产业应用
普立得科技成立于2004年,专注于工业级3D列印与3D扫描逆向工程,并提供3D打印、三维扫描的代工整合服务,同时也代理德国知名品牌Zeiss 三维扫描仪。
普立得科技在台湾地区设有3个区域办事处,大陆地区设有8个区域办事处,截至目前销售超过900套设备。普立得科技的3D打印/3D扫描技术正在改变和加快亚洲地区设计和制造的发展。 3D打印技术的出现是对生产方式的一种革新,客制化的特性能够为复杂设计降低成本,同时也能提供更低成本的零部件,使企业降低成本、获取更高利润。
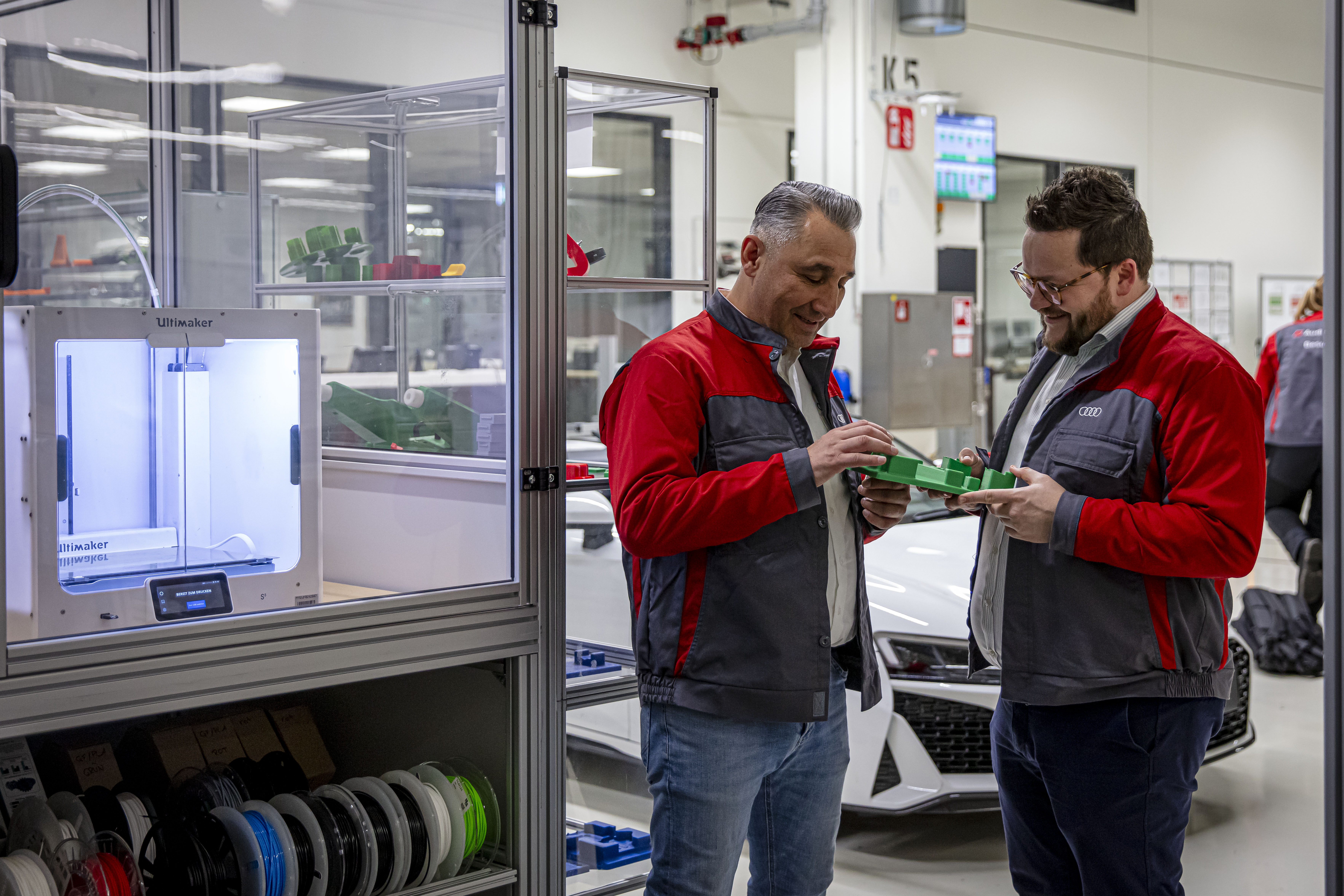
奥迪运动版:3D打印工具、夹具和固定装置只需一天而不是几周
当新款奥迪E-Tron GT推出时,位于德国海尔布隆的奥迪运动版Bôllinger Höfe工厂迅速需要近200个新的工具、夹具和固定装置进行生产。设计这些工具需要花费大量时间。外包生产有时可能需要数周到数月的时间。这就是设计自动化和3D打印为奥迪运动版提供无与伦比的工作流程的地方。 奥迪运动版Böllinger Höfe工厂是一家高端汽车生产工厂。他们的主要生产重点是高性能奥迪R8和全电动奥迪E-Tron GT。这些车是德国著名汽车制造商的crème de la crème。装配线上写满了德国的效率。裸露的笼子装在机器人平台上,安装在顶部轨道上。这列专车随后经过许多安装了特定订单零件的车站。很难发现两辆一模一样的车紧挨着,这使得整个操作更加令人印象深刻。 每个工作站都有有限的时间来组装零件并将其安装到汽车上。这就是为什么优化和高效的工作流程对机制至关重要的原因。定制工具、夹具和固定装置在使机械师的工作更快、更容易和符合人体工程学方面发挥着巨大作用。 奥迪运动版3D打印专家Cem Guelaylar表示:“我们为这里的工厂生产近800种工具、夹具和固定装置。”。“外包需要两三周、四周或几个月以上的时间。这取决于供应商和将订单带给供应商的过程。3D打印帮助我们在很短的时间内获得了这些工具。工人们来找我们说,我需要一个夹具来组装汽车。他需要一天的时间才能拿到这个工具。” 适用于不同应用程序的不同工具 有一些自定义工具可以帮助在安装过程中对齐零件。例如,用于安装车顶或汽车外部的徽标。这提高了最终车辆的一致性和质量,同时节省了每辆车的分钟数。质量控制工具确保所有汽车都符合奥迪的最高标准。这些定制夹具安装在汽车零件上,用于测量对准和公差。例如,奥迪运动版创建了一个自定义夹具,将抬头显示器(HUD)聚焦在汽车仪表板上。该夹具使用两个投射在已安装HUD上的激光器。当激光器对准时,意味着反射玻璃安装正确。 许多零件在安装到汽车上之前需要进行组装。在中央流体板上添加管道,在中央控制单元上添加电缆和散热器,等等。简单地放在工作台上处理这些零件会使任务变得非常困难。这就是奥迪运动版在工厂中使用许多固定装置的地方。这些固定装置将零件固定到位,便于快速组装。这些固定装置不仅节省了时间,而且对生产的一致性也有很大影响。其中许多固定装置的设计也对工人的人体工程学产生了积极影响。例如,将工具保持在更好的工作方向。 用几分钟而不是几小时设计零件 因此,当新的E-Tron GT推出时,制造近200种不同的工具、夹具和夹具面临着巨大的挑战。他们需要它们快速开始生产。设计这些工具需要花费大量的时间和专业知识。它们需要精确、用户友好且易于生产。这就是Trinkle的固定伙伴发挥重要作用的地方。Fixturemate是专门为创建装配夹具而设计的软件。将导入零件并将其设置为直角。然后,通过添加基板、零件需要支撑的位置和孔来创建夹具,以便将其安装到桌子上。还有一个现成工具库,如夹具。该软件对用户非常友好,任何人都可以使用它。虽然在传统的CAD软件中设计工具可能需要几个小时,但在fixturemate中只需要10-20分钟。 Guelaylar指出:“我们开始在这里生产奥迪E Tron GT全电动汽车。这款新车需要近200个固定装置和工具。Fixturemate帮助我们在短时间内带来了大量固定装置。”。“我们把零件放在Fixturemate中,几分钟内就可以把夹具从这个软件中取出。通常,在经典结构中,我们需要两个小时、三个小时、四个小时,这取决于零件的大小。Fixuremate非常容易使用。我们可以带学员来,向他们展示如何使用Fixturemate软件,他们可以直接使用这个软件,在短时间内把夹具带出来。” 奥迪运动版3D打印的优势 奥迪运动版不仅需要快速设计零件,还需要在很短的时间内生产出来。工具的外包生产成本高昂,也可能需要数周至数月的时间。这就是奥迪从3D打印室开始的原因。Ultimaker S5等多种打印机使奥迪运动版能够满足其工具需求。工具现在可以在一天内打印,只需花费很小的成本。无需要求报价、向供应商介绍情况以及等待零件生产和交付。当一个零件不符合要求时,可以直接进行改进和重印。 适合工作的材料 大多数固定装置都是用坚韧的PLA打印的。这种材料具有与ABS类似的弯曲和强度特性,但打印起来非常容易,没有ABS的挑战。还有使用TPU95a打印的用于保护汽车零件的工具。