产业应用
普立得科技成立于2004年,专注于工业级3D列印与3D扫描逆向工程,并提供3D打印、三维扫描的代工整合服务,同时也代理德国知名品牌Zeiss 三维扫描仪。
普立得科技在台湾地区设有3个区域办事处,大陆地区设有8个区域办事处,截至目前销售超过900套设备。普立得科技的3D打印/3D扫描技术正在改变和加快亚洲地区设计和制造的发展。 3D打印技术的出现是对生产方式的一种革新,客制化的特性能够为复杂设计降低成本,同时也能提供更低成本的零部件,使企业降低成本、获取更高利润。
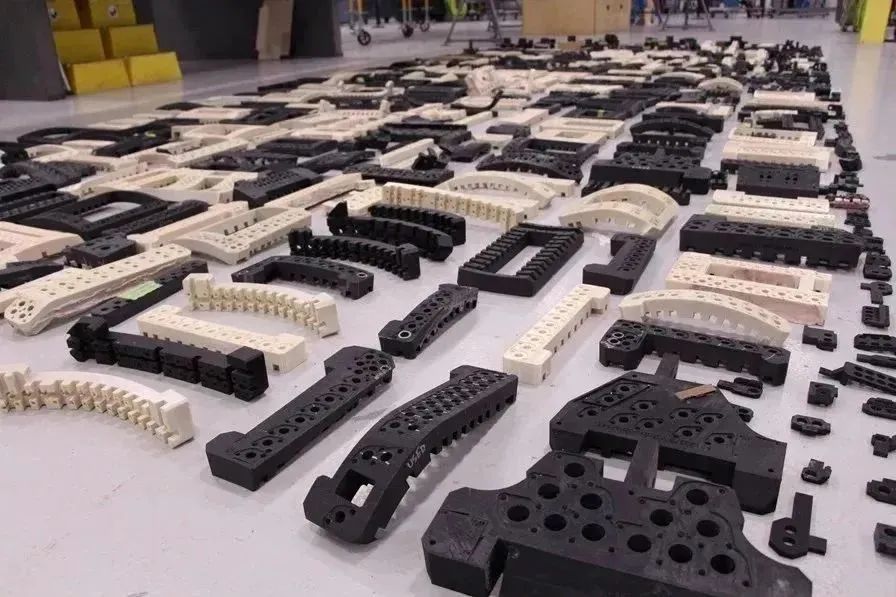
可持续生产丨“硬核”FDM 3D 打印钻孔导向器助力超音速飞行
Boom Supersonic通过实现可持续超音速飞行,重新定义了商业航空旅行。作为Boom公司久负盛名的商务班机,Overture致力于在速度、安全性和可持续性方面达到行业标准。 Overture使用100%可持续航空燃料,从而实现净零碳排放,同时飞行速度可达当今最快客机的两倍。XB-1是该公司2020年推出的一款演示飞机,目前正在进行净零碳排放飞行测试。 挑战 想要连接XB-1演示飞机的各种零件就需要在机身结构上钻出大量孔洞。单独钻孔非常耗时,因为要对每个孔洞进行定位。除此之外,在动力钻孔过程中,还需要夹具来支撑钻孔工具,并为每个孔洞支撑起正确的角度。钻孔导向器是一个切实可行的解决方案,但传统的金属导向器成本高昂,同时交付周期漫长 解决方案 Boom公司工程师3D打印了多孔洞钻孔导向器,用于在机身结构的较大区域内精准定位紧固件孔洞 这款多孔洞钻孔导向器由Fortus 450mc™和F900™打印机使用FDM® Nylon 12CF碳纤维和ULTEM™ 9085树脂材料打印而成。 此类坚固刚硬的热塑塑料具有足够的强度和硬度,可支撑动力钻孔工具,同时能够精准定位孔洞。 用于生产XB-1演示飞机的3D打印钻孔导向器样品 效果 仅以一台典型的钻孔导向器为例,Boom便节省了近3,700美元(约24,000RMB)的材料成本,并将交付周期从数周缩短至数日。到目前为止,在生产XB-1演示飞机的过程中,已采用3D打印技术生产超过700台孔导向器,节省的材料成本十分可观。相比机加工,内部采用3D打印而节省的交付时间对生产计划也带来了非常积极的影响。 通过XB-1机身上的碳纤维增强塑料(CFRP)和钛合金叠层,用于钻紧固件钻孔的3D打印钻孔导向器
了解更多
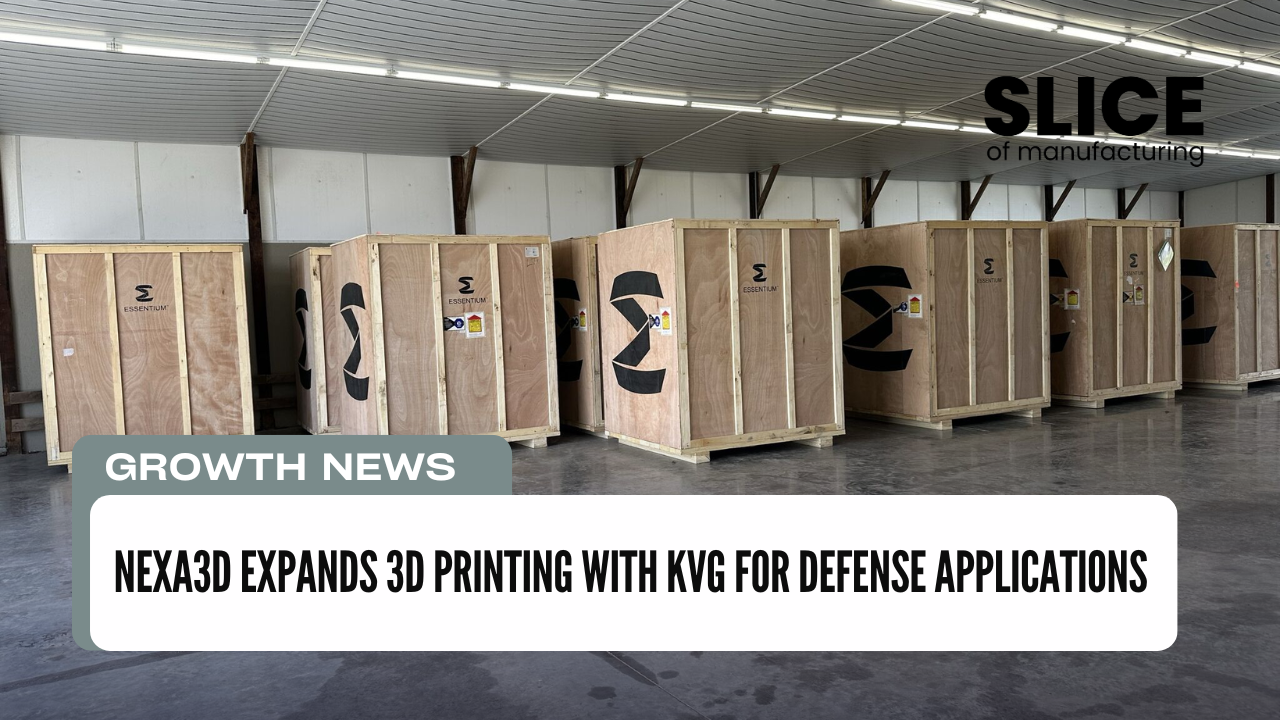
Nexa3D 利用 KVG 扩展了 3D 打印技术,用于国防应用
15 台全新高速挤出(HSE)系列3D打印机添加者 KVG型促进国防的可部署制造。 HSE 180 和 HSE 280i 型号可直接在现场提高高精度部件的生产。 收购随之而来 Nexa3D的的购买 Essentium(Nexa3D公司),增强其材料组合和高速打印能力。 源 (美国商业信息) 值得注意的引述: “我们很高兴将更多的Nexa3D的HSE系列3D打印机添加到我们的产品群组中,并将这些系统集成到我们的运营中。 - 约翰·,KVG创始人兼首席执行官 “将我们的 HSE 180 和 HSE 280i 模型部署到 KVG 证明了我们致力于突破 3D 打印技术界限的承诺。” - 伊莉莎·泰佩尔, Nexa3D 首席政府官 我们的看法: Nexa3D和KVG之间的合作有望彻底改变全球军事和国防部件的制造方式。通过利用尖端的3D打印技术,此次合作不仅强调了敏捷制造解决方案在关键领域日益增长的重要性,而且还体现了技术战略投资如何提高运营效率和准备程度。随着对快速、现场制造的需求不断攀升,这些举措对于在竞争日益激烈的国防工业中保持领先地位至关重要。Nexa3D和KVG的这一举措可能会激发其他行业进一步采用先进的制造技术,以寻求类似的效率提升。
了解更多
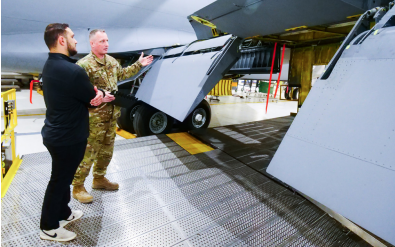
缅因州空军国民警卫队使用Essentium技术提高战备状态
