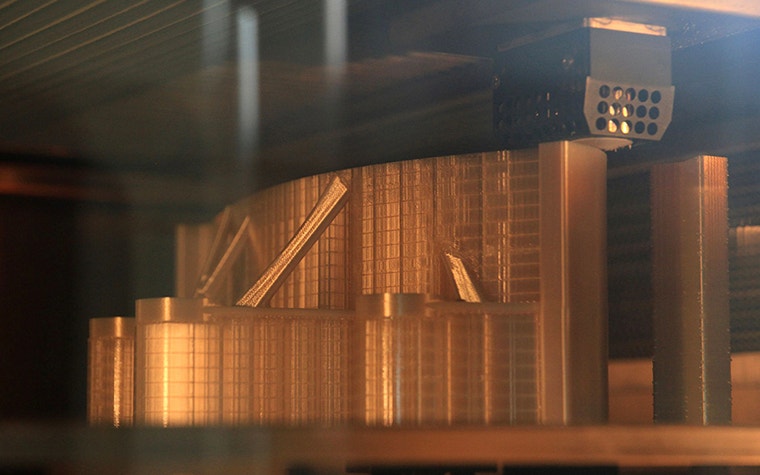
空中客车采用3D打印技术
发布时间:2023/02/01
- 访问量:
【概要描述】
说到改装飞机,时间是至关重要的。但是,当机舱中新设计的元件需要与现有组件集成时,像头顶舱末端的间隔板有时必须进行调整或重新设计。由于改造时间紧迫,空客正在寻找一种快速、智能的解决方案来小批量生产面板。Materialise的航空制造工厂采用量身定制的后期制作流程,提供了理想的解决方案。
挑战
生产小批量定制零件,以满足紧迫的时间和质量要求
当航空公司更新其客舱布局时,现有组件和新组件之间通常会有间隙。这些需要用定制面板连接,以创造一个有吸引力的,无缝完成的内部。随着时间的推移,直到飞机能够重返天空产生收入,找到一种生产新零件的聪明方法——通常需要非常有限的数量——是至关重要的。
传统上,新的塑料零件是使用定制的注塑模具制造的。这个过程相对复杂,尤其是因为许多组件是高度专业化的。鉴于典型改造所需的零件数量有限,交付周期长,每个零件的成本高空中巴士渴望找到一种更快、更具成本效益的解决方案,用于商用飞机头顶储物箱旁边的隔板。
但是,无论成本和交付周期有多重要,在处理航空航天工业,尤其是商用飞机机舱时,它们并不是唯一的考虑因素。除了必须满足严格的质量要求才能被视为可以飞行,它们还必须满足严格的美学标准—空客在他们的A350 XWB客机上集成了3D打印部件在过去,但从来没有在乘客看得见的地方。这是一个将3D打印带入下一个前沿领域并进入飞机机舱的机会。
解决方案
利用定制的后期制作完成的航空制造业
使用3D打印直接生产间隔板给空客带来了许多重要的好处,其中最明显的是交付时间。对于小批量系列和定制零件,航空3D打印比传统制造提供了更快的上市时间,因为不需要之前的工具生产。
“我们认为这个项目是我们如何为航空航天业服务的一个很好的例子。它展示了Materialise如何提供超越3D打印的端到端流程。”
— Erik De Zeeuw,Materialise航空市场经理
设计优化是另一个受欢迎的好处。然而像格子一样的内部结构传统的注射成型技术增加了复杂性和成本,3D打印可以轻松解决这一问题,使实现轻质仿生面板和优化组件质量成为可能。
隔板是在Materialise使用FDM技术生产的。
在表面处理方面,Materialise的后期制作流程确保了3D打印部件符合空客严格的美学要求——一旦生产出来,面板就会按照空客机舱的要求进行喷漆,所有这些都使用了空客批准的阻燃材料。
Materialise的航空市场经理Erik De Zeeuw总结说:“我们认为这个项目是我们如何为航空业服务的一个很好的例子。它展示了Materialise如何提供超越3D打印的端到端流程。这是一个严格的质量流程,从设计到完成,融入了每一个细节。”
基础在于精心打造的质量管理体系,其结果由Materialise制造工厂持有的多项认证证明:ISO 9001制造认证、TISAX汽车行业认证、ISO 14001环境管理认证,以及两项关键的航空航天行业认证:EN9100和EASE 21。后者是来自欧盟航空安全局(EASA)的生产组织批准(POA)。
结果呢
重量轻15%的飞行就绪型美观面板