这种柔软的材料非常适合防止零件损坏。 得益于UltiMaker的生态系统,奥迪运动版还可以获得数百种第三方材料。这些材料通常具有非常特殊的特性。奥迪运动版使用的其中一种材料是ESD安全PLA,用于处理电子部件的固定装置。使用Ultimaker Cura可以轻松地使用这些材料准备3D打印,因为打印配置文件在市场上是免费的。 Guelayler继续说道:“我们使用Tough PLA是因为它便宜且易于使用。我们使用TPU主要用于保护和保护汽车零件。我们还使用ESD安全材料,有时还使用ABS或PETG。对我们来说,3D打印对我们的工厂和工人来说是一件非常快速和有用的事情。”。 奥迪运动版确实擅长不断提高效率。通过开始对工具进行3D打印,他们将工具生产成本降低了80%以上,同时在一天内而不是几周内将这些工具交付给工人。除此之外,通过使用fixturemate,奥迪运动版还使夹具设计变得简单快捷。您不需要专门的CAD设计师来创建夹具设计。从设计到3D打印,任何人都可以创建他们需要的工具,并开始受益。
了解更多
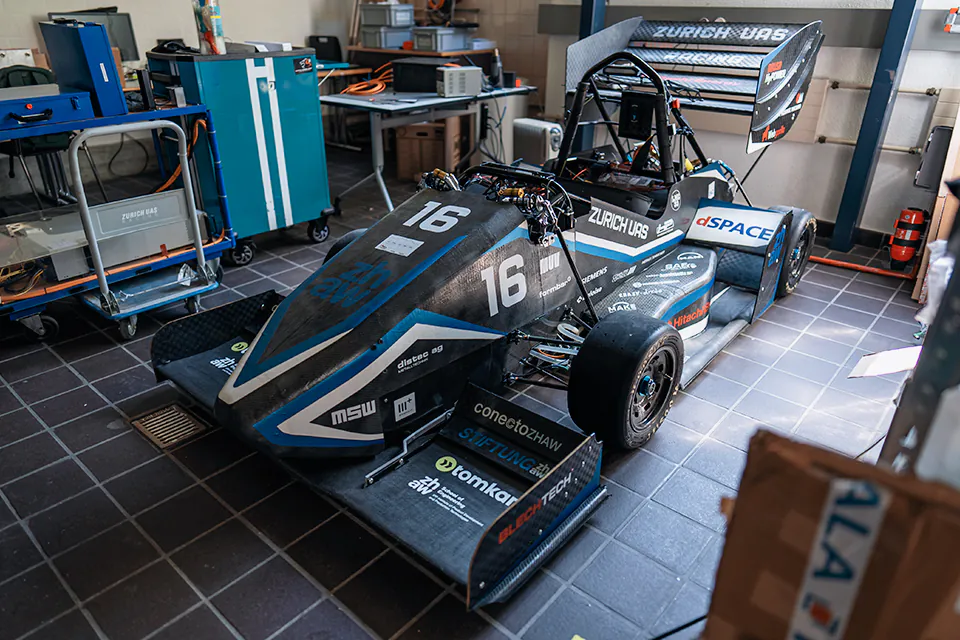
3D打印赛车零件的成功
来自苏黎世应用科学大学的瑞士学生正在建造一辆电动赛车,作为学生方程式比赛的一部分。该团队的成功秘诀包括Sintratec使用选择性激光烧结工艺制造的3D打印赛车部件。 瑞士队加大油门 在苏黎世应用科学大学在温特图尔,莫雷诺·阿皮塞拉(Moreno Apicella)欢迎我们,并带领我们进入一个工作室。除了他的硕士学位,这位机械工程学生还是苏黎世UAS赛车。该项目的目标是:在一年内制造一辆电动赛车,并获得至少三场欧洲学生方程式赛事的参赛资格。为了实现这一目标,这位崭露头角的工程师可以利用广泛的专业知识:我们目前有大约65名成员——大多数来自技术领域,但也有来自商业和经济研究的,阿皮塞拉说。年轻团队的目标是在2024年第四次参加比赛时,提高前几年的成绩。 Moreno Apicella是苏黎世UAS车队的队长,负责车辆的开发。 在赛道上亲身体验 Formula Student events是最大的国际工程竞赛,来自世界各地的学生在各个类别中相互竞争。使用他们自己开发的赛车,挑战是在动态和静态学科(如工程、性能、金融和美学)中战胜其他大学团队。“对我来说,这场比赛的独特之处在于它为学生提供了将理论知识应用于现实世界工程挑战的实践经验,”阿皮塞拉说。此外,与行业专业人士的密切合作也为团队提供了重要的交流和对未来职业的洞察。 大约65名ZHAW学生正在一年内开发一款电动赛车。 多样化的制造技术 在应用科学大学的车间里,摆放着过去两年的赛车和今年的车型,它们仍然由带车轮托架的管状框架组成。学生们必须在五月的首次展示前完成这辆车,然后在七月的活动开始。由于时间和预算紧张,Apicella和他的同学们也依靠增材制造技术来制造他们的车辆。这位机械工程专业的学生解释道:3D打印对我们的团队至关重要,因为它让我们能够快速制作原型,并以高精度定制复杂的零件。设计的自由度对于优化电动汽车尤其重要。 基于之前的车型,UAS车队正在打造其2024赛车。 来自3D打印机的组件 该团队使用了各种3D打印工艺,例如用于空气动力学包层压模具的熔融沉积建模(FDM)。然而,对于直接进入汽车的部件,需要更复杂的技术:我们对3D打印赛车部件的要求是良好的强度重量比和优异的机械性能,如防水组件,阿皮塞拉说。FDM很快达到极限,因此学生们转向选择性激光烧结(SLS)。作为赞助的一部分,瑞士SLS 3D打印机制造商Sintratec生产了几件产品。 Sintratec S3打印机用于制造PA12材料的各种部件。 符合人体工程学的方向盘 使用SLS的一个具体例子是方向盘。从一开始就很清楚将会使用加法技术。“我们采集了司机的手印,并进行了3D扫描,”阿皮塞拉描述道。基于这一点,我们能够从人体工程学的角度设计方向盘,使之完全适合他的手。完成CAD模型后,零件在S3辛特拉特克使用坚固的PA12尼龙,然后与电子设备一起内置在汽车中。由于这是一次性的定制,传统制造不仅成本更高,而且无法提供相同水平的定制。 方向盘是根据人体工程学设计的,并根据驾驶员的手部扫描进行3D打印。 防水冷却夹克 赛车的另一个3D打印元素是冷却夹克。传动系统的这一关键部件将冷却液引导至四台发动机,以调节它们的温度。在这里,Apicella的团队能够充分利用SLS 3D打印的设计自由:我们在冷却外套中集成了一个相当复杂的结构,特别是内侧,这位学生解释道。这种几何形状实际上不可能用加工工艺制造,这就是我们选择SLS的原因。由于学生方程式赛车规则规定,没有液体可以从赛车中泄漏,防水性能的PA12材料对于这个应用也是至关重要的。 PA12冷却套是设计、组装并内置于车辆中的。 汽车行业的潜力 选择性激光烧结等先进制造技术已经成为现代汽车开发和生产不可或缺的一部分。对于UAS车队来说,附加值是显而易见的。“我认为SLS对于汽车行业和我们项目的主要优势在于高度的设计灵活性和速度,”阿皮塞拉强调道。