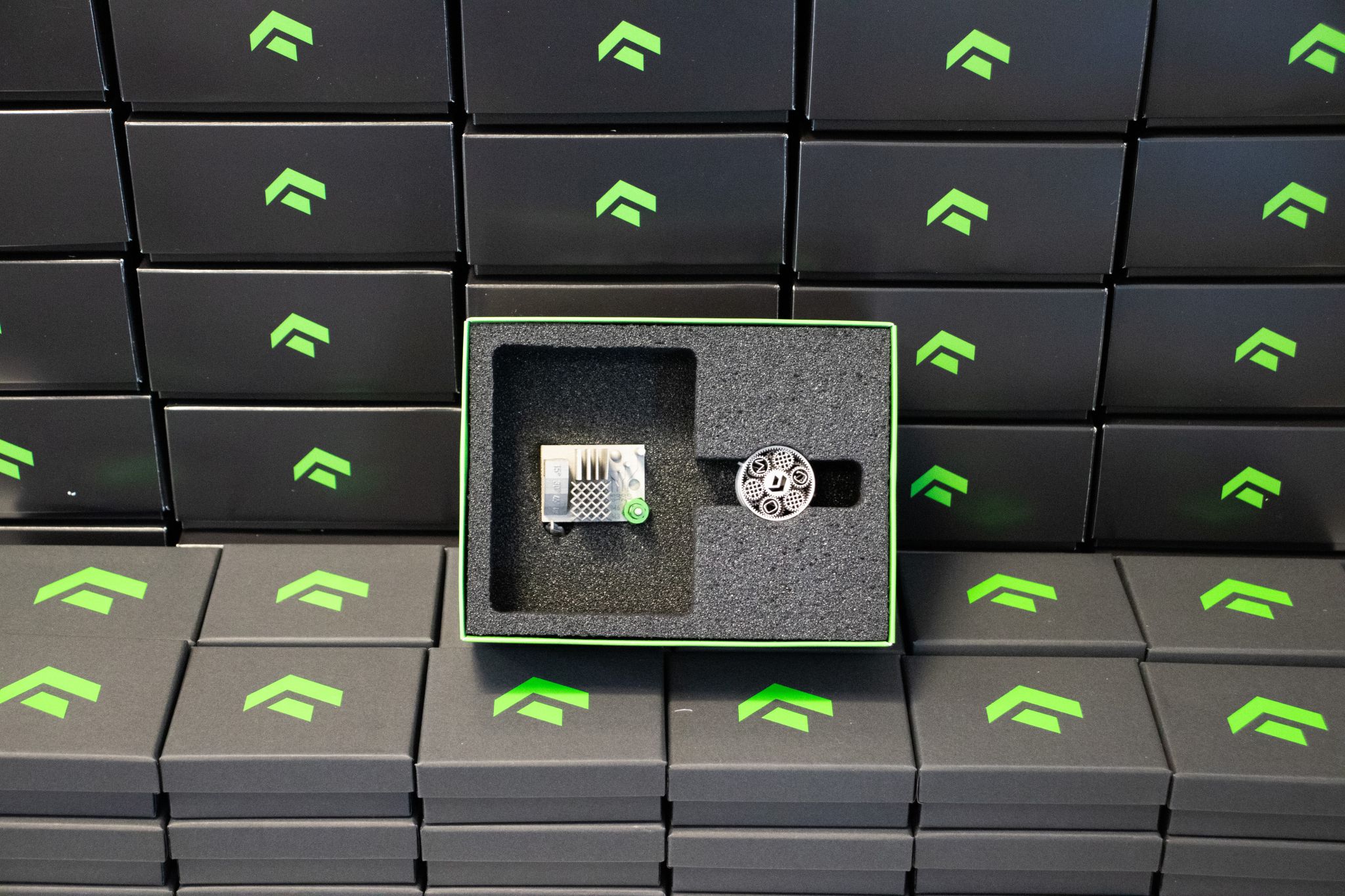
一键式金属盒 - 批量生产
一键式金属盒 - 批量生产 但里面有什么? 更大的盒子是我们的转销商盒子。它由我们的基准部件、5 个行星齿轮和两个相关的信息卡组成,解释了制造过程并展示了 多功能可能性。 较小的盒子里装着一些五颜六色的东西。有什么猜测吗?