第101空中加油联队印制飞行控制维修训练辅助器材,帮助维持警卫的熟练程度 摘要 缅因州空军国民警卫队第101空中加油联队(ARW)使用Essentium高速挤压(HSE™)3D打印平台和Essentium PCTG打印飞行控制维修训练辅助工具,以帮助维护 传统警卫的熟练程度。这些训练辅助工具: •提供对稀有零件的快速和可重复访问 •通过加强训练减少飞机坠落的情况 •提高飞行关键维修的安全性 概述 在第101次ARW,传统警卫每月有一个周末参加飞机维修训练。在那些日子里,他们专注于职业培训,包括走过各种部件的维修过程,以提高他们的熟练程度和经验。 Jason Howes军士长解释道:“拥有训练有素的警卫是没有价值的。”。“他们从能够把手放在产品上,了解结果会是什么样子,以及获得肌肉记忆中获得的信心是非常宝贵的。” 当传统的警卫没有得到熟练的训练时,后果可能是严重的。不正确的维修可能会永久损坏飞机零件,需要更换。如果它在供应链中不可用,可能会导致飞机坠毁。在最坏的情况下,如果零件没有正确修复,并且这是飞行安全问题,您可以失去了飞机,甚至失去了生命。 挑战 不幸的是,维护周期和飞机维修并不总是与训练周末一致。在没有飞机维修的日子里,传统的警卫必须阅读技术数据理解指导,然后在库存材料而不是实际零件上执行该过程。虽然这种方法在为警卫做准备,对实际零件进行培训,使他们有信心准确快速地修理零件。 传统警卫训练的一个部件是外侧副翼平衡片。这个部件是一个关键的飞行控制部件,有几个铰链点连接到飞机硬件上。这些连接点经常磨损,要进行维修,警卫必须加工新孔,安装衬套,检查精度,并安装它们,使外侧副翼平衡片恢复到原始出厂规格。然而,备用副翼平衡片的使用极为有限,通常仅用于现实世界的维修需求。再加上军事单位常见的人员流动,副翼平衡片中留住经验丰富的专业人员可能很难维持。 解决方案 为了确保现有的警卫能够熟练地修理外侧副翼平衡片,第101 ARW创建了一个训练辅助工具。使用这个零件的比例模型,警卫可以使用适用于组件的技术数据来修复它,就像他们拥有实际零件一样。 使用Essentium HSE 180 ST 3D打印机,第101 ARW的工程师在一个周末内创建了培训辅助工具。对该零件的唯一要求是,当铝部件压入其中时,它必须保持其尺寸。由于成本低、表面光洁度好和冲击强度高,第101届ARW的工程师选择使用Essentium PCTG。 Howes解释道:“对于这个应用程序,我们选择Essentium而不是其他打印机,因为它打印速度更快,外部尺寸更准确。”。“材料成本也比较低。” 成果 自从训练辅助器材投入使用以来,使用过辅助器材的警卫给予了积极的反馈。由于它是一个复制品,对援助的训练很好地转化为实际的组成部分。这一宝贵的工具也引起了当地其他军事部门的注意,如缅因州陆军国民警卫队,他们开始要求为他们的旋转飞机提供类似的训练辅助设备。HSE目前被用作跨职能部队的乘数,可以塑造整个联合部队的未来战备状态。 训练有素的警卫可以延长飞机零件的使用寿命,减少飞机坠落的情况,消除飞行安全问题,甚至防止人员伤亡。像外侧副翼平衡翼片辅助这样的训练辅助设备可以具有这样的价值,对于第101次ARW的工程师来说,这只是一个开始。
了解更多
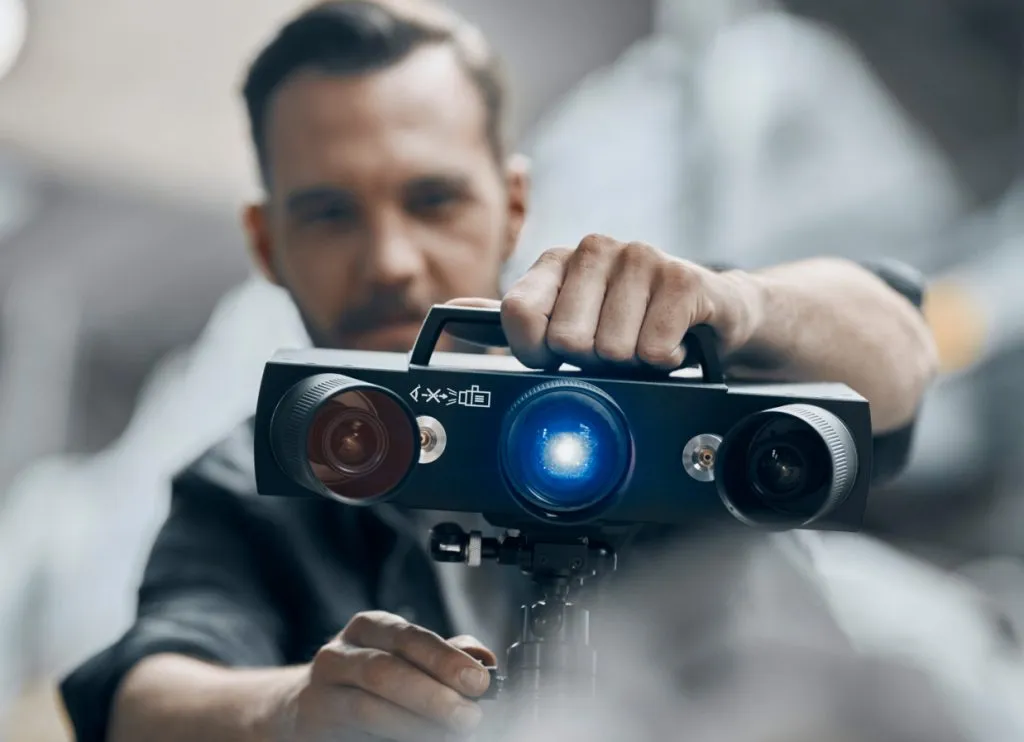
光学案例|交通运输 - 三维扫描并逆向游艇备件
Tollycraft游艇年代久远,节流阀损坏,但缺少原始零部件。CAD Micro公司使用ATOS Q对游艇的节流阀进行扫描,并将生成的STL数据用于精确的3D打印,制作所需备件。 本章,我们的合作伙伴CAD Micro将展示如何利用ATOS Q进行逆向工程设计。使用可移动扫描仪对节流阀进行扫描,并将生成的STL数据用于精确的3D打印。 游艇的预制备件制作 CAD MicroSolutions Inc. 在公海上执行了一项特殊的任务,确切地说,是在一艘1974年的Tollycraft游艇上。这艘游艇中两根油门杆中的一根已经断裂,必须更换掉。然而,由于制造年代久远,非常难以寻找到原始的配件。 ▲图一:在游艇上进行三维扫描 ▲图二:不完整的节流阀杆 ATOS Q生成可靠的STL数据 扫描数据的质量决定了逆向工程是否成功。尤其是,精确细节的捕捉以及难以触及区域的扫描非常具有挑战性。 ATOS Q搭配ROT480旋转台可以完美地完成这项任务。无论是设备的设置还是扫描的过程都非常快速、简便。即使在现场需要移动设备,ATOS Q的扫描结果也非常出色,可以轻松获得高精度的扫描数据。 「借助ATOSQ的先进技术,我们能够精确捕捉到微小细节以及深孔区域,这对逆向工程来说至关重要。没有这些,我们就不可能对油门杆进行精确建模。」 ——CAD MicroSolutions Inc. 将三维扫描数据用于3D打印 利用蔡司检测软件,可以提供现有节流阀必要几何形状的数字化副本。生成的STL数据可直接导入逆向工程软件,用于3D打印。因此,CAD Micro公司可以制作出第二个与原始节流阀相似的3D打印件。将3D打印部件组装起来后即可以发挥其原来的功效。