这使得该技术非常适合轻型结构部件、定制夹具和备件,最终有助于提高车辆性能和效率。在温特图尔,该团队相信SLS 3D打印将在赛道上的耐力测试中证明自己。 由于SLS等附加工艺,汽车零部件可以更自由地设计和更快地生产。 成功的瑞士合作 Sintratec支持公式学生项目3D打印的赛车零件,但目前还没有来自瑞士的。对于苏黎士UAS车队来说,地理上的接近使得合作更加明显和直接。Moreno Apicella总结说,与Sintratec的合作非常令人满意。我们拥有出色的技术支持,并且通过SLS,我们拥有了满足我们要求的最佳材料和工艺,有助于优化我们汽车的性能。对于学生来说,很明显,这种3D打印技术也将在未来广泛应用的项目中发挥关键作用。 高精度和鲁棒性相结合:SLS非常适合多种工业应用。 “我们将SLS技术用于3D打印赛车零件,因为它具有设计自由度和出色的机械性能。 Moreno Apicella团队经理 苏黎世无人机车队
了解更多
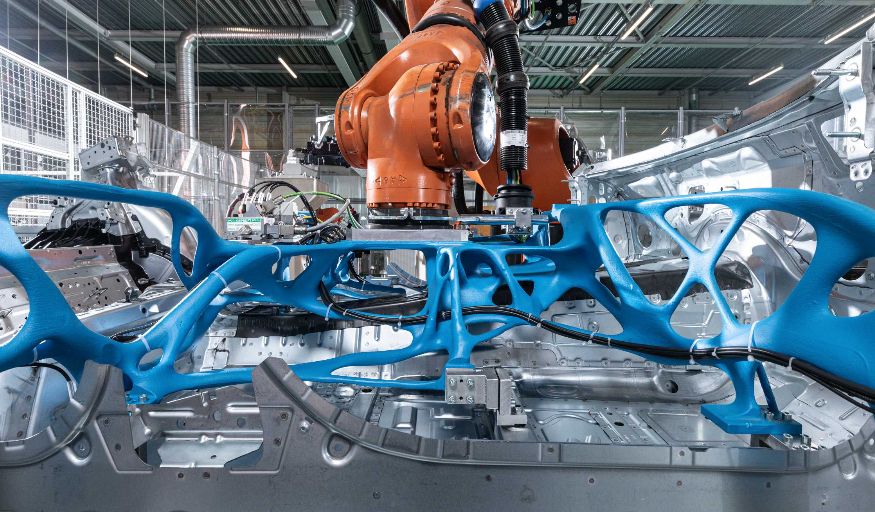
宝马集团扩大3D打印定制机器人夹具的使用范围
PressClub 保加利亚切斯卡新闻俱乐部PressClub 拉丁美洲, 加勒比海地区墨西哥新闻俱乐部PressClub 罗马尼亚 慕尼黑。凭借 30 多年的经验, 宝马集团是增材制造领域的先行者,更好 称为3D打印。早在1991年,3D打印机就开始使用了 生产单个车辆零部件,最初用于 概念车、原型车和赛车,然后用于生产 模型。宝马集团现在还生产许多工作辅助工具和工具 用于各种3D打印工艺中自己的生产系统。从 为员工量身定制的矫形器,以及教学和生产辅助工具, 到大型、重量优化的机器人抓手,用于以下用途 CFRP屋顶和整个地板元件。在「增材制造」上 位于Oberschleißheim的Campus“,宝马集团的中心枢纽 3D打印生产、科研、培训30多万 零件于 2023 年「印刷」。此外,超过 100,000 个打印部件 每年在形成全球的所有工厂中生产 生产网络,从斯帕坦堡和德国工厂到亚洲工厂。 “宝马集团越来越多地使用增材制造 生产系统有很多好处。例如,我们能够 快速、经济、灵活地生产我们自己的生产辅助工具 和搬运机器人,我们可以单独适应特定的 随时满足要求,并能够优化其 重量。重量更轻,生产线上的速度更快, 更短的周期时间,降低成本。此外,较小的机器人可以 用于中期,还可以减少 CO2 排放和 成本,「宝马增材制造负责人Jens Ertel说」。 “除了直接增材制造程序外,宝马 集团还一直在使用基于沙子的3D打印来制造模具 在兰茨胡特(Landshut)的工厂工作多年。通常使用此技术 制造原型铸件,以及大型 生产高性能电机零部件。另一个非常 现在有吸引力的应用领域是大型生产辅助工具。 Light 产品和工艺规划主管 Klaus Sammer 说 金属铸造。 用于生产铝制气缸盖的印刷模具 在大规模生产中 增材制造工艺已在日常工作中用于 在宝马集团兰茨胡特工厂工作了很长时间。多年来,这些已经 包括用于制造铝制气缸盖的模具, 使用砂型铸造工艺进行三维打印。 在这里,沙子被反覆涂成薄层并粘在一起 使用活页夹。这使得创建模具成为可能 制造非常复杂的结构,然后填充 液化铝。 使用3D打印制造用于CFRP屋顶的大型机器人夹持器 多年来,宝马集团的轻量化结构和 兰茨胡特的技术中心一直在使用一个特别大的 夹持器元件,使用3D打印工艺制成。 机器人的抓手重约 120 公斤,可以是 在短短 22 小时内制造出来,然后用于压力机上 为BMW M GmbH车型生产所有CFRP车顶。印刷机是第一位的 装载CFRP原料。夹持器只需旋转 180 度 度以拆除完成的屋顶。与传统相比 夹持器,使用3D打印制造的版本大约是20个 重量减轻百分比,从而延长机器人的使用寿命 还减少了系统的磨损和切割 维护间隔。两个步骤的组合使用也减少了 循环时间。机器人夹持器的一个独特功能是理想的 两种不同3D打印工艺的组合。虽然真空 夹持器和用于针夹持器的夹具,用于提升 CFRP 原始 材料采用选择性激光烧结(SLS)制成,大 屋面壳体和承重结构采用大规模制造 打印 (LSP)。LSP可用于生产大型元件 经济和可持续。该工艺使用注塑成型 颗粒和再生塑胶,而CFRP残留物也可以 被使用和回收。与使用初级原材料相比, 制造夹持器时的二氧化碳排放量约为 60 百分比降低。 新一代仿生夹具进一步减轻重量 2023 年夏天,新一代、更轻的抓手问世 介绍。为了实现这一点,分析了以前的夹持器概念 并优化了拓扑 - 仿生机器人抓手的诞生。 这将 LSP 打印机的屋顶外壳与 SLS 真空吸尘器和 仿生优化的轴承结构。为此,一个模具 印刷型芯用于砂型铸造。然后铸造这个模具 采用复杂的铝制结构。新的夹具是进一步的 比其前身轻 25%,这意味着整个过程 制造 BMW M3 的 CFRP 车顶只需一个即可完成 机器人,而不是像以前那样有三个。如今,双倍 宝马集团内部单独制造的夹具,由 3D打印,用于宝马集团兰茨胡特工厂的所有CFRP屋顶。 