了解更多
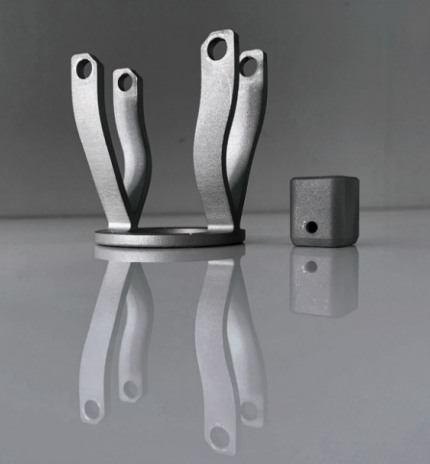
为自己的企业快速制造:添加金属制造的成本和时间效率
挑战 快速且经济高效地生产必须满足复杂功能和机械要求的组件并且同时可靠地用于长期工业用途。 如果您正在进行产品开发,并且需要一个具有特定机械功能的组件,那么有两件事对进一步开发至关重要:时间和成本。这个部件需要很快,而且生产成本不应该太高。这适用于所有开发部门,无论其公司规模如何。 在一键式金属的情况下,部件的几何和机械要求很复杂:该部件用于耐久性试验台,用作将电机连接到阀门的支架,阀门通过电机和阀门上的孔拧紧。材料专业-perties还必须具有高弹性,以便承受高达40Nm的电机力矩。 因此,由于该组件必须适合长期工业使用,因此生产样品组件的传统快速原型设计是不够的。为了确保可靠和稳健的使用,我们必须进一步考虑快速制造。 为了平等地满足部件的所有要求,以确保永久的工业用途,必须提前做出一个重要的决定:哪种制造工艺可以确保最佳结果? 制造过程必须能够实现部件的要求,并使其快速可用。 –Stefan Weber,一键式金属首席技术官 解决方案 增材金属制造确保了成本和时间效益,同时为长期使用提供行业标准的部件质量。 传统的减磨还是增材制造?如果从成本、时间和设计灵活性的角度对两种可用的制造工艺进行比较和检查,则在通过外部服务提供商进行铣削时会出现三个主要冲突: 时间:由于没有内部铣床 必须呼叫服务提供商。最快的交付时间是一个月。如果交货时间缩短,成本就会增加两倍。 成本:根据选择的交货时间,铣削部件的成本在330欧元到620欧元之间。此外,由于几何形状的自由度有限,部件必须分为多个部分制造,这意味着材料和成本费用更高。 结构:由于铣削程序实现精确的几何形状是有限的。这使得组件更大,更不容易接近,这使得组装更加困难。 通过内部金属3D打印机MPRINT+进行增材制造,因此与铣削相比,一键式金属具有显著优势: 时间:由于内部的金属3D打印机,一键金属独立于外部服务提供商的交付时间,因此节省了宝贵的时间。 成本:除了消除外部服务的成本外 供应商,一键金属可以立即回收金属3D打印中使用的高达96%的材料。这意味着一键金属不仅节省了材料成本,而且选择了更经济的增材制造选项。 设计:增材制造提供了最佳的功能集成,因为设计的巨大自由度意味着所有必要的技术功能都只包含一个组成部分。 部件上的力当电机承受40Nm的负载时,部件在支架内发生不同程度的移动。红色区域偏移最大,为0.18µm。 MPRINT+在相对较短的时间内用200W光纤激光器生产出所需的组件,同时为一键式金属提供了理想的性价比。 与塑料材料相比,金属粉末的使用也确保了该部件的材料特性能够在高达40Nm的发动机扭矩下承受其作为发动机和阀门之间支架的功能,并且不会断裂。这样,该部件就可以长期使用,毫不犹豫。 (1) CAD模型 3D打印灵活的设计选项实现了最佳的功能集成。 (2) 打印过程 预定义的工艺参数简化了打印准备确保所需的结果。 (3) 装配 完成后,可以立即安装该组件并准备使用。 节省时间96% 技术信息 组件功能 阀门和电机安装支架 材料 不锈钢1.4404/316L 节省成本23% 技术 带200W光纤激光器的LPBF 层数 3541 施工时间 22.3小时 粉末消耗量 0.18公斤 生产成本2 253,01欧元 节省材料97% 1.组件的实际消耗,不包括打印过程的总工作量。 2.成本计算假设内部机器具有系统市场价格,包括人员和装修成本。 该部件必须能够承受发动机扭矩,因此具有较高的抗拉强度。材料特性必须确保这一点。 –Michael Volk,One Click Metal首席产品开发工程师 优势 节省时间和成本 一键式金属在为组件选择添加剂制造时的最大优势是显著减少了时间和成本。这不仅包括制造时间和成本,还包括交货条件和材料。这导致了性价比的最佳平衡,同时具有最小的努力和最大的结果。 加速开发时间 最重要的是,在公司自己的金属3D打印机MPRINT+中,增材制造的时间独立性为一键式金属提供了主要优势。由此产生的组件打印灵活性大大加快了开发时间,因为它不受外部服务提供商交付时间的限制和延迟。 可持续供应链 在全球化时代,许多供应链都不明确且复杂,内部增材制造的可能性意味着从粉末供应商到成品部件的整个价值链都有一个透明的视角。通过这种方式,一键金属能够避免漫长的交付路线,并减少潜在的环境影响。 个体繁殖能力 公司内部工业金属3D打印的实施模拟了组件的多次单独复制。一旦确定了工艺参数,就可以随时重复制造工件。此外,可以很容易地调整可能的变化根据发展现状,并根据各自的要求进行调整。这消除了大量生产过剩或大量库存的需要。 我们能够毫不拖延地继续开发我们的产品,因为组件很快就可以买到,而且我们不依赖交付时间。 –Roman Denisov,开发工程师,One Click Metal 关键事实摘要 挑战 快速、经济高效地生产一种组件,该组件必须满足复杂的功能和机械要求,同时可靠地发挥作用,以供长期工业使用。 节省时间96% 解决方案 增材金属制造确保了成本和时间有效性,同时提供长期使用的行业标准组件质量。 成本节约23% 优势 1、节省时间和成本 2、加速开发时间 3、可持续供应链 4、个体繁殖能力 节省材料97% 技术信息 组件功能 阀门安装支架和发动机 材料 不锈钢1.4404/316L 技术 带200W光纤激光器的LPBF 层数:3541 施工时间22.3小时 粉末消耗量1 0,18kg 生产成本2 253,01欧元 1、组件的实际消耗,不包括打印过程的总工作量。 2、成本计算假设内部机器具有系统市场价格,包括人员和装修成本。
了解更多
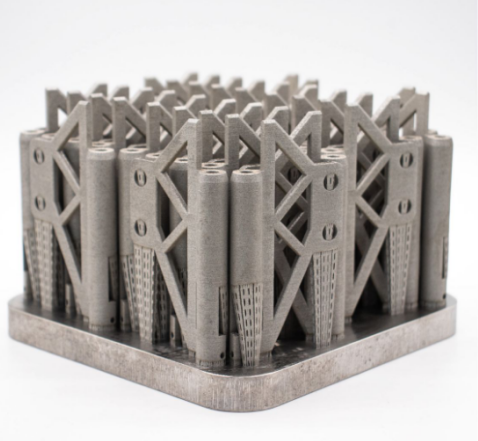
WERKE一家国际机器制造商如何通过使用金属3D打印,一步一步地提高生产成本。
简介 如今,INDEX Werke及其品牌INDEX和TRAUB是其中之一世界领先的数控车床制造商之一。带5个生产基地和七个国际销售和服务 Esslingen-总部位于纽约的公司集团目前在全球80个地点开展业务。这家总部位于Esslingen的公司成立于1914年,如今拥有2000多名员工。高度创新的产品系列以及为最佳客户解决方案提供的全面服务体现了质量、可靠性和技术领先地位。 INDEX Werke旗下品牌INDEX和TRAUB是世界领先的数控车床制造商之一。这家总部位于Esslingen的公司集团拥有五个生产基地、七家国际销售和服务公司以及广泛的经销商网络,在全球80个地点设有办事处。 INDEX集团的特殊优势在于在每种情况下都能为客户开发出最佳的制造解决方案。凭借INDEX和TRAUB品牌,该集团拥有最广泛的车削零件完整加工计划,包括系列和单件产品-生产。应用工程师在为客户制定最佳制造策略时可以从中汲取经验。特别是在几何要求高、精度高的工件中,工程服务对客户来说是不可估量的好处。这既适用于标准设计中的单个机器,也适用于完整的制造系统,可以由几个相互连接的机器组成。工程和研发在INDEX占据着关键地位,超过10%的员工在INDEX工作。 挑战 为多轴自动车床的棒料库生产滑块的经济性,该滑块由滑块小车和夹紧件组成。 INDEX为其多轴车削提供棒材进料器机器,负责将原材料送入加工区。为了能够不断地将棒材送入加工过程,每个金属棒材都有一个滑块。通常,滑块由滑块小车和夹紧件组成。有可能节省成本以及组装和存储成本。为了更容易理解,我们将分别考虑滑块和夹紧件,因为两者都可以通过3D打印进行优化 因此,INDEX希望主要通过以下因素使用金属3D打印来节省时间和成本: 1.减少组装工作量 2.减少废品 3.减少制造工作量 4.减少所需的备件存储空间 如何在添加剂的帮助下实现这一点制造将在下面的页面上进行解释。首先,让我们看一下这两种应用程序及其要求。 应用程序 棒式给料机需要两个应用程序协同工作,才能将材料送入多轴机器的处理室。第一个应用是滑动小车,它充当夹具的“臂”。 作用 通过弹簧加载的冲头将夹紧件的轴向移动力传递到半成品杆上。 组件要求 滑动小车必须具有高稳定性和精度,才能安装弹簧柱塞。还必须能够将滑动小车安装在夹紧件上。 以前的生产方法 目前,滑动小车由一个底板和一个转动部件组成。旋转部件焊接在基板上。 迄今为止的单位数量和成本 滑动小车每年需要520台。到目前为止,传统生产的成本为每个滑块127欧元.手推车这导致每年总计66040欧元。 挑战 由于焊接工艺的必要性,滑动小车的生产非常复杂,并且涉及增加的时间和成本。此外,该部件还存在质量问题,主要是由于焊缝造成的。这可能会导致故障,而故障又会耗费时间。 应用程序 第二种应用是所谓的夹紧件。它与滑动小车一起将棒材输送到加工区。 作用 坐在V型皮带上,在滑动小车的帮助下将棒材输送到加工区。 组件要求 该部件应精确地位于C形导轨中,并且必须能够在几乎没有磨损的情况下来回移动。此外,必须为皮带安装和夹紧件的安装切割螺纹。 以前的生产方法 夹持件目前由两块不锈钢板和一个铝制基体组成。由于导轨的位置必须精确地与基体相匹配,因此两块不锈钢板被钉在铝基体两侧并用螺钉固定。这导致了较高的组装工作量。然后将螺纹切割成软铝。 迄今为止的单位数量和成本 每年需要520个夹紧件。到目前为止,传统生产的成本为每件夹紧件205欧元。这导致每年总计106600欧元。 挑战 必须为夹片的各个零件创建几个供应商。这导致了多阶段的供应链以及高成本和组装工作。对于单独的夹紧件的组装,在材料供应之后需要4个步骤。如果产品棒进料器发生变化,则会增加更换工作量。