了解更多
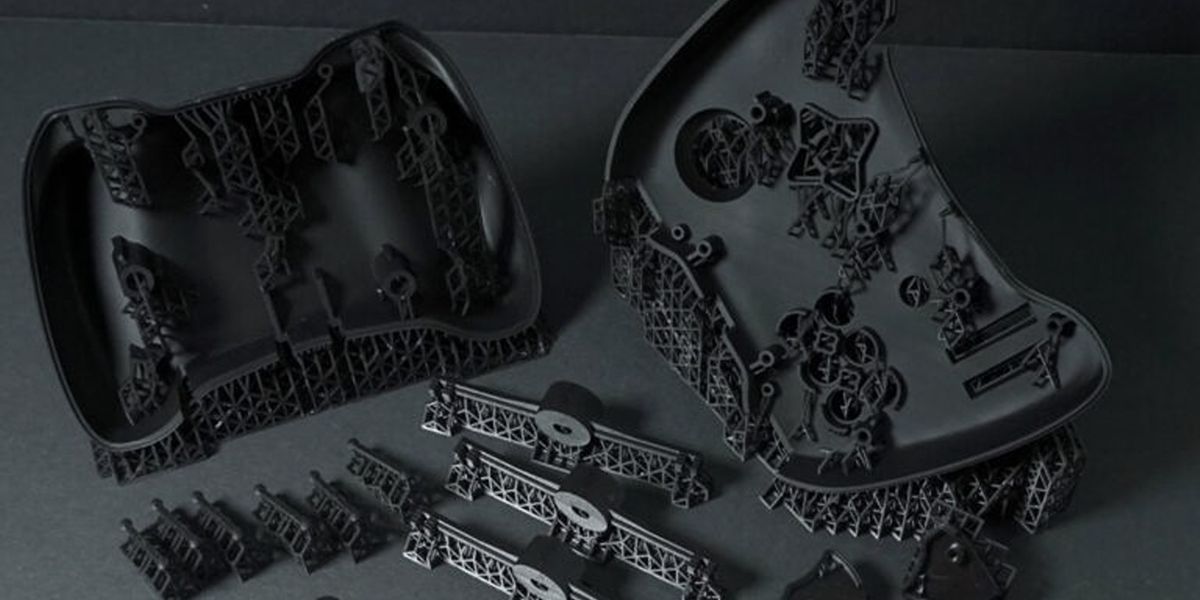
使用 XiP 桌面 3D 打印机彻底改变飞行类比
该团队与MotoCilino的工程专家合作,在创纪录的时间内将手持式飞行控制器商业化 在一个速度、准确性和成本效益至关重要的行业中,Yawman Flight 与MotoCilino工程服务公司和 Nexa3D 合作,以应对设计和开发首款用于飞行类比的手持控制器的挑战。Yawman Arrow 融合了传统的手持游戏控制器和各种尺寸飞机上的独特飞行控制。Arrow 专为精度和多功能性而设计,将传统的操纵杆、桌面油门象限和方向舵踏板等全部整合到手持式外形中。 其结果是产品创新和制造效率的突破,XiP桌面3D打印机在取得成功方面发挥了关键作用。 挑战 快速且经济高效地创建高保真原型,而无需在开发过程的早期投资工具 Yawman Flight 面临着在大量时间和预算限制下创建独特的飞行模拟器控制器的挑战。主要目标是开发一种首创的手持式飞行模拟器控制器,并快速、经济高效地完成项目,而无需投资昂贵的注塑模具。此外,该团队要求所有元件具有高质量的表面光洁度和机械性能,因此快速且经济地实现类似注塑成型的质量对于项目的成功至关重要。 Yawman Flight 的目标客户群是飞行模拟爱好者和航空业专业人士,他们需要高质量、逼真的飞行模拟体验。飞行模拟行业需要高质量的产品,这些产品能够满足零件公差和机械性能的严格规范,以提供真正逼真的模拟体验。 “XiP 使我们能够创造出一种最终产品,在表面光洁度和性能方面表现出类似注塑成型的质量,但没有成本和较长的交货时间。如果我们在原型设计阶段使用另一种制造方法,我们会延迟一年之多。Thomas Nield,Yawman Flight 工程主管 溶液 XiP 因其准确性和打印速度而被证明是完成这项工作的理想工具 Yawman Flight 与 MotoCilino 工程服务公司合作,在创纪录的时间内开发了一款独特的控制器,经历了 17 次不同的设计反覆运算,然后在短短几周内验证了最终组装。最终的原型控制器由36个不同的元件组成,所有这些元件都是使用xABS3843高性能树脂在XiP桌面3D打印机上打印的。 MotoCilino 的团队选择在 XiP 上打印元件,因为打印机的可靠性和高打印质量,使用模仿最终生产级 ABS 机械性能的高性能级树脂。事实上,成品控制器的视觉美感和机械性能与那些模制的元件几乎没有区别。Motocilino 的所有者 Paul Cilino 说:“在 XiP 上打印使我们能够在使用另一台桌面 SLA 打印机时将元件交付给 Yawman 团队所需的时间减半,而且 XiP 上的打印质量非常出色。 效益 将上市时间缩短了近一年,并以极低的成本交付了高保真原型 该团队能够完成设计,并快速且经济高效地交付具有类似注塑成型的表面光洁度和机械性能的高质量原型。成品元件包括超过 36 个打印元件,所有元件在光洁度和机械性能上都与注塑成型元件几乎没有区别。因此,该团队现在已准备好在 2023 年 7 月进行商业发布时进行规模化生产,此前在今年早些时候的测试版发布期间收到了巨大的初始需求。
了解更多
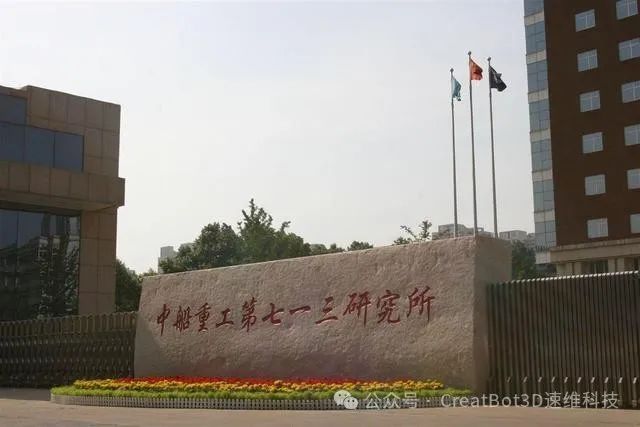
速维科技CreatBot助力中国船舶集团第七一三研究所实施工业4.0战略,降本增效实现智能制造
Part1速维科技CreatBot助力中国船舶第七一三所实现新型工业化转型 中国船舶集团有限公司第七一三研究所(后续简称中船重工713所)创建于1963年4月,隶属于中国船舶集团有限公司。 建所50多年来,出色完成了多项国家重点项目,先后获得国家、国防科工委、省部级等各类科技奖励400多项。 中船重工713所业务范围广泛,产品多样,实力雄厚,研发产品涉及船舶与海洋设备,新能源设备及交通运输设备等领域。 (图为客户背景) 从2021年底国务院印发《“十四五”智慧制造发展规划》以来,中船重工713所积极响应国家号召,落实国家的中国制造2025与工业4.0战略。 中船重工713所研发的产品既有涉及船舶与海洋的大型工业设备零部件,也有风电光伏等设备中的阀门等一些需要耐高温坚韧的小型零部件。 