新的3D打印夹持器也用于运行中的底盘结构 宝马集团还采用了使用3D打印生产的夹具 底盘结构工艺 – 例如,夹具印有 用于处理宝马集团里根斯堡工厂门的LSP流程。 通过使用 3D 打印生产的优化轴承结构,我们 在搬运门时能够增加夹持器的刚性 里根斯堡工厂的元素,同时减少 重量。在随后的项目中,可以使用机器人 承载能力低,有助于降低成本,「弗洛里安说」。 Riebel,里根斯堡的门和翻盖生产主管。 然而,该公司现在在宝马集团更进一步 工厂慕尼黑。截至最近,仿生机器人的第一个例子 在母厂使用了夹持器。该夹持器可以保持和 移动 BMW i4 的整个地板元件。用于地板元件 夹持器,3D打印用于创建砂型铸造模具,这是 填充液态铝。承载在以下方面进行了优化 重量和最大负载能力,并称重所有附加 附加元件仅重 110 公斤。这使得它大约为30% 比以前的传统型号更轻。制造使用 砂型铸造和铝使代表复杂的成为可能 荷载优化结构。这样可以最大程度地减轻重量 因此,从中期来看,可以使用更小的和 更轻的重型起重机器人,需要更少的能量,因此 减少二氧化碳排放。Markus Lehmann,工厂负责人 宝马集团慕尼黑工厂的工程和机器人:「在慕尼黑 工厂,我们正在不断扩大生产辅助工具的使用 通过增材制造制造。说到这个领域 夹持器和处理系统,我们使用 3D 打印来装备我们的 已建立的夹具,带有单独的印刷附件,并且是 已经用高度集成和 重量优化的轴承结构。处理完整的 BMW i4 时 地板组装,这使我们能够减轻整个地板的重量 抓手减少 30% – 50 kg – 从而延长 我们的设施。 在增材制造中使用创新软件解决方案 复杂的仿生结构是使用 特殊的通用软件工具,如Synera。BMW iVentures 拥有 战略性地投资了这个软件,以前称为Elise。 Synera 允许快速有效地优化,现在用于许多 宝马集团内的开发领域。特别值得一用 3D打印软件,拓扑优化,仿生 结构几乎可以一对一地打印,这要归功于 3D打印工艺的灵活性。这使得它 可以充分挖掘轻质结构的潜力。 宝马集团的增材制造园区拥有一支 设计和施工专家,他们比较了各种各样的 软件解决方案,并使用它们来设计元件。知识是 然后通过增材制造在整个公司传递 校园。在夹具设计方面,特殊的工作流程是 开发和实施,允许计算和 轴承结构的构造将在很大程度上实现自动化,以及 因此快速高效。
了解更多
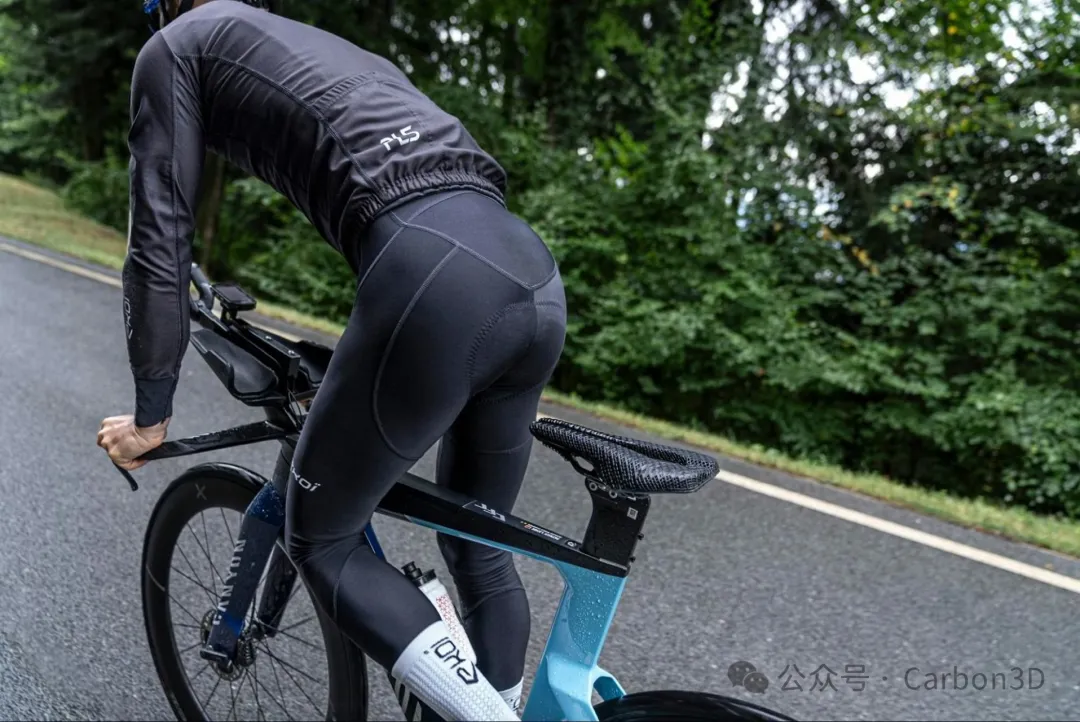
Selle Italia 和 Prototek 为自行车消费者打造更舒适的高性能鞍座
介绍 Selle Italia是一家位于意大利威尼斯郊外的自行车鞍座制造商。这家拥有百年历史的公司以拥抱创新而闻名,并决定为其品牌 Selle Italia 和 Selle San Marco 打造一款高科技鞍座,为客户提供更高水平的骑行舒适度。 虽然其他鞍座制造商也在采用 3D 打印,但 Selle Italia 希望使其产品与众不同,因此Selle Italia求助于公司附近的 Carbon 合作伙伴Prototek来开发这一款新产品。 这种关系和产品线迅速进入高速发展阶段,推出了多款基于Carbon增材制造平台开发的的鞍座。 材料和产品要求 Selle Italia 希望将其鞍座提升到一个新的水平,为此决定尝试增材制造技术。多年的公路自行车赛事赞助以及车座设计经验使该公司处于开发突破性新产品的有利位置。 为了满足精英自行车手所需的最高性能水平,Selle Italia 希望找到一种不仅能为骑手提供支撑,而且透气的材料,最终提供更舒适的骑行体验,其要求包括: --鞍座垫材部分有多个区域,可优化性能和舒适度 --柔软且有一定摩擦力的能量回弹性材料 --高透气性 --增加骑手的舒适度 --可以制造难以成型的结构 寻找合适的合作伙伴 Selle Italia 对采购自己的打印机群进行制造并不感兴趣,因此它们寻找可以协助鞍座的实际设计和产品开发以及生产路径的合作伙伴。在调研了当地潜在供应商后,Selle Italia选择与Carbon生产网络成员Prototek 合作。Prototek 的设计专业知识和数字化工厂让 Selle Italia 有信心开始与 Prototek 一起更新其经典车座、Selle Italia SLR Boost 和 Selle San Marco Shortfit 2.0 的设计。 确定最佳打印平台 Prototek 建议 Selle Italia 利用 Carbon增材制造平台制造 SLR Boost 和 Shortfit 2.0 鞍座,因为 Carbon 的打印技术可以轻松打印出 Selle Italia 和 Selle San Marco 想要的独特设计空间,而且其最终材料非常适合鞍座应用。Prototek 知道,通过 Carbon,Selle Italia 将能够实现他们用其他方式无法实现的目标。 Prototek 建议使用 Carbon 的 EPU 41高性能弹性聚氨酯材料,这是一种耐用、高弹性、能量回弹性材料,可为骑手提供缓冲和足够的摩擦力。