我们与空中客车公司携手合作,生产了该公司有史以来第一个可用于机舱的3D打印零件。结合增材制造和我们的后期生产流程,面板通过了所有空客客舱装饰和表面检查。由于3D打印使设计优化成为可能,间隔板获得了完全仿生设计认证——这是空中客车公司第一个这样做的机舱部件,也是该公司不断努力优化部件重量的成功结果。与旨在用于传统生产方法的原始设计相比,3D打印面板轻了15%。
Materialise和空客之间的紧密合作是这个项目成功的A关键。正如Erik指出的,“我们在Materialise的目标是成为空客值得信赖和可靠的增材制造供应商。我们通过利用我们的软件和技术在设计和生产过程中共同创新来实现这一目标,同时也通过无缝整合空客自己的工作方式来实现这一目标。"
通过这个项目,增材制造展示了它可以为航空公司带来的巨大利益,它将价格、质量和美观以及快速交付周期完美结合。
空中客车采用3D打印技术
【概要描述】
说到改装飞机,时间是至关重要的。但是,当机舱中新设计的元件需要与现有组件集成时,像头顶舱末端的间隔板有时必须进行调整或重新设计。由于改造时间紧迫,空客正在寻找一种快速、智能的解决方案来小批量生产面板。Materialise的航空制造工厂采用量身定制的后期制作流程,提供了理想的解决方案。
挑战
生产小批量定制零件,以满足紧迫的时间和质量要求
当航空公司更新其客舱布局时,现有组件和新组件之间通常会有间隙。这些需要用定制面板连接,以创造一个有吸引力的,无缝完成的内部。随着时间的推移,直到飞机能够重返天空产生收入,找到一种生产新零件的聪明方法——通常需要非常有限的数量——是至关重要的。
传统上,新的塑料零件是使用定制的注塑模具制造的。这个过程相对复杂,尤其是因为许多组件是高度专业化的。鉴于典型改造所需的零件数量有限,交付周期长,每个零件的成本高空中巴士渴望找到一种更快、更具成本效益的解决方案,用于商用飞机头顶储物箱旁边的隔板。
但是,无论成本和交付周期有多重要,在处理航空航天工业,尤其是商用飞机机舱时,它们并不是唯一的考虑因素。除了必须满足严格的质量要求才能被视为可以飞行,它们还必须满足严格的美学标准—空客在他们的A350 XWB客机上集成了3D打印部件在过去,但从来没有在乘客看得见的地方。这是一个将3D打印带入下一个前沿领域并进入飞机机舱的机会。
解决方案
利用定制的后期制作完成的航空制造业
使用3D打印直接生产间隔板给空客带来了许多重要的好处,其中最明显的是交付时间。对于小批量系列和定制零件,航空3D打印比传统制造提供了更快的上市时间,因为不需要之前的工具生产。
“我们认为这个项目是我们如何为航空航天业服务的一个很好的例子。它展示了Materialise如何提供超越3D打印的端到端流程。”
— Erik De Zeeuw,Materialise航空市场经理
设计优化是另一个受欢迎的好处。然而像格子一样的内部结构传统的注射成型技术增加了复杂性和成本,3D打印可以轻松解决这一问题,使实现轻质仿生面板和优化组件质量成为可能。
隔板是在Materialise使用FDM技术生产的。
在表面处理方面,Materialise的后期制作流程确保了3D打印部件符合空客严格的美学要求——一旦生产出来,面板就会按照空客机舱的要求进行喷漆,所有这些都使用了空客批准的阻燃材料。