在集团深入研究,并调研了市面上多家3D打印机企业后,中船重工713所最终慎重选择了我司旗下的D1000,D600Pro2, F430NX, PEEK-250等多款工业级3D打印机,以满足多维度,多品类,多领域工业产品设计与制造的需求,助力研究所的智慧设计转型。 所有设备在春节前已经交付给中船重工713所,在使用了近1个月后我在2024年新春开工后收到了中船重工713所美好的产品使用体验反馈。 (图为中船重工713所采购设备的交付安装现场) Part2速维科技CreatBot完善的交付服务 不仅有送货到门的物流服务,速维科技还提供包括针对超大机器安排吊车从窗户运输至室内,现场的安装,调试,软件升级,产品培训及任何问题的售后到场回应等一系列的暖心交付体验。 通过CreatBot打印机的配套切片软件CreatWare,中船重工713所的工作人员可以轻松在多平台上快速地完成3D模型的切片操作,且软件可以根据模型形状和大小,自动精准优化打印路径。 通过CreatBot打印机的印表控制软件CreatCloud,中船重工713所的工作人员可以轻松地控制整个3D打印流程,在打印大尺寸模型,使用大卷耗材,连续打印时效果尤其显著。 (图为速维技术人员对中船重工713所员工进行3D打印机配套软件使用培训) (图为速维技术人员指导中船重工713所员工进行3D打印机配套软件使用) Part3速维科技CreatBot 超大尺寸工业级3D打印机 传统的FDM 3D打印设备的成型尺寸普遍在400x400x400mm以下,而在船舶控制系统中,一些零部件的尺寸普遍都接近1m左右,市面上常规的3D打印机根本无法满足需要,而大尺寸模型打印的精度和速度问题也始终是研究人员的顾虑。 此次中船重工713所通过采购速维科技的大尺寸工业级3D打印机D600Pro2及超大尺寸工业级3D打印机D1000来满足以上场景的应用。 D600Pro2大尺寸工业级3D打印机是制造大型和全尺寸零件、原型、工具、模具、夹具和夹具的理想机器。 而D1000 3D打印机则是目前世界上构建体积达到1立方米的超大尺寸打印机之一。 为了实现高效率高精度的大尺寸打印,D1000和D600Pro2系列均采用滑台模块设计,其厚度是普通导轨的5倍,它可以保证经过百万次运动惯性冲击后,机器导轨也不会变形或失去精度,相比普通导轨的长度达到1000mm,使用半年后的精度丢失问题,此种设计可以极大程度保证打印机打印的高精度,保证高质量的打印,同事减少企业的维护成本和时间成本。 以中船重工713所设计的太阳能电池板清洗车的零部件打印为例,其需要超高性能和高速度的印表场景,此时需要着重解决马达转速、定位精度等关键挑战。 D1000和D600Pro2均采用闭环环伺服电机,回应速度快,无惯性,无延时。 充分满足工业级别对于生产制造的高精度要求的同时,还可以克服打印中的失步问题,及减少打印过程中的热量和噪音。 D1000与D600Pro2还配备了最新的智慧自动升降双挤出机,喷头温度高达 420 °C, 且喷头套件可快速拆卸更换,方便维修和更换不同 尺寸的喷头套件。 它不仅可以结合水溶性支撑以最快的速度打印巨大的PLA原型,而且可以打印ABS、PC、尼龙、碳纤维、 柔性的或更高性能的材料,打印后皆能直接应用。 此外D1000及D600Pro2上的断点恢复与耗材检测,封闭的加热室,自动调平系统等功能等都为中船重工713所在船舶升降设备零部件及太阳能电池板清洗车零部件的原型设计过程中提供助力。 (图为中船重工713所采购的D1000 3D打印机) Part4速维科技CreatBot 超高温专业3D打印机 此次向中船重工713所交付的设备中还包含F430NX,PEEK-250这两款未发售的新机型。 这些设备卓越的性能和稳定的质量使得中船重工713所迫不及待地希望在产品公开发售前抢先体验。 由于船舶升降设备所需的复材性能较高,而PEEK此种耐高温,耐磨损及耐腐蚀等特性常常作为航空航天,汽车电子,工业制造等领域的首选。 速维科技即将推出的PEEK-250 3D打印机,其喷头温度高达480°C,热床温度可以达到200°C,腔室温度可达到180°C,遥遥领先于同行的同系列产品,可以满足几乎所有的高性能热塑性高分子材料打印温度的要求。 而F430NX则定位于专业桌面独立双喷头3D打印机,将大大增强3D打印体验。 目前这两款机器正在速维相关的合作伙伴企业内测中,我们会在今年5月的TCT亚洲3D打印、增材制造展览会上发布这两款新产品.