它还适用于多分区晶格设计结构,这些设计非常透气,并且可以精确调整参数以提供各种机械响应,从而为骑手提供更好的骑行体验。 当 Selle Italia 和 Prototek 最初开始合作时,Prototek 安装了一台 M2 打印机。虽然完全能够生产优质晶格,但 M2 成形平台的尺寸对于鞍座生产而言相对较小。然而,Prototek 巧妙地设计了一种方法,将座垫部分分成两块打印,然后将其组装成一块供 Selle Italia 进行测试。功夫不负有心人,Prototek的努力得到了回报!M2上制作的原型样品成功向 Selle Italia 展示了潜力,并在大型 L1 打印机上使用 Carbon平台投入生产,使得鞍座的垫材可以一次打印成形。 “参与 Selle Italia 等顶级品牌的项目总是令人愉快的。他们拥有顶级标准,凭借Carbon的技术和材料,我们能够实现他们的目标并提供他们所寻求的东西。” 安德里亚·巴尔奇 Prototek 原型设计和 3D 生产部门主管 产品扩展和增长 到 2023 年夏天,Selle Italia 的 首款3D打印鞍座取得了销量上的成功,受到了非常积极的客户反馈。这使他们坚信 Carbon Digital Light Synthesis™ (Carbon DLS™) 是其鞍座在市场上脱颖而出的不可或缺的一部分。Selle Italia趁热打铁扩展了其 3D打印鞍座产品线,包括两个品牌的四种鞍座,分别用于高性能公路车、舒适型自行车和铁人三项自行车,这是有史以来第一个采用增材制造技术制造的铁三自行车鞍座,并与世界冠军铁人三项运动员帕特里克·兰格 (Patrick Lange) 合作开发。这些鞍座包括: --Selle Italia Watt 3D --Selle Italia SLR Boost 3D --Selle Italia Novus Boost Evo 3D --Selle San Marco Shortfit 2.0 3D 展望 随着 3D 打印鞍座的推出,Selle Italia 发现欣赏高端产品并爱好科技的客户兴趣急剧增加,表明消费者正在享受这种全新技术带来的骑行体验。2024 年,Selle Italia 的赛车鞍座将开始在环意自行车赛、环法自行车赛和环西班牙自行车赛的专业赛道上与车手一起亮相。 “ “我们始终以满足最苛刻的自行车手的需求为标准开发产品,努力提升他们的骑行舒适度并提高他们的运动表现。因此我们信任 Carbon 和 Prototek 等高级合作伙伴的 3D 车座项目,坚信我们之间的持续合作有助于提高自行车运动的整体创新水平。” 安德里亚·布扎沃 Selle Italia SRL 总经理 自从与 Prototek 合作生产以来,五个产品线已累计生产了超过 15,000 个鞍座,这不仅证明了客户需求,也证明了 Selle Italia 的创新以及 Prototek 的设计和生产专业能力。 源文摘自:Carbon 3D
了解更多
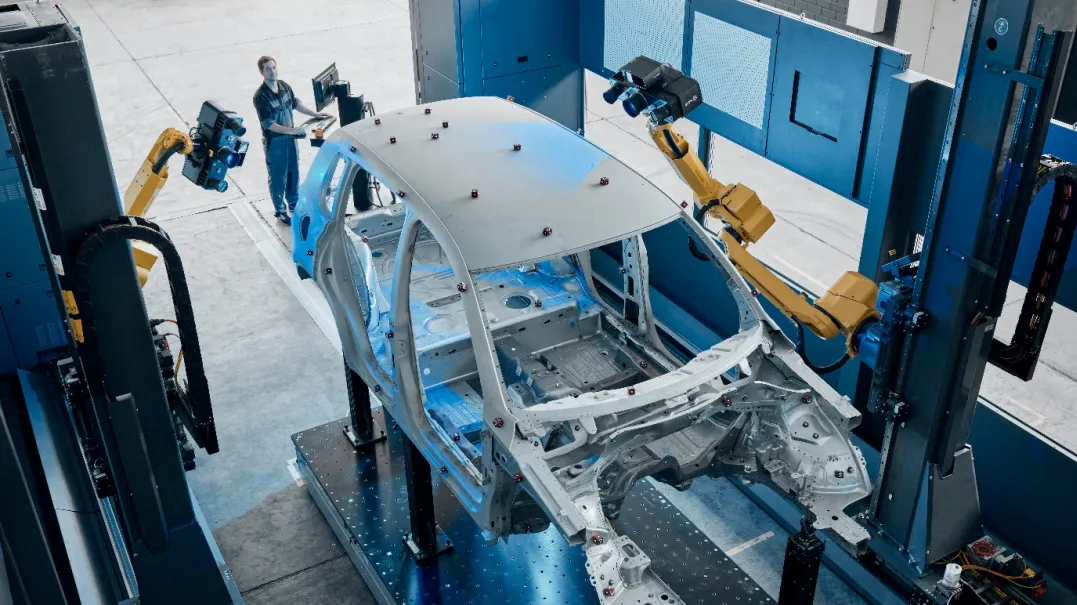
蓝光扫描技术助力钣金制造
近年来,汽车行业正在经历翻天覆地的变化,新能源转型,造车新势力不断涌现,智能制造不断深入到生产中的各个环节。如何在传统行业中提质增效?唯有拥抱新技术,拥抱新趋势。 传统钣金行业在工艺上已经相当成熟,但是对于数字化技术的应用更全面的质量控制仍然有提升的空间。 在一个简化的钣金成型方案中,工艺链包括四个主要步骤:产品研发,模具制造,试制和量产。而随着光学测量技术的不断发展,蔡司将光学测量技术和先进的软件技术相互结合,为传统钣金制造行业焕发新的生机贡献力量,可将其应用于钣金产品开发到量产的全生产流程。 在产品开发阶段,通常在一开始会制作一个设计模型,然后将其转换为数字化数据,例如CAD模型。在这个阶段ZEISS ATOS三维扫描仪将用于快速精准的扫描,从而获得逆向工程的数据。通过仿真模拟进行计算和优化从而设计出易于生产的零件。 模具制作阶段,ATOS三维扫描仪可以快速获取大型模具的高精度形面数据,全面的数据不遗漏每一处细节。从模具生产到模具试产试制,减少模具生产中的迭代次数,加速模具优化。经过优化的模具可以快速数字化来确保了在模具使用期间进行的任何更改都有可靠的存档。这种数字化数据还支持直接复制铣削,以取代损坏的模具。 在钣金试制中需要考虑部件本身的尺寸情况和相对于对手件的装配情况。利用扫描数据进行车身部件的三维数据检测和虚拟匹配分析,并可以进一步结合虚拟装夹技术进行产品装配状态预测,降低检具夹具等支出。利用ZEISS ATOS三维扫描仪结合ZEISS INSPECT软件实现对试制过程更快速全面的产品分析。 在产品量产阶段,我们需要掌控部件的生产状态,监控模具和部件的质量,保证其符合性和一致性,同时又需要满足高效率快节奏的生产要求。这就需要使用自动化测量单元,ZEISS ScanBox 以其高效,精准,智能的特点,可以获得更高的吞吐量和更高的可重复性。结合ZEISS ATOS扫描仪可以更加快速地获取部件表面数据,提供整个零件表面、孔、槽、修边和回弹的尺寸检测,以及趋势分析。 蔡司基于其技术创新和研究成果生产和研发引领行业的三维扫描系统。持续不断地开发和提升软件和硬件水平,为您提供完善地三维扫描解决方案。我们的产品广泛应用于工业生产,科研,教育等诸多领域。并将根据您的具体需求为您选择理想的产品和技术方案解决您的测量问题,持续为您提供可靠的技术支持,确保与您共同成功。