重新包装的交货时间是42天。 解决方案 增材金属制造确保了成本和时间的有效性,同时提供了长期使用的工业级部件质量。 成本降低62% 该公司的专家决定使用金属3D打印机进行这两个部件的增材制造。 所需存储量减少66% 一旦创建了CAD模型,完成了数据和打印准备,设计部门就可以在公司自己的MPRINT金属3D打印机上直接开始制造过程,而不必经过通常上游常规工作准备的过程链。 组件效率降低80% 带有42个滑动小车的构建板的打印时间为50.5小时。对于夹持件,其中4个位于一个构建板上,打印时间为22.5小时。由于通过智能设计以及在安装空间中的最佳定位,使必要的支撑结构以及后处理的数量最小化 多主轴系统中的部件可以在很短的时间内完成。由于必要的螺纹可以预先打印在夹紧件中,并且夹紧件是一体打印的,因此组装从总共五个步骤减少到一个步骤。 废料减少10% 由于所使用的材料,这些部件在联合使用中显示出高的机械和热负载能力。因此,滑动小车可以最佳且可靠地将材料进给到主轴系统中的工艺中。 Material 1.2709 1.2709 Technology LPBF with 200W fiber laser LPBF with 200W fiber laser Number of layers 2328 (40µm layer thickness) 860 (40µm layer thickness) Build time 50,5h (42 pieces) 22,5h (4 pieces) Material usage 9,07cm³ /part 34,25cm³/part Manufacturing costs 29€/part by 42/job 97€/part by 4/job 常规制造 增材制造 增材制造 用途 滑动小车和夹紧件总是一起用于将棒材输送到多轴机床的加工区域。 夹紧件借助于两块金属板安装在V形带的起点和终点之间。因此,V形带通过夹持件中的凹口被积极地和摩擦地张紧和紧固。在夹紧件的中间,滑动小车用两个螺钉固定。现在,弹簧加载的柱塞可以插入滑动小车的孔中。 该组件与V型皮带一起线性移动,并根据需要将半成品输送到加工区。 在多轴机床的料库中提供了一个检查或组装位置,用于组装夹紧件和滑动小车。为了便于接近,必须打开两个半壳来引导半成品。现在,V形带的起点和终点都很容易接近,因此将两者固定在一起的夹紧件可以插入。 组装冲泡组件后,两个半壳再次闭合,组件即可使用。 优势 经过优化的组件设计 逐层增材制造工艺实现了前所未有的几何自由度。这意味着,不能使用传统制造方法一体制造的部件也可以使用金属3D打印来实现。夹持件和滑动小车都可以由单个零件额外制造,不再由单独的零件组成。此外,额外的制造可以在夹紧件上预先打印螺纹,然后可以毫不费力地重新切割。 更灵活、更快的生产 除了大大缩短了工艺链外,金属3D打印机中这两个应用程序的快速高效生产还减少了从CAD创建到现成组件所需的工作量。印刷和返工(添加剂)需要10天,而40个夹具和滑动小车需要42天(传统)。因此,如果是附加版本或自定义版本 在需要的应用程序中,只需最少的预处理即可在几天内打印出来。因此,公司能够进行灵活的调整。 通过设计调整进一步减少材料 优化原来的滑动小车设计节省了材料,从而也节省了打印时间。最初源自传统生产的设计意味着42辆滑动小车在457cm³时的建造时间为74.5小时。通过巧妙地调整设计,打印时间减少到50.5小时,材料消耗减少到381cm³。 关键事实摘要 降低62%成本 挑战 所需存储量减少66% INDEX制造的多轴系统包含一个棒料进料器,用于将材料送入加工过程。这需要由滑动小车和夹紧件组成的滑动器,这在传统生产中导致高的组装和成本支出。 解决方案将组件效率降低80% 采用金属增材制造,可以经济地开发和生产滑块小车和夹紧件,它们是理想的滑块。与传统制造相比,除了成本和材料外,组件生产的交付周期还可以显著缩短。 优点 废料减少10% 经过优化的组件设计 减少材料和成本 缩短了公司的交付周期 技术信息 棒式给料机的组件功能滑块 材料1.2709 技术 带200W光纤激光器的LPBF 层数 滑动小车:2328 夹紧件:860 生成时间 滑块小车:50.5h 夹紧件:22.5h 每个零件的粉末用量滑块小车:9.07cm³ 夹紧件:34.25cm³ 制造成本滑块小车:29欧元/件 夹紧件:97欧元/件
了解更多
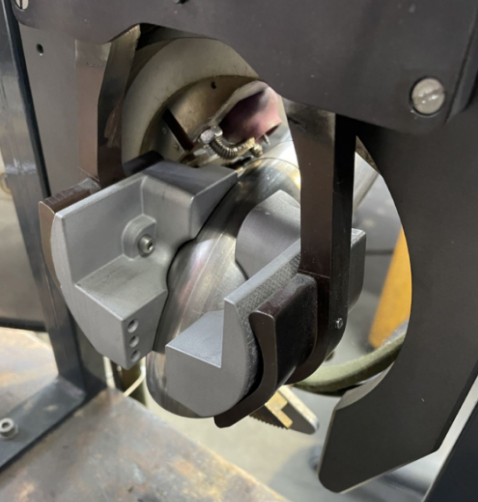
HOEDTKE金属UND激光技术如何创新金属加工公司正在利用潜力金属3D打印的发展 定制解决方案,同时减少制造交付周期。