了解更多
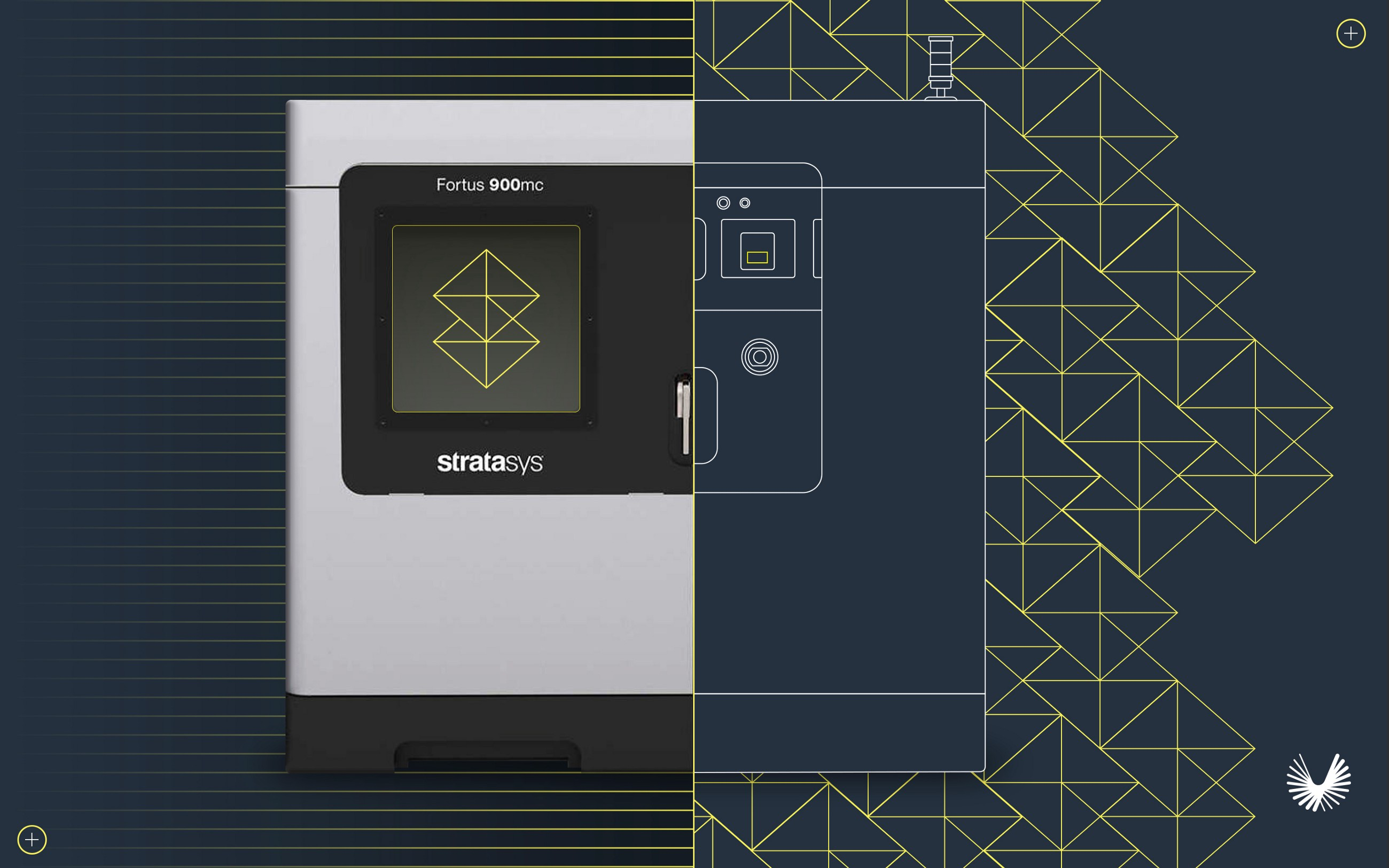
Boom的3D打印飞机部件揭示了制造业的未来
Boom是如何利用3D打印来优化机库的性能和效率的? 3D打印技术已经席卷了世界制造业。从消费品设计到医学建模,越来越多的公司看到了3D打印在快速原型设计和制造方面的价值。 也许没有哪个行业能像航空航天那样产生如此深远的影响。波音公司预计通过在787梦想客机上3D打印钛部件,每架飞机可节省300万美元。霍尼韦尔通过增材制造节省了7个多月的重新设计时间。空中客车公司能够在头顶储物舱中制造出比以前轻15%的隔板。 Boom两年多前开始使用3D打印,这是与全球领导者Stratasys合作的一部分。从那时起,该公司已经制造了数百个3D打印零件、工具和原型,并节省了数千小时的工作时间。Stratasys和Boom最近宣布将合作伙伴关系延长七年至2026年,并将继续为复杂问题实施创造性解决方案。 Boom和许多类似公司的利益是深远的。三个最显著的好处包括节省时间、金钱和体重。许多飞机零件固有地具有复杂的几何形状,部分原因是空间和重量限制。在3D打印之前,复杂的零件是从一块实心材料中铣削出来的,通常会变得极其昂贵、费力和耗时。 3D打印对Boom的影响有多大?我们分享了五种独特的印刷部件,这些部件照亮了飞机制造的未来: 压力调节器支架 该压力调节器支架用于安装前起落架舱液压系统中调节备用压力的部件。如果这个部件是按传统要求用铝制成的,则需要6周以上的时间,成本为2000美元。这件飞行硬件只花了9.5个小时的打印时间,材料成本为70美元。 遥测连接安装 该部件在遥测连接验证测试期间用作设备支架。作为测试的一部分,工程团队在科罗拉多州14000英尺的派克峰上安装了设备,并确认可以在200英里外保持飞机和地面站之间的可靠遥测连接。 飞行控制试验台 该飞行控制试验台用于测试水平尾翼执行器偏转的机制,能够以极低的费用进行快速彻底的安全测试。尽管这些印刷部件不会用作飞行硬件,但它们使工程师能够确保飞行硬件执行器按预期工作。 压缩机排气管 快速原型设计的另一个很好的例子是,这种压缩机引气管道在发动机测试期间被用来重新引导发动机核心的空气,并作为测试件来确保飞行过程中的最终零件配合。如果没有3D打印,像这样的零件可能会失去特色,这一过程需要使用许多不同的零件才能获得最有效的形状。 这个传统的铝制零件的设计要复杂得多,大约需要4周和4000美元。对于Boom来说,这部分只需要14个小时和150美元。 装满飞行硬件的托盘 这项94小时的打印工作由70多个零件组成,是在Stratasys F900机器上完成的,机器上有一个装满飞机上各种系统飞行硬件的托盘。得益于电气、机翼、飞行控制、液压和机身系统,与传统制造方法相比,仅这一项工作就节省了数千美元和数周的交付周期。 随着越来越多的公司继续采用3D打印作为制造解决方案,Boom继续寻找新的、创新的方法来使用这项多功能技术。随着该公司致力于建造历史上最快的商用客机Overture,飞行部件、工具和原型的3D打印将发挥强大作用。
了解更多
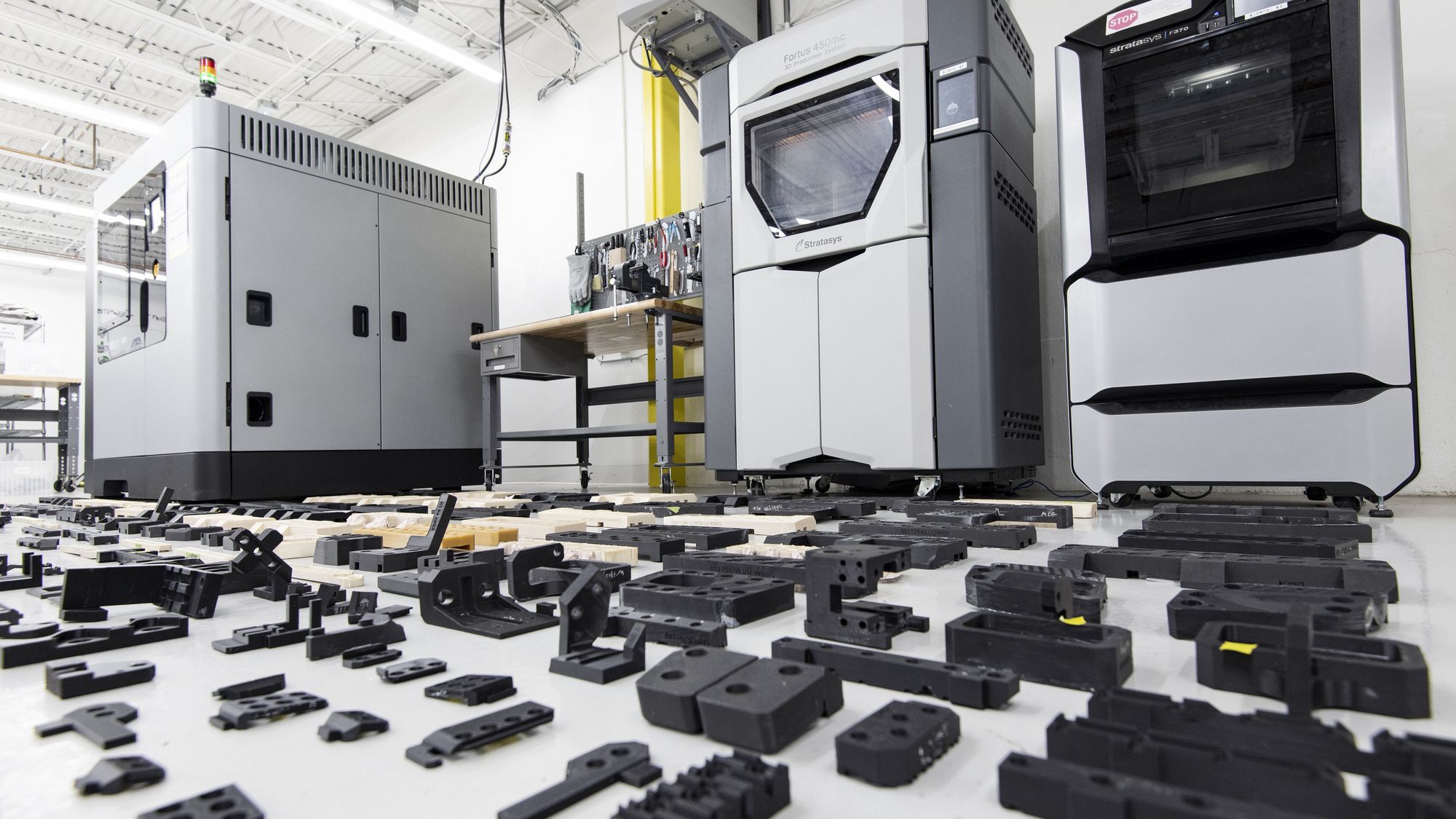
3D打印——飞行的未来