了解更多
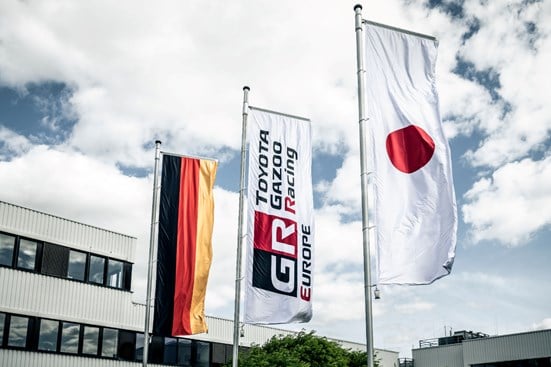
TOYOTA GAZOO Racing Europe 选择 Stratasys 的立体光刻技术进行空气动力学测试
Stratasys 和 TGR-E 宣布建立激动人心的合作伙伴关系,将使用行业领先的 Neo 立体光刻 3D 打印机进行风洞建模。 TOYOTA GAZOO Racing Europe (TGR-E) 总部位于德国科隆,是丰田赛车运动工程和开发的中心。 TGR-E负责为着名比赛(如国际汽联世界耐力锦标赛卫冕冠军GR010 HYBRID)开发高性能汽车的技术开发,并为现任世界拉力锦标赛冠军GR Yaris Rally1 HYBRID生产发动机。除此之外,该团队还为其他在顶级赛车运动中工作的组织和团队提供专业的开发和生产服务。 使用 Neo 进行敏捷建模 在高风险的汽车工程领域,风洞建模对于提高汽车空气动力学性能至关重要。3D打印是这项创新的最前沿,使工程师能够对复杂元件进行原型设计,并以无与伦比的速度和精度生成用于测试的小规模模型。 SLA 3D 打印是汽车原型制作和工具制作的理想选择,因为它能够创建高精度和详细的元件,同时大大缩短了后处理时间。Stratasys 的 Neo SLA 打印机提供一流的光滑表面和复杂的几何形状,这对于准确的空气动力学测试至关重要。 借助 Neo,TGR-E 团队可以基于有形的风洞数据创建快速反覆运算设计,由于 Neo 的高精度,节省了大量的后期处理时间。 Neo 生产的缩放风洞模型具有准确的侧壁质量和精度,使工程师能够可靠地模拟真实世界条件,从而有效地分析空气动力学性能。 TGR-E 的团队与 Stratasys 转销商 ProductionToGo 合作,选择了 Stratasys 的三台 Neo 立体光刻 (SLA) 3D 打印机来支持风洞建模。 “与 Stratasys 和 Production2Go 的每个人的开放和建设性合作特别积极,”Toyota Gazoo 集团负责人 Christopher Sigmund 说。 该团队对 Neo 的印表表面质量以及打印机的易用性印象深刻。 Christopher Sigmund 继续说道:“这些打印机非常稳定,运行速度比我们以前的 SLA 打印机高得多。大多数元件都具有非常好的表面,几乎不需要返工。 首席技术员Manfred Werner对此表示赞同:「 该软件非常直观。您可以快速浏览各个控制面板并找到自己的方式。Neo 的光滑表面和尺寸精度非常好,零件可以很容易地返工。Neo 是我近 22 年的 3D 打印职业生涯中有幸操作过的最好的 SLA 机器。 Somos PerFORM树脂在风洞建模中具有高耐热性和出色的打印分辨率® Somos PerFORM格式®材料可生产坚固、耐高温的复合材料部件,其粘度是所有复合立体光刻材料中最低的。零件制造速度更快,更易于清洁,并具有卓越的侧壁质量,具有无与伦比的特征细节。 “我们密切参与了PerFORM的早期开发,我们知道我们想与它合作。它是满足我们需求的最佳材料。 ——Thomas Linke,TGR-E 复合材料和增材制造经理
了解更多
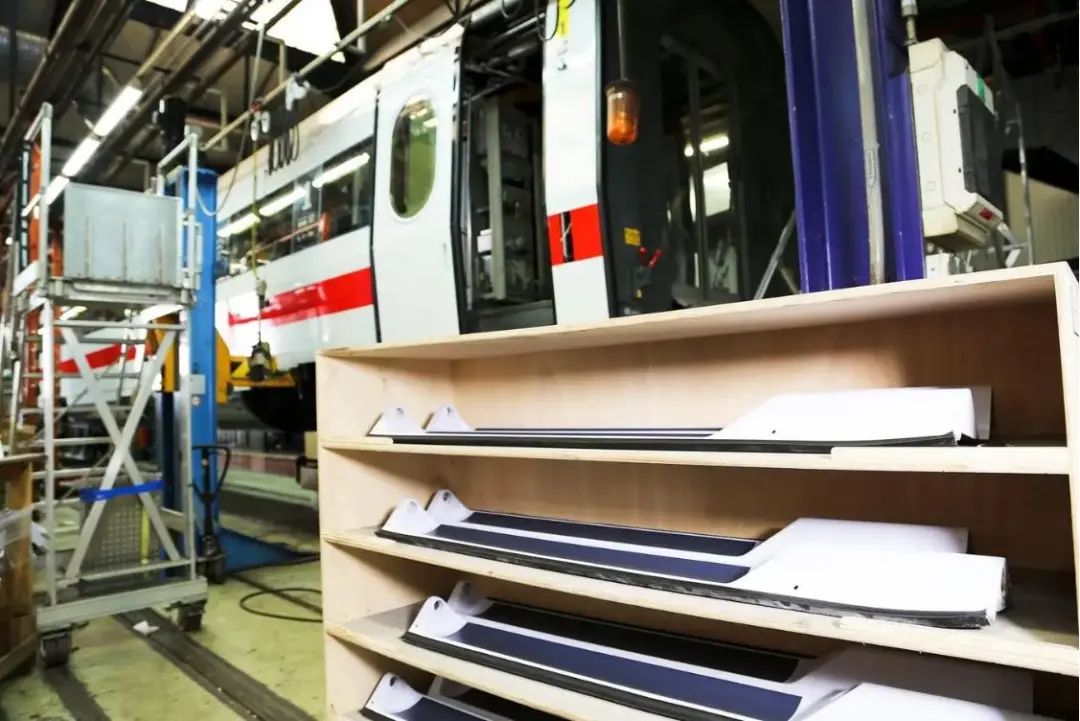
德国联邦铁路公司使用Formlabs打印10 万余个部件,节约数百万欧元
德国联邦铁路公司正在逐步扩大3D打印应用。从2015年开始使用3D打印技术起,德国联邦铁路公司内部生产了 10 万余个部件,节省了数百万欧元。3D打印有效帮助他们满足工厂的日常需求,提前为不同的应用进行设计,直接在现场生产,然后在工厂实施,与传统工具相比,提供了更大的设计自由度和灵活性。 德国联邦铁路公司 (DB) 是世界上最大的铁路公司之一,每天运送超过 1000 万名乘客。维护运送数百万人所需的庞大基础设施并非易事——该公司在全德经营着 50 家工厂,为其客运和货运列车提供服务。 DB 车辆维修子公司的新明斯特工厂位于最北端,拥有近 750 名员工,负责城际列车和通勤列车乘客车厢的维护、修理,有时还进行全面检修或现代化改造。该工厂也是拥有现场 3D 打印车间的设施之一,旨在提高运营效率。 “我们在 2015 年就开始使用 3D 打印技术,从那时起,我们已经在德国联邦铁路公司内部生产了 10 万余个部件,节省了数百万欧元。” ——德国联邦铁路集团 3D 打印项目营销专家 Susanne Tost 接下来,让我们了解一下德国联邦铁路公司制造工程师兼增材制造专家 Carsten Wolfgramm 和德国联邦铁路集团 3D 打印项目营销专员 Susanne Tost 是如何使用 Formlabs 3D 打印解决方案生产制造辅助工具,以简化工作流程、降低成本,并帮助列车快速恢复运行的。 