Materialise的航空市场经理Erik De Zeeuw总结说:“我们认为这个项目是我们如何为航空业服务的一个很好的例子。它展示了Materialise如何提供超越3D打印的端到端流程。这是一个严格的质量流程,从设计到完成,融入了每一个细节。”
基础在于精心打造的质量管理体系,其结果由Materialise制造工厂持有的多项认证证明:ISO 9001制造认证、TISAX汽车行业认证、ISO 14001环境管理认证,以及两项关键的航空航天行业认证:EN9100和EASE 21。后者是来自欧盟航空安全局(EASA)的生产组织批准(POA)。
结果呢
重量轻15%的飞行就绪型美观面板
我们与空中客车公司携手合作,生产了该公司有史以来第一个可用于机舱的3D打印零件。结合增材制造和我们的后期生产流程,面板通过了所有空客客舱装饰和表面检查。由于3D打印使设计优化成为可能,间隔板获得了完全仿生设计认证——这是空中客车公司第一个这样做的机舱部件,也是该公司不断努力优化部件重量的成功结果。与旨在用于传统生产方法的原始设计相比,3D打印面板轻了15%。
Materialise和空客之间的紧密合作是这个项目成功的A关键。正如Erik指出的,“我们在Materialise的目标是成为空客值得信赖和可靠的增材制造供应商。我们通过利用我们的软件和技术在设计和生产过程中共同创新来实现这一目标,同时也通过无缝整合空客自己的工作方式来实现这一目标。"
通过这个项目,增材制造展示了它可以为航空公司带来的巨大利益,它将价格、质量和美观以及快速交付周期完美结合。
- 分类: 产业应用
- 发布时间:2023-02-01 11:03
- 访问量:
说到改装飞机,时间是至关重要的。但是,当机舱中新设计的元件需要与现有组件集成时,像头顶舱末端的间隔板有时必须进行调整或重新设计。由于改造时间紧迫,空客正在寻找一种快速、智能的解决方案来小批量生产面板。Materialise的航空制造工厂采用量身定制的后期制作流程,提供了理想的解决方案。
挑战
生产小批量定制零件,以满足紧迫的时间和质量要求
当航空公司更新其客舱布局时,现有组件和新组件之间通常会有间隙。这些需要用定制面板连接,以创造一个有吸引力的,无缝完成的内部。随着时间的推移,直到飞机能够重返天空产生收入,找到一种生产新零件的聪明方法——通常需要非常有限的数量——是至关重要的。
传统上,新的塑料零件是使用定制的注塑模具制造的。这个过程相对复杂,尤其是因为许多组件是高度专业化的。鉴于典型改造所需的零件数量有限,交付周期长,每个零件的成本高空中巴士渴望找到一种更快、更具成本效益的解决方案,用于商用飞机头顶储物箱旁边的隔板。
但是,无论成本和交付周期有多重要,在处理航空航天工业,尤其是商用飞机机舱时,它们并不是唯一的考虑因素。除了必须满足严格的质量要求才能被视为可以飞行,它们还必须满足严格的美学标准—空客在他们的A350 XWB客机上集成了3D打印部件在过去,但从来没有在乘客看得见的地方。这是一个将3D打印带入下一个前沿领域并进入飞机机舱的机会。
解决方案
利用定制的后期制作完成的航空制造业
使用3D打印直接生产间隔板给空客带来了许多重要的好处,其中最明显的是交付时间。对于小批量系列和定制零件,航空3D打印比传统制造提供了更快的上市时间,因为不需要之前的工具生产。