对于建造XB-1的团队来说,3D打印在建造的每个阶段都被证明是无价的。 强大的发动机。强金属。坚固的起落架。 当我们想到飞机零件时,我们想象的是几乎坚不可摧的材料和组件。3D打印的零件不会出现在脑海中。但材料和3D打印机的进步正在加速变革,使3D打印成为原型设计、工具和飞行硬件的完美选择,更不用说更换零件、内饰甚至厕所固定装置了。 3D打印正在改变我们设计和制造飞机的方式。 对于建造Boom超音速演示机XB-1的团队来说,3D打印在建造的每个阶段都被证明是无价的。飞机上安装了300多个独特的零件。但3D打印对XB-1的贡献远不止零件制造。 三台3D打印机,三种需求 在XB-1构建的早期,Boom团队与Stratasys合作,探索3D打印(也称为增材制造)的选择。该项目着眼于3D打印,以满足三种不同的需求:功能原型、工具支持和飞行硬件的按需制造。三台打印机满足了建造的需要:Stratasys F900、450mc和F370。 F900、450mc和F370。 Stratasys F900是一架机器的战马,在Boom的机库中占据了中心舞台。F900打印多种材料,包括ULTEM 9085和ULTEM 9085CG。两者都是阻燃、高性能树脂热塑性塑料,具有高强度重量比、优异的耐热性和高冲击强度。该团队使用9085打印钻头块,并使用9085 CG打印已经安装在XB-1上的数百个零件。9085 CG具有合格证书,与标准材料相比,具有更好的可追溯性和过程控制,是飞机零部件制造的理想选择。 Stratasys Fortus 450mc还可打印多种材料。该团队指定它用于用FDM尼龙12 CF打印钻头块,这是一种非常坚固的材料。FDM尼龙12 CF浸渍有碳纤维,是打印硬质钻头的理想选择。在XB-1钛合金后机身的建造过程中,该团队使用了数百个钻块,连夜打印。它不仅加快了构建速度,还减少了团队的停机时间。 Stratasys F370通常使用ASA打印,这是一种经济、低强度的材料,非常适合快速成型和测试配件。该团队用F370打印了原型,以减少任何意外碰撞(零件干扰或零件连接或接触的不匹配区域)的风险,并安装到现有的飞行硬件上。3D打印零件的测试配件支持设计改进,因此当团队最终制造零件时,每个零件都像手套一样合身。 功能原型:设计完美配合 在XB-1建造的第一阶段,首要任务之一是制造飞行控制系统的原型部件,包括机构和机械部件。每个原型的目标是验证零件是否适合,以及是否与其他零件一起工作。有了原型,团队可以在投入宝贵资源制造零件之前检查是否存在冲突(连接零件不匹配)。 Stratasys F900是一款能够打印多个 通过在几个小时内打印多个迭代并微调设计,该团队保持了构建的进度。他们还避免了当零件从制造商那里到货时出现不合适的情况。通过将这些功能保留在内部,团队将停机时间降至最低。 Stratasys F900是一款能够在其巨大的3'x2'x3'打印床上打印多个零件的机器。 所有的打印机都投入到制作从燃料歧管到发动机支架的原型的工作中。例如,该团队3D打印了外侧发动机前支架,以检查与左右发动机的配合情况。经过多次迭代,他们在配合检查中成功验证了设计。 此引擎的多次3D打印迭代 该团队为遮篷3D打印了这个原型闩锁机构,以确保运动学符合预期。 工具:实现更高的精度并减少潜在的损坏 在XB-1的建造过程中,该团队利用F900和450mc的能力打印了550多个钻头块。这些块支撑着钛机身与其他印刷夹具的精心组装,包括驾驶舱舱壁的夹具。 该团队使用计量学方法用这些块钻孔,从而提高了精度。该团队以更高的准确性减轻了对飞机的潜在损坏。 通过使用3D打印的钻块,该团队保持了建造进度,同时也减轻了钛制后机身的任何潜在损坏。 如果没有3D打印,钻块的交付周期将在几周左右,更不用说用铝制造数万美元了。通过内部3D打印,这些相同的块只需几天就能以更低的成本打印出来。 此图显示了团队使用3D打印的钻头块精确钻孔的许多地方. Metallics:承受热量的钛3D打印零件 由于行业的重大进步,现在几乎可以使用任何材料进行3D打印。银、光聚合物、立体光刻材料(环氧树脂)甚至钛都可以应用于3D打印。 Boom与VELO3D建立了合作关系,生产金属零件,否则需要数周甚至数月的时间才能加工。该公司总共为XB-1 3D打印了21个零件,包括XB-1的一些最复杂的钛零件:可变排气阀(VBV)系统的歧管,该系统从发动机压缩机中排出多余的空气。 