挑战 对于客户,必须制造与安全相关的弯管其生产仅轨道焊接被批准为制造商-环工艺。但是,由于几何形状的原因,零部件不能夹在焊接机的标准框架中。 解决方案 金属增材制造的使用使得-管道夹爪的研制与生产肘部。与传统生产相比,manu-制造这些部件也可以减少一半以上。 优点 优化组件设计 减少工作量 显著缩短了公司的交付周期 技术信息 组件功能:2个弯管夹爪 材料:不锈钢1.4404/316L 技术:带200W光纤激光器的LPBF 层/组件:1878 层厚:20µm 构建时间:22.5小时 粉末用量/成分:0.3公斤 Hoedtke Metall-und Lasertechnik是一家以创新为导向的生产公司,具有工程能力,旨在在塑造我们时代的技术问题方面发挥决定性作用。该公司为客户提供开发和实现创意和产品。 数十年的经验 Hoedtke Metall-und Lasertechnik在金属和钣金加工领域拥有超过85年的经验。作为最早的公司之一,Hoedtke自1979年以来一直致力于三维部件的激光切割、焊接和硬化。 此外,十多年来,霍克一直在使用各种塑料和金属增材制造工艺。该公司专注于技术和应用程序开发。这包括各种材料加工的系统工艺参数研究以及新型硬件和软件的测试组件以及增材制造工业试验的各种应用的发展。 作为一家合同制造商,Hoedtke提供原型、单个零件、组件和系统,并提供制造工艺的开发和鉴定。其客户包括汽车行业、飞机制造和医疗技术等各行各业的公司。 挑战 对于客户来说,必须焊接与安全相关的弯管。但是,由于部件的几何形状,焊接过程经客户批准的不易适用于生产这些管道。 该顺序具有挑战性的方面是,线性部分仅为20mm的弯管不适合轨道焊接系统。然而,同时,这些部件是安全相关部件,仅经批准用于用这样的系统Kai Flechsenhar,Hoedtke Metall-und Lasertechnik的设计工程师 因此,该公司面临着解决两个对立边界条件冲突的挑战: 1.客户订购的部件必须在轨道焊接系统上制造,因为它们只被批准用于该制造过程。 2.由于管的几何形状,部件不能在标准轨道焊接系统中夹紧,因此不适合使用这种系统进行生产。 弯曲管段的线性部分对于轨道焊接系统的现有夹紧装置来说太小。管段可以不被提起并气密焊接。由于焊接工艺由客户要求决定,因此焊接设备必须以便能够成功地处理客户的订单。 解决方案 金属增材制造的使用使经济地开发和生产适用于管件的夹爪。此外,交付周期用于部件的生产可以减少64%。 该公司的专家选择增材制造独立的夹爪,以影响客户组件的曲率。所开发的部件起到了适配器的作用,从而能够将管段夹紧在现有的焊接结构中。因此,在制造过程中可以满足客户的要求。 制造过程可以在创建CAD模型、数据和打印准备后,通过公司自己的MPRINT金属3D打印机上的设计部门直接开始,而不必经过通常上游的经典工作准备的过程链。 两个夹爪的印刷时间约为46小时,总粉末消耗量约为0.6kg后,组件完成。由于必要的支撑结构以及后处理的数量通过智能设计和优化最小化轨道焊接系统中的部件的组装可以在尽可能短的时间内进行。 总体而言,通过使用金属3D打印,可以将从数据创建到最终夹爪的交付周期缩短约64%。这种减少尤其是在数据准备和生产方面实现的。除了加快金属3D打印的工作准备外,主要通过减少等待时间来缩短流程链。出现这些情况例如,由于公司的材料库存和机器容量有限,在机械加工生产中。 由于所使用的材料,夹爪在使用中显示出高的机械和热负载能力。因此,弯管可以通过开发的设备可靠地固定和气密焊接,从而成功完成客户订单。两个夹爪现在也可用于客户的下一个订单系列。 在几天内,从组件的设计到最终使用的整个过程链都可以运行——这是与传统制造相比,速度明显更快。”Hoedtke Metall-und Lasertechnik增材制造技术专家Vanessa Seyda博士 优势 经过优化的组件设计 逐层增材制造工艺实现了尚未实现的几何自由度。这意味着不能使用传统生产方法制造的部件也可以使用金属3D打印来实现。由于设计自由,制造的部件的功能表面可以最佳地适应和生产管部件。这确保了部件的可靠和长期使用。 工作量减少 金属3D打印机中两个夹爪的快速高效生产既减少了明显缩短的工艺链,也减少了从CAD创建到现成组件所需的工作量。如果需要额外的或定制的夹爪,只需几天的准备工作就可以打印出来。因此,该公司能够生产客户订单的管道部门-每次新的系列订单都不会出现并发症。 显著缩短了 几天之内,Hoedtke Metall-und Laser technik的技术专家就能够开发出一种部件专用焊接材料,并使用金属增材制造进行制造和测试。与相比,由于等待时间缩短和流程链缩短,该应用程序在公司的交付周期缩短了一半以上传统制造。
了解更多

Cold Metal Fusion 3D打印为Binder Jetting技术提供了更高质量、更经济的替代方案