“我们认为这个项目是我们如何为航空航天业服务的一个很好的例子。它展示了Materialise如何提供超越3D打印的端到端流程。”
— Erik De Zeeuw,Materialise航空市场经理
设计优化是另一个受欢迎的好处。然而像格子一样的内部结构传统的注射成型技术增加了复杂性和成本,3D打印可以轻松解决这一问题,使实现轻质仿生面板和优化组件质量成为可能。
隔板是在Materialise使用FDM技术生产的。
在表面处理方面,Materialise的后期制作流程确保了3D打印部件符合空客严格的美学要求——一旦生产出来,面板就会按照空客机舱的要求进行喷漆,所有这些都使用了空客批准的阻燃材料。
Materialise的航空市场经理Erik De Zeeuw总结说:“我们认为这个项目是我们如何为航空业服务的一个很好的例子。它展示了Materialise如何提供超越3D打印的端到端流程。这是一个严格的质量流程,从设计到完成,融入了每一个细节。”
基础在于精心打造的质量管理体系,其结果由Materialise制造工厂持有的多项认证证明:ISO 9001制造认证、TISAX汽车行业认证、ISO 14001环境管理认证,以及两项关键的航空航天行业认证:EN9100和EASE 21。后者是来自欧盟航空安全局(EASA)的生产组织批准(POA)。
结果呢
重量轻15%的飞行就绪型美观面板
我们与空中客车公司携手合作,生产了该公司有史以来第一个可用于机舱的3D打印零件。结合增材制造和我们的后期生产流程,面板通过了所有空客客舱装饰和表面检查。由于3D打印使设计优化成为可能,间隔板获得了完全仿生设计认证——这是空中客车公司第一个这样做的机舱部件,也是该公司不断努力优化部件重量的成功结果。与旨在用于传统生产方法的原始设计相比,3D打印面板轻了15%。
Materialise和空客之间的紧密合作是这个项目成功的A关键。正如Erik指出的,“我们在Materialise的目标是成为空客值得信赖和可靠的增材制造供应商。我们通过利用我们的软件和技术在设计和生产过程中共同创新来实现这一目标,同时也通过无缝整合空客自己的工作方式来实现这一目标。"
通过这个项目,增材制造展示了它可以为航空公司带来的巨大利益,它将价格、质量和美观以及快速交付周期完美结合。
原文来自网络
扫二维码用手机看
最新消息
ZEISS 三维扫描仪 | 3D打印 普立得科技
普立得科技成立于2004年,专注于工业级3D打印机与三维扫描,同时我们也是ZEISS GOM代理商,并提供3D打印及扫描的代工整合服务,特此加值整合相关软体,包含拓扑优化设计 、医疗影像分析、逆向工程 、3D检测等,期望推进积层制造的使用习惯为生产带来更多价值。





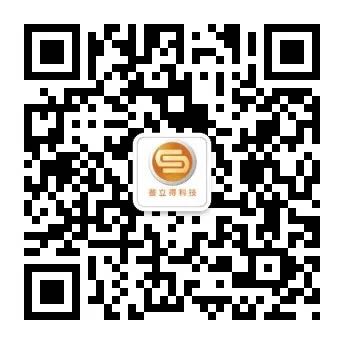
微信公众号
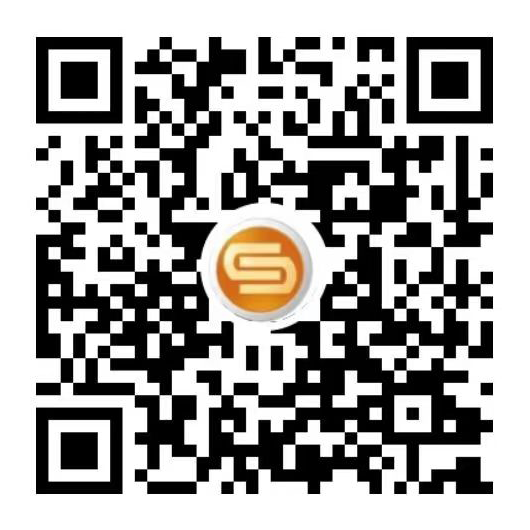
视频号
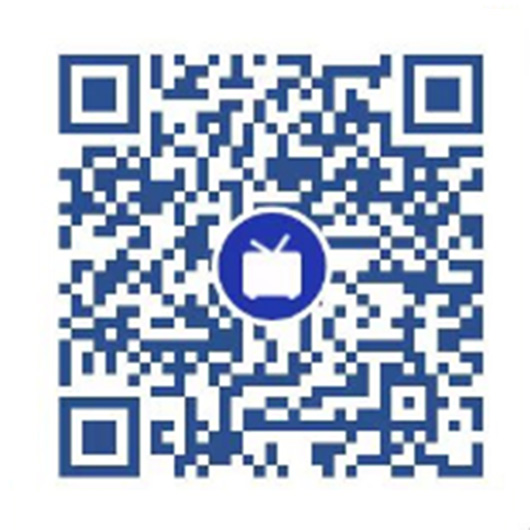
哔哩哔哩
您有什么疑问,或想咨询我们的产品与服务,请留下信息,我们会及时与您联系!
© 2021 普立得科技有限公司 All Rights Reserved 粤ICP备19059200号