现场按需生产制造辅助工具 城际快车 (ICE) 是德国联邦铁路公司的旗舰客运服务,主要面向商务旅客和长途通勤者,时速高达 320 公里。 第一代 ICE 1 客运列车已投入运行长达 30 余年,现在正在进行全面翻新:几乎全部拆除、从头开始重建、配备现代化设施,并重新喷漆。 这一大型现代化项目需要多个工厂和部门以及油漆工、锁匠、电工等各行各业的人员密切合作。新明斯特工厂则是此跨国运营的中心之一。 新明斯特 DB 车辆维护厂是参与 ICE 1 客运列车大型现代化项目的工厂之一。 Wolfgramm 表示:“制造辅助工具必不可少,因为使用现有的传统工具无法完成所有工作。” 在翻新每个部件以及拆卸或重组客运列车的过程中,有许多步骤都可以更轻松地完成,以节省时间或确保质量和一致性。在对数十辆客运列车进行现代化改造时,这些工具的优势就会迅速凸显。 “通过与本厂以及其他工厂的人员密切合作,我们正在开发大量实用工具,旨在帮助工人粘贴图形、画线或标记钻孔位置,消除大量测量时间。如今,3D 打印技术可以制作出色的模板,让工作变得更轻松。”Wolfgramm 表示。 传统上,这些制造辅助工具均在木工车间由木材通过锯切、打磨和铣削制作而成,或者在需要金属部件时使用车床或铣床等传统金属加工机器。然而,这些解决方案更加耗时、费力且昂贵。 “增材制造提供了无可匹敌的能力,可以快速处理初始形状,然后对其进行改进。因为我们拥有 CAD 软件中的数字设计功能,所以如果出现不合适或需要更改的情况,我们可以快速调整。对于设计的更新、放大或缩小,3D 打印(尤其是粉末打印)可谓是意义非凡。” ——德国联邦铁路公司制造工程师兼增材制造专家 Carsten Wolfgramm 新明斯特的 3D 打印车间拥有十台不同的 3D 打印机,其中包括两台 Fuse 系列 SLS 打印机。 位于新明斯特的 3D 打印车间拥有十台搭载多种技术的不同 3D 打印机。其中两台是 Fuse 系列 SLS 打印机,一台使用多功能且强度高的 Nylon 12 Powder,另一台使用柔性材料 TPU 90A Powder。车间里还有两台树脂打印机,一台是大幅面 Form 3L 打印机,另一台是 Form 3 打印机。 Wolfgramm 及其团队可以根据部件要求,选择更适合的打印工艺和材料。 “我们之所以使用 Formlabs 设备,是因为其性价比对我们来说是无可匹敌的。它们非常可靠、即插即用,尤其是 SLS 打印机。其部件不断迭代,可以简化工作。而且这些打印机可以全年不间断运行。” ——德国联邦铁路公司制造工程师兼增材制造专家 Carsten Wolfgramm 将 3D 打印车间设在新明斯特,可以使团队保持灵活性,并根据需求快速响应。Wolfgramm 说:“不同于发送订单,我们不再依赖于供应链和漫长的周转时间。” “借助 3D 打印技术,我们能够非常迅速地满足工厂的日常需求。我们可以提前为不同的应用进行设计,直接在现场生产,然后在工厂实施。没有其他任何生产厂家能为我们提供这种服务”,Tost 补充道。 新明斯特的增材制造应用 喷漆用遮蔽工具 在修复 ICE1 客运列车时,所有塑料部件都要拆除、打磨、填充并重新喷漆。其中一个部件是安装在每节车厢门把手后的大型凹槽塑料面板。每块面板都需要采用新型双色油漆设计,这样深色部分可以更持久地防止留存污垢和使用痕迹。 喷涂弧形和更复杂的油漆方案通常需要使用折叠尺和卡尺费力进行测量,以便油漆工正确标记位置和遮蔽表面,从而实现一致的效果。 遮蔽有机形状一直都是一种耗时的手工操作。 3D 打印遮蔽工具可以大幅减少测量花费的时间。 “利用 3D 打印技术,我们可以轻松开发模板。只需制作一次,然后就可以在其他工厂和地点以各种方式加以利用。例如,我们可以将30 分钟的喷漆工作缩短到 2 分钟。” ——德国联邦铁路集团 3D 打印项目营销专家 Susanne Tost 与传统工具相比,3D 打印提供了更大的设计自由度,可以制造出适合特定工作的复杂工具。Wolfgramm 补充说:“增材制造技术,尤其是 SLS 工艺,可以实现复杂的几何形状,如半径和小凸起。” 行李架的划痕保护 长途客运列车在拆卸时,行李架会被拆除。修复完成后,一旦粉刷车厢壁并重新加固,就需要将行李架放回原位。而这些行李架又大又重,而且与车厢壁之间的缝隙非常小,因此需要一种柔性材料作为防刮伤和防撞击的保护层。如果工人不小心划伤了车厢壁,就会需要返工,这不仅成本高昂也十分费时。DB 的团队设计了定制保护罩,并在 Fuse 1+ 30W 中使用柔性材料 TPU 90A Powder 进行打印。 该团队使用柔性材料 TPU 90A Powder 进行划痕和冲击保护。 SLS 3D 打印实现了可以安装在行李架和车厢壁之间的超薄设计。 “在我们开发出这种划痕保护装置并使用 3D 打印出来之前,我们的同事总是使用气泡膜或类似工具进行传统遮蔽工作,以试图避免划痕,但这并非每次都能成功。