在VBV歧管的情况下,使用机械加工、焊接或铸造等传统制造方法是不切实际的。他们只能使用3D打印实现所需的零件几何形状。 Boom与VELO3D的合作使XB-1上安装了21个3D打印金属零件。 轻型3D打印零件:航空航天工程师的游戏规则改变者 3D打印不仅在建造过程中节省了时间和资源,还减轻了飞机的重量——这改变了所有航空航天工程师的游戏规则。由于飞机重量与燃料消耗直接相关,航空航天工程的目标是制造一种重量轻、同时满足所有安全要求的飞机。重量越轻的飞机燃烧的燃料越少,因此重量的任何减轻都会产生巨大的影响。 根据材料的选择,3D打印零件可以比用钢和铝制造的传统零件轻得多。在拥有340多个独特3D打印部件的XB-1上,重量的减轻带来了巨大的不同。 现在,制造团队已经将XB-1交付给地面和飞行测试团队,他们正将注意力转向Overture的设计和制造,这是Boom未来的超音速客机。对于Overture来说,3D打印的可能性似乎是无穷无尽的,除了原型设计、加油和飞行硬件外,还可以选择机舱内部、飞行甲板和厨房的3D打印部件。3D打印的进步为这些可能性提供了动力,这将为降低生产成本、加快制造进度以及通过制造更轻的飞机来减少排放开辟新的途径。
了解更多
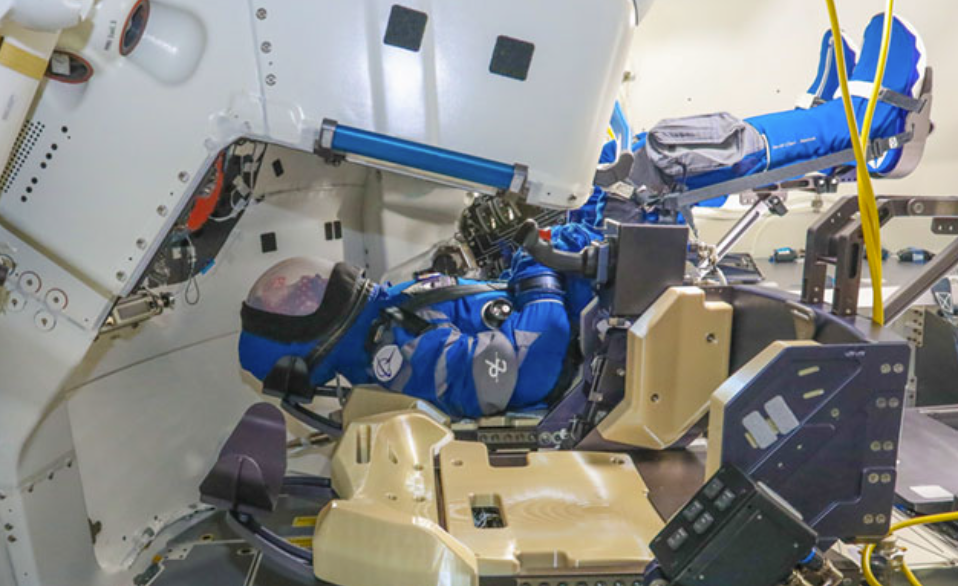
rp+m 3D 打印了波音 Starliner 航天器的座椅
3D打印服务局快速原型和制造(rp+m)通过社交媒体透露,其俄亥俄州总部的一个工程师团队已经3D打印了波音Starliner飞船使用的座椅,该飞船于19年2022月<>日在NASA的无人飞行测试中发射到国际空间站(ISS),并在六天后安全返回地球。 “五月对rp+m来说是一个繁忙的月份,”LinkedIn上的帖子写道。“我们很自豪能成为美国国家航空航天局(NASA)和波音公司这一具有里程碑意义的任务的一部分,该任务于19月<>日成功发射了星际客机,并于上周重新进入。增材制造『实际上』正在改变世界,朋友们! 此外,rp+m 增材制造工程师 Cameron Rogers 不仅证实该公司是 Starliner 3D打印座椅的幕后推手,他还表示 rp+m 打印了“三套不同的座椅,尺寸略有不同”。 对于这项任务,rp+m 依靠 Stratasys 的熔融沉积建模(FDM)技术,该技术与专用3D打印机和生产级热塑性塑胶配合使用,以制造坚固、耐用且尺寸稳定的部件。具体来说,Stratasys FDM 的商业负责人 Tom Leach 表示,该团队使用了 F900大型体积打印机和 ULTEM 9085 树脂3D印表材料来制造座椅。 美国宇航局宇航员观看联合发射联盟阿特拉斯五号火箭与波音公司的CST-100 Starliner航天器在轨道飞行测试-2任务之前被推出到发射台。图片由NASA/Joel Kowsky提供。 由波音公司制造的乘员太空运输(CST)-100 Starliner是一类两艘部分可重复使用的航天器,旨在将乘员运送到国际空间站和其他低地球轨道(LEO)目的地,作为航空航天巨头对NASA商业乘员计划的贡献的一部分。与SpaceX一起,波音公司的任务是建造一艘航天器来取代航天飞机,并使美国摆脱长达十年的依赖俄罗斯联盟号太空舱进入轨道站。 SpaceX 在9年乘坐猎鹰 2020 号火箭发射首次载人任务后取得了进展,现在定期将机组人员送往国际空间站。然而,波音公司在试图让Starliner启动并运行实际的载人任务时遇到了一系列问题。 最后一次试飞被称为轨道飞行试验2(OFT-2),是 OFT-1 测试的重做,该测试于2019年发射,但在 Starliner 因软件逆境导致太空舱在发射后不久烧毁推进剂而发生故障,未能到达国际空间站后过早结束。 