大多数时候,当一家公司表示正在开发3D打印技术时,人们通常会直接想到“3D打印机的开发”。当我们听说Headmade Materials以及他们制作这种金属3D打印踏板的有趣方式时,我们犯了这个错误。Headmade Materials不是一家3D打印机制造商,然而,该公司开发的3D打印技术是我们在这个市场上见过的最有趣的技术之一——用于材料生产。 这项技术被称为冷金属聚变(CMF),这一概念诞生于联合创始人仍在当地聚合物研究机构Das Kunststoff Zentrum(SKZ)工作时。整个故事大约始于五年前,创始人之一克里斯蒂安·斯陶迪格尔和克里斯蒂安·费舍尔。 有些人可能会说这是运气,但我想说,他们的项目当时专注于高填充聚合物的加工和激光烧结工艺,他们的工作,最重要的是,他们的技术性能,有助于在不到五年的时间内快速将这一概念从研发阶段转变为商业阶段。 “在第一次拍摄后,我们已经有了非常好的第一感觉,我们实现了96%的高密度。但我们花了几个月的时间深入市场,找出潜在客户的痛苦和收益。在我们相对容易地找到更大的试点客户后,我们意识到我们的流程确实满足了市场需求”,Staudigel在一次对话中告诉我们。 那么,这个概念是什么,可以用零件实现96%的高密度? Cold Metal Fusion技术是一种基于烧结的3D打印技术,可以打印金属零件。该解决方案专为批量生产而设计,将SLS的世界与用于脱脂和烧结的标准粉末冶金工艺相结合,可以帮助制造商实现超过100000个零件/年的产量。 “在我们的冷金属融合技术中,我们独特的原料材料,由金属粉末和粘合剂组成,在激光烧结机上加工聚合物,以获得绿色零件。然后,在标准的粉末冶金工艺中,绿色零件被脱胶并烧结成复杂的金属零件,”我们在本周意见中的嘉宾解释道。 这里特别有趣的是,SLS和粉末冶金在制造操作中都有着良好的质量记录。然而,Headmade Materials的团队已经找到了一种方法,通过将原料材料集成到游戏中来增强和结合这两种方法,而不需要任何其他工艺或机器调整。在这种情况下,人们可以期待的第一个好处是可以获得广泛的材料选择。事实上,Headmade的产品组合中已经有316L不锈钢、钴铬、Ti6Al4V钛、CP-Ti 1级钛和钨合金。不锈钢17-4PH、无需热后处理的高硬度工具钢、具有高导热性和导电性的铜合金以及超级合金应在未来几周或几个月内跟进。 尽管他们的大部分经验都是在EOS Formiga P110和Sintratec S2机器上完成的,但总经理解释说,金属3D打印零件的生产可以在各种激光烧结系统上完成。此外,3D打印过程不需要构建板和支撑结构,就像我们过去在粉末床融合过程中看到的那样。 可能引起制造商对该技术兴趣的其他特征是工艺与MIM脱脂和烧结工艺的兼容性,其能够实现低加工温度,从而节省加热时间和能源,并消除了进一步印刷后热处理的需要;以及它能满足的零件特性(密度、屈服强度、拉伸强度、伸长率)。 该公司解释道:“冷金属熔化工艺实现的密度取决于材料、印刷和烧结工艺,但316L不锈钢的密度通常>98%,钨-重金属合金等液相合金的密度高达100%。通过优化每个金属零件的工艺步骤,可重复密度高达99%。”。 图片:Headmade Materials 尽管每批可以制造的零件数量取决于零件尺寸和机器尺寸,但Staudigel确保“[他们]技术的一个很酷的特点是易于扩展。” 从应用的角度来看,CMF技术可以针对粉末冶金行业和3D打印行业的操作员。这意味着,所有垂直行业,如医疗、汽车、航空航天和工业部门,通常采用AM技术,都可以在Headmade Materials的解决方案中找到一个有价值的附加方案。 Headmade Materials的发言人指出,从财务角度来看,他们的技术仍然“比SLM便宜。与运营商最终实现塑料零件的SLS相比,Cold Metal Fusion是金属零件的一个有趣的替代品,尤其是对于那些希望从原型和非常小的系列转向更大数量的人来说。” 他提醒道:“我们的CMF工艺与SLM相比,更具互补性。我们为行业提供了一种基于烧结的方法,该方法提供了SLS打印的优势。零件光谱和使用领域通常与SLM大不相同。最终,我们的技术为Binder Jetting技术提供了更高质量、更经济的替代方案。”。 下一步计划是什么? 该公司去年通过风险投资公司btov Partners获得了190万欧元的资金,目前正寻求扩大业务规模。 Staudigel总结道:“两年前,我们从两个人开始,现在我们有一个10人的团队。我们正在快速发展,我们必须进一步发展。从技术角度来看,我们将在未来几周发布3D打印行业独有的新合金和新产品功能。”。
了解更多

Cold Metal Fusion如何帮助使用聚合物SLS 3D打印机创建金属3D打印零件