波音公司解决了这些问题,并让Starliner准备好在2年夏天在 OFT-2021上发射,但在计划升空前不久的飞行前检查显示,太空舱服务模块推进系统上有13个卡住的阀门没有回应命令。路透社最近的一份报告称,由于Aerojet Rocketdyne是Starliner服务模块推进系统的官方硬件供应商,两家公司因燃油阀故障而发生冲突。 从那时起,波音公司花了大约八个月的时间来解决导致航班延误的问题。一旦航天器上的阀门问题得到解决,OFT-2终于起飞了。这对rp+m团队来说是个好消息,他们终于在轨道上见证了3D打印座椅。 座位上是「火箭人罗茜」,这是波音公司的人体测量测试设备,以二战的铆工罗西命名,是对在航空航天和人类航天领域开辟道路的女性的颂歌。罗茜被绑在Starliner上进行飞行测试,这次是为了帮助航天器在飞行的各个阶段保持重心。 “她是一个 180 磅重的欧洲棕褐色测试设备,旨在代表人类身高和体重尺寸的第 50 个百分位,”商业船员计划船员和货物住宿子系统负责人 Melanie Weber 说。“罗茜的第一次飞行提供了数百个关于宇航员在飞行过程中将经历的数据点,但这一次她将帮助保持Starliner在上升、对接、脱离和着陆过程中的重心。即使是你驾驶的汽车也必须保持重心,否则它可能会翻车。 对于OFT-2,先前连接到Rosie的15个传感器的航天器数据捕获埠用于从放置在座椅托盘上的传感器收集数据,座椅托盘是将所有乘员座椅固定到位的基础设施。传感器可以捕获数据,以表征所有四个乘员座椅的运动,乘员舱总工程师Dan Niedermaier解释说。 罗茜穿着波音蓝色宇航服和红色波点头巾,还戴着由95岁的梅·克里尔(Mae Krier)手工缝制的配套口罩,梅·克里尔(Mae Krier)是现实生活中的罗茜,她17岁时在西雅图的一家波音工厂帮助制造飞机。 Starliner 人体测量测试设备 Rosie the Rocketeer 在 Starliner 太空舱的轨道飞行测试 19 期间戴着手工缝制的 Rosie 主题 COVID-2 口罩和亲笔签名的 Rosie 围巾。图片由波音公司提供。 波音公司与美国宇航局的合同涵盖了无人驾驶的OFT-1和OFT-2任务,以及预计将于今年年底或明年初与两名宇航员Barry “Butch” Wilmore和Suni Williams一起发射的机组飞行测试。第一次载人试飞将从佛罗里达州卡纳维拉尔角太空部队基地的太空发射场-41乘坐联合发射联盟阿特拉斯五号火箭升空,就像OFT-2一样。 一旦试飞完成,美国宇航局将开始对Starliner航天器和系统进行认证,以执行空间站的载人任务。定期、长期的商业船员轮换任务使该机构能够继续在轨道实验室上进行研究和技术调查,并为未来探索月球和火星奠定基础。 作者:Vanesa Listek3D打印机3D打印3D打印材料太空3D打印
了解更多
ZEISS 三维扫描仪 | 3D打印 普立得科技
普立得科技成立于2004年,专注于工业级3D打印机与三维扫描,同时我们也是ZEISS GOM代理商,并提供3D打印及扫描的代工整合服务,特此加值整合相关软体,包含拓扑优化设计 、医疗影像分析、逆向工程 、3D检测等,期望推进积层制造的使用习惯为生产带来更多价值。





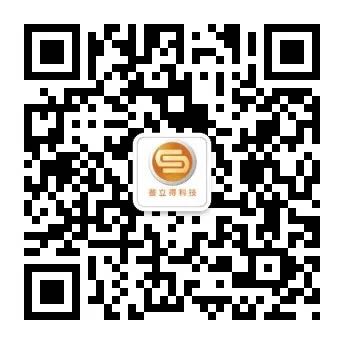
微信公众号
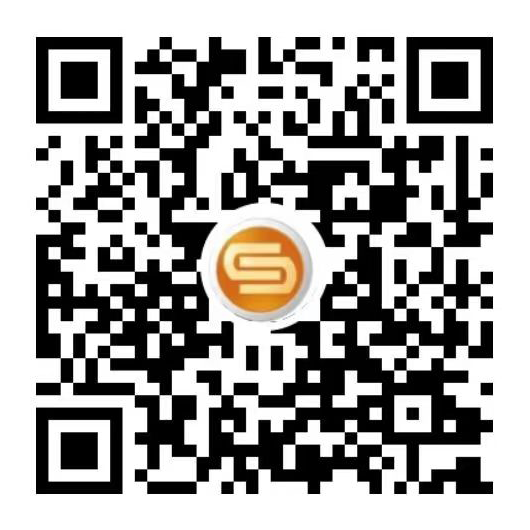
视频号
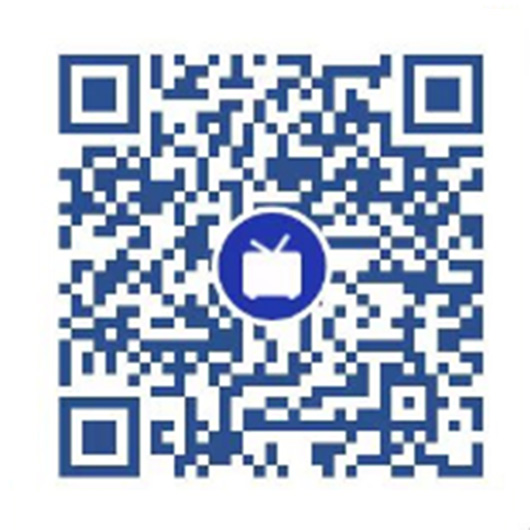
哔哩哔哩
您有什么疑问,或想咨询我们的产品与服务,请留下信息,我们会及时与您联系!
© 2021 普立得科技有限公司 All Rights Reserved 粤ICP备19059200号