Sintratec SLS 3D打印机上生产的金属3D打印零件-图片由Sintratec提供 增材制造中最先进的方法之一是Cold Metal Fusion,这是Headmade Materials开发的一种解决方案,用于从SLS 3D打印机中创建金属3D打印零件。需要提醒的是,Cold Metal Fusion不是一种3D打印工艺,而是一种可以与SLS 3D打印机结合的解决方案,以帮助生产金属3D打印零件。 最近,SLS 3D打印机制造商Sintratec提供了一份关于如何在其SintratecS2 3D打印机上使用冷金属融合工艺进行最终金属零件制备的详细指南。 以下是如何使用Sintratec的CMF工艺和SLS 3D打印机制造轻型汽车齿轮 3D打印过程首先识别轻质零件的复杂几何形状,然后使用Sintratec的全材料平台进行打印。Sintratec S2和MCU-160构建模块用于3D打印轻型汽车齿轮。 Headmade Materials为SLS技术制造的M2工具钢和17/4PH不锈钢是CMF机器中仅有的两种制造金属零件的材料。然而,Sintratec在其指导方针中提倡使用17/4PH进行汽车齿轮3D打印。 第一步是“打印作业准备”,类似于标准选择性激光烧结(SLS)工艺,首先在Sintratec Central软件中进行准备。一旦完成,3D模型将被导入、复制并排列以构建体积。此时要注意烧结阶段CAD设计的收缩。这因材料而异,17/4PH为14%。 设置完成后,应将打印作业切片并导出. Sintratec确保通过增材制造制造的金属零件显示出与传统制造相同的机械性能水平。相反,通过CMF工艺制造的金属零件超过了MIM标准,因为它在硬化后具有13.2%的优异伸长率。与CMF联盟硬件一起,这项技术将帮助轻型汽车齿轮用户管理孔隙率,因为该设计具有自由流动的通道,使其具有卓越的机械性能。
了解更多
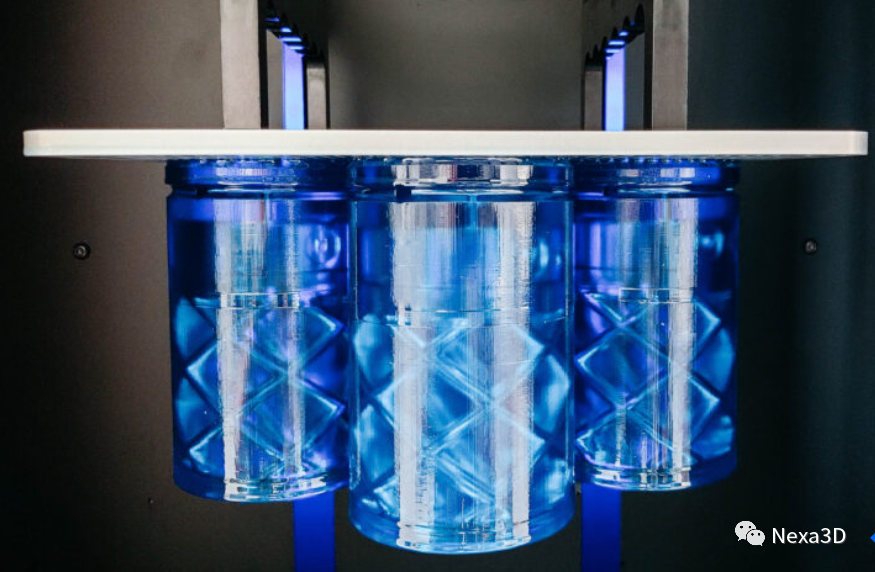
Fraunhofer IFAM使用自由注射成型(FIM)工艺加快金属注射成型
Fraunhofer IFAM使用自由注射成型(FIM)工藝加快金屬注射成型 研究所採用自由注射成型工藝,實現複雜金屬零件的快速成型 Fraunhofer IFAM是著名的Fraunhofer協會的一個研究所,是金屬注射成型(MIM)領域公認的領導者,為航空航太,能源,海事和其他要求苛刻的行業的公司提供服務。為了支持對新應用的研究,同時降低交貨時間和成本,Fraunhofer最近決定實施由Nexa3D的XiP Desktop 3D印表機和LSPc®技術驅動的自由注射成型(FIM)工藝。該平臺使製造商能夠在投資傳統金屬模具之前快速、經濟高效地對複雜的注射零件進行原型製作。 挑戰 金屬注塑模具的生產成本高,耗時長 在金屬注射成型(MIM)中,金屬粉末與塑膠粘合劑混合,形成原料,然後注射到金屬模具中。原料的磨蝕性對工具的品質提出了很高的要求,而MIM過程的複雜性通常導致需要多次迭代。Fraunhofer希望為公司提供一條快速、經濟有效地測試新概念的途徑,並轉向Nexa3D和自由注射成型(FIM)提供解決方案。 “Nexa3D 自由注射成型為我們提供了完美的工具,以支持創新型公司測試新概念和新材料。”——Sebastian Hein, Fraunhofer IFAM解決方案 優勢: 能夠在10天或更短的時間內提供原型金屬零件 顯著降低了原型加工成本 增加設計自由度 去風險發展,創新3D列印注射模具,使用xMOLD樹脂和自由注射成型 Fraunhofer受到其他公司使用自由注射成型(FIM)的啟發,決定引入XiP桌面3D印表機和xMOLD樹脂。這種緊湊的平臺是在MIM中通常遇到的產品尺寸範圍內列印模具的理想解決方案,xMOLD模具樹脂在高性能材料成型方面有著良好的記錄。 收益—複雜金屬零件的設計週期縮短為2周 通過使用Nexa3D的XiP3D印表機和xMOLD材料採用自由注射成型(FIM),Fraunhofer IFAM團隊為客戶帶來了許多好處。 快速成型:自由注射成型(FIM)使Fraunhofer IFAM能夠快速成型MIM零件,用於客戶演示和驗證測試。FIM零件的材料性能已被證明與傳統鋼模具生產的材料性能密切匹配,確保了準確的性能評估。 節省時間和成本:自由注射成型(FIM)允許Fraunhofer IFAM大幅減少試驗模具生產所需的時間和成本。XiP印表機的速度非常快,可以在當天進行列印和注入,同時與傳統的試驗工具相比,可以節省超過75%的成本和時間。 降低開發和創新的風險:Fraunhofer IFAM已經證明,FIM與巴斯夫的黃金標準Catamold原料相容,使客戶能夠使用特性良好的材料進行開發和創新。 客戶影響-演示複雜設計的原型MIM 金屬注射成型(MIM)一直受到原型選擇稀缺的困擾。傳統的基於AM的方法,無論是基於粉末還是基於粘合劑,都不能用於評估在脫脂和燒結過程中成型部件的流動路徑、模內應力模式或翹曲。因此,當想要驗證零件設計和工藝參數時,注塑機不得不投資於高成本的試驗模具。Fraunhofer IFAM已經完成了第一個專案-圍繞GE噴氣發動機支架建模-展示了Freeform注射成型的簡單性,速度和設計自由度。 Fraunhofer IFAM團隊決定採用一種適合注射成型的支架設計,並使用巴斯夫著名的現成Catamold 17-4PH原料作為材料。採用XiP列印可溶注射模具,採用Arburg 320注塑機完成成型。 該專案確認了自由注射成型(FIM)的幾個重要方面: 模具設計時間從幾天縮短到幾個小時,因為模具不需要合併分割線,頂銷或滑動功能。 測試模具的製造可以在幾天內完成,而不是幾周。 自由注塑成型可以使用標準的注射成型機和原料進行,並提供與傳統金屬注射成型相媲美的材料品質。 源文摘自:Nexa3D
了解更多
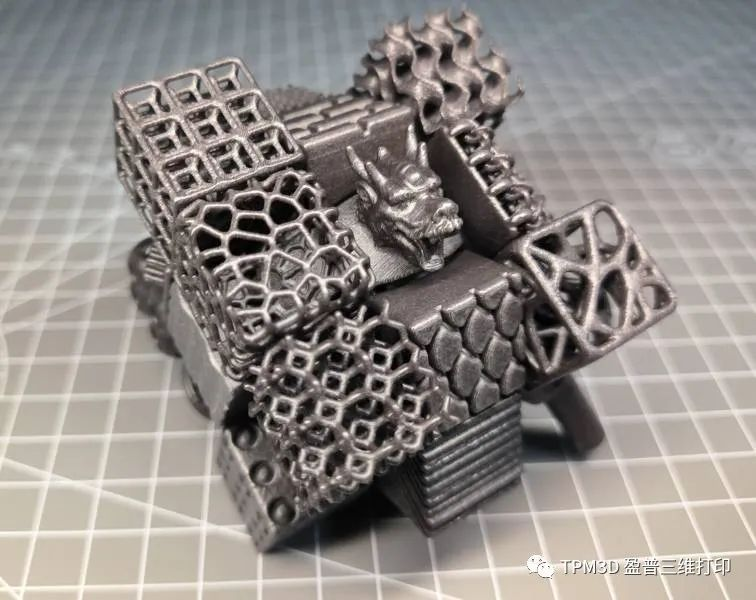
SLS前来挑战!超高复杂度的3D打印魔方
我们都知道,通常3D打印技术对于模型的复杂程度并不敏感,但越是复杂和精细的模型,对打印设备的成型精度和细节表现力的要求就越高。今天我们用SLS 3D打印技术挑战打印一个高难度的魔方。 这个魔方由27个不同的小块组成,其中包括:核心块1个、对接块6个(表面纹理特征)、边角块8个(镂空/晶格结构特征)、棱边块12个(装配一体打印结构/精细结构特征),这27块分别打印,然后组装在一起。 图01 魔方由27个不同特点的小块组成 这个魔方模型非常考验打印设备的整体打印精度和一致性,因为27块小块在打印后要实现组装,并顺畅旋转,就需要保证打印结果与设计预留间隙一致。除此之外,每种类型的小块都有不同的结构特点,考察不同方面的打印能力。 其中,核心块要求打印后具备良好的机械强度、光滑且耐磨的表面,从而满足旋转顺畅和长期使用的要求;6个对接块对打印强度和表面效果有同样要求的同时,也要求体现出设备对小的凹凸纹理的打印能力。 图02 对接块还要求设备能打印出表面的凹凸纹理 8个边角块则要求设备在打印各种细小镂空和晶格结构时,激光扫描的精细度和控制能力,以及在清粉时,小间隙是否能够清理彻底。 图03 边角块由各种类型的镂空和晶格结构组成 12个棱边块主要可以分为2类:装配结构的一体成型和精细结构的打印,目的是分别体现装配结构和精细结构的打印效果,同时也考察了材料在打印后的机械强度和耐久性。 图04 锁链、弹簧、球头、螺纹、铰链、齿轮6种装配结构一体打印 图05 小船、龙头、薄壁、细柱、螺旋、镂空6种精细结构打印 对于这个比较复杂的魔方,我们决定使用盈普高复用性的Precimid1172Pro BLK灰黑色尼龙12材料打印,这款材料具备优秀的综合性能,打印零件的表面效果好、颜色稳定、耐磨耐用,新粉比例可以低至20%,通用且性价比高。打印设备是盈普P360 SLS激光烧结增材制造系统,层厚选择为0.1mm。 图06 盈普P360和PPS清洁高效生产解决方案 图07 激光烧结打印中 经过试打印和工艺参数调整,我们成功的将27个小块打印出来,并使用PPS实现清洁高效的拆件和清粉。 图08 清粉照片 再经过喷砂处理后,每一个小块的打印效果完美呈现了出来。 图09 核心块与对接块 图10 边角块 图11 棱边块 所有小块都可以顺利组装,并实现良好的旋转效果。 图12 组装后的效果 现在我们可以说SLS 3D打印技术已经完成了这项超复杂的魔方打印挑战,但为了优化整个魔方的外观效果,提升产品价值,我们还对它进行了化学蒸汽平滑处理,抛光后的魔方表面光滑亮泽,颜色更深,并且旋转更加顺畅、防水耐用。最终实现了更棒的制作效果,挑战完美达成! 图13 最终经过化学蒸汽平滑处理后的魔方 源文摘自: 盈普三维
了解更多
ZEISS 三维扫描仪 | 3D打印 普立得科技
普立得科技成立于2004年,专注于工业级3D打印机与三维扫描,同时我们也是ZEISS GOM代理商,并提供3D打印及扫描的代工整合服务,特此加值整合相关软体,包含拓扑优化设计 、医疗影像分析、逆向工程 、3D检测等,期望推进积层制造的使用习惯为生产带来更多价值。





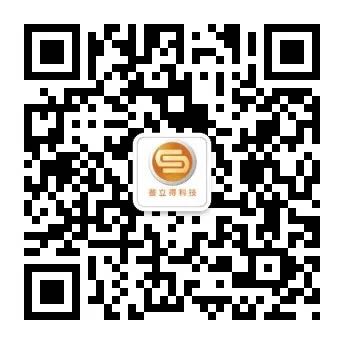
微信公众号
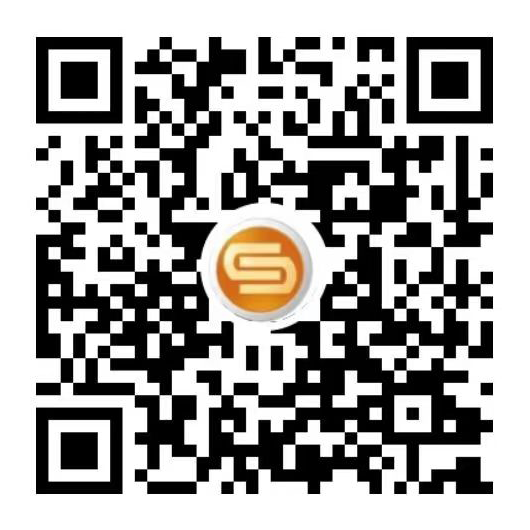
视频号
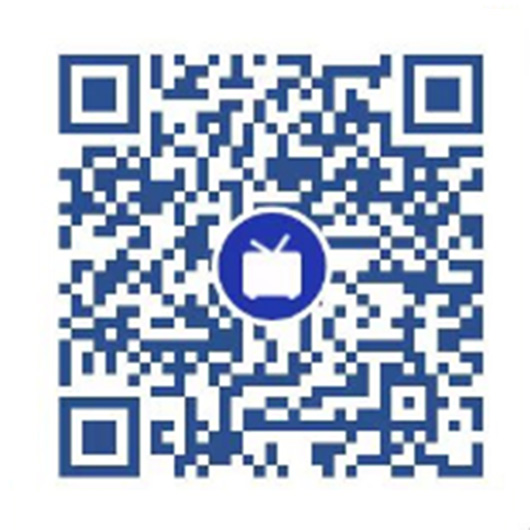
哔哩哔哩
您有什么疑问,或想咨询我们的产品与服务,请留下信息,我们会及时与您联系!
© 2021 普立得科技有限公司 All Rights Reserved 粤ICP备19059200号