由于采用了新的 TPU 部件,我们终于第一次成功地完全消除了划痕。” ——德国联邦铁路公司制造工程师兼增材制造专家 Carsten Wolfgramm 电缆导向器盖帽原型 由于 ICE 1 客运列车生产已有 30 多年之久,有些部件已经不复存在。在修复过程中,团队发现许多安装在座椅下方的、用于保护和引导插座电缆的盖帽在清洁时破损或完全丢失。由于这些都是定制部件,他们无法轻易找到替代品。 在 ICE1 客运列车中,许多保护和引导电源插座电缆的盖帽均已丢失。 DB 的团队对设计进行了逆向工程,并使用 SLS 3D 打印原型来测试配合度,并获得真实尺寸。 “DB 公司对这些部件进行了重建,并要求我们使用 SLS 3D 打印技术和 Nylon 12 Powder 打印原型,以测试是否匹配并了解实际尺寸。我认为第二个版本已经非常匹配,可以轻松滑入就位。SLS 打印技术提供的可能性是超卓的。配合度、速度和材料强度都很高,因此我们可以进行实际尝试。”Wolfgramm 说道。 手持扫描仪支架 制造辅助工具还可用于简化各工厂工人的日常工作。DB Fernverkehr 公司从事材料管理的员工使用手持扫描仪识别和管理材料。通常情况下,他们必须手持扫描仪,如果要拿东西或使用双手,就必须放下设备。 材料管理部门的员工需要一种安装手持扫描仪的方法,便于将扫描仪放在身边,而不用一直占用一只手。 该团队制造了三种不同的支架,可以固定在包、腰带或工具箱上。 “他们问道:‘你们就不能为这个手持扫描仪设计一个支架,让我们可以随身携带、随时使用吗?’ 最终,我们设计了三种不同的支架,可以固定在包、腰带或工具箱上。SLS 3D 打印很简单,因为它可以打印出真实尺寸,而且我不需要移除任何大型支撑结构,所以除了除粉和喷砂之外,我不需要做很多后处理操作。”Wolfgramm 说道。 面向未来的车辆维护数字化 “增材制造将长期存在。它使传统机器无法实现的复杂几何形状成为可能,并可以轻松制造和复制工具,而不会产生高昂的额外成本。工具或部件在数字化后,就可以在世界任何地方打印出来。我们的目标是到 2030 年在车辆维护中实现 10% 的备件数字化,这将支持我们快速按需再制造部件,确保我们能够继续快速交付部件,同时也确保生产过程以及材料和资源处理过程绿色环保,从而解决许多其他挑战。” ——德国联邦铁路公司制造工程师兼增材制造专家 Carsten Wolfgramm 列车的安全法规与飞机一样严格,有时甚至更加严格。如今,只有现场的工业级 FDM 打印机才能满足这些严格的规定。德国联邦铁路公司正在与 Formlabs 公司和其他合作伙伴联手,开发工作流程、工艺和材料,以便在未来通过认证以满足这些要求。
了解更多
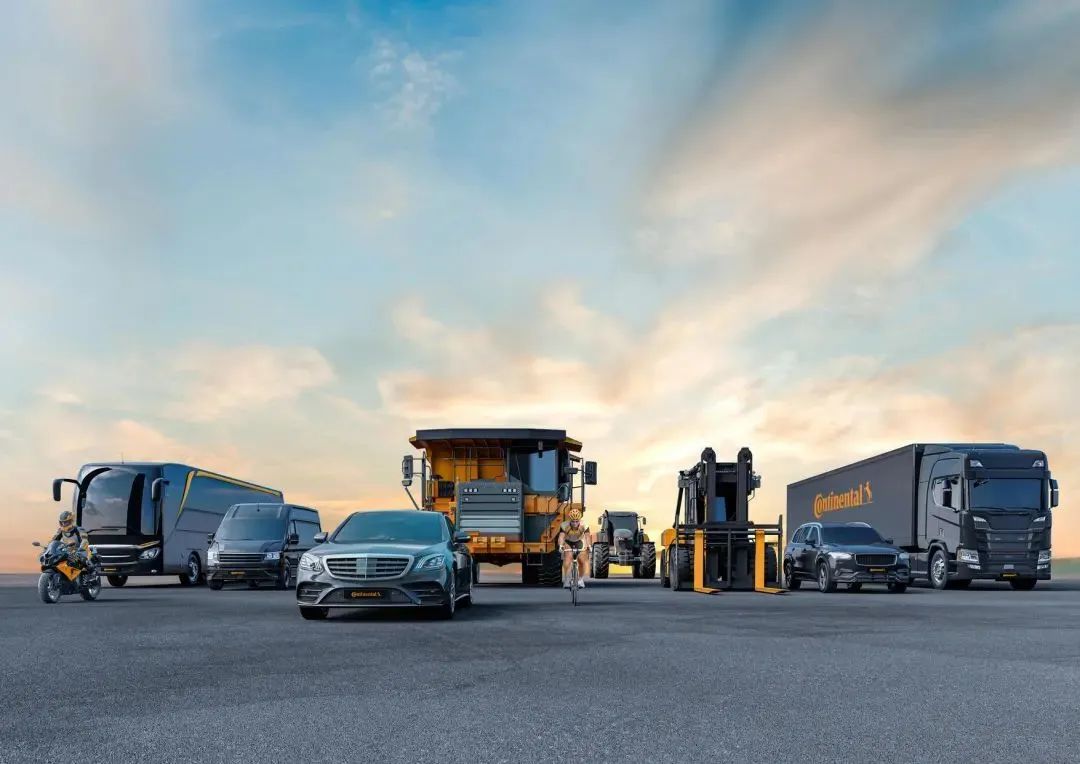
德国大陆集团引入Stratasys FDM技术,用于生产防静电释放汽车部件德国大陆集团引入Stratasys FDM技术,用于生产防静电释放汽车部件
汽车制造商大陆集团为其位于德国卡本的增材制造能力中心(ADaM)全新安装了一台Stratasys Fortus 450mc FDM 3D打印机。 尽管以轮胎闻名,但大陆集团也生产汽车零部件并通过大陆工程服务(CES)部门提供汽车服务。 该公司认为低成本、高产能和电气安全是制造业成功的关键,而这些特性在Stratasys的3D打印技术中均有所体现。 目前全球经济环境仍存在挑战,增材制造为企业提升产品开发效率发挥着关键作用。随着越来越多专业级材料的出现,制造商能够满足传统生产应用中的严苛要求,并为其提供更多定制化服务。 ——Yann Rageul Stratasys制造事业部负责人 大陆集团增材制造能力中心为内外部客户提供各式各样由金属和热塑性塑料制作的增材制造样品、机械部件和系列组件。这个顶尖的能力中心拥有强大的工业级增材制造技术。 自1996年以来,我们一直在传统生产方法之外使用增材制造技术进行生产,我们的增材制造能力中心让我们得以在更大范围内,将3D打印融入从设计到后期生产的运营全过程。 ——Stefan Kammann CES样品和机械解决方案负责人 大陆集团一贯非常重视生产速度和零件质量,全新安装的Fortus 450mc 3D打印机被用于制造集团自有生产线上的功能原型、最终使用零件,甚至是夹具。 仅仅数小时就能打印出组件,这为团队发掘出更多灵活度和潜在效能,尤其是在生产很难采购的备件时。对此,大陆集团表示Fortus 3D打印机能“加快生产流程并确保持续的自动化生产”。 有了Fortus 450mc,我们可以用高效能的热塑性塑料快速进行备件和部件的生产,且预期效果与传统制造方法相当。重要的是,这避免了使用传统制造工具所需的冗长工期,还能省去大量因等待备件耗费的停机时间。 ——Stefan Kammann CES样品和机械解决方案负责人 大陆集团生产的很多3D打印部件都会在生产车间与电子元件接触,这就意味着它们需要具备静电耗散特性以防止静电释放(ESD)。一旦静电释放,就会破坏产品甚至引起火灾。 因此,大陆集团选择Stratasys的静电耗散材料ABS-ESD7生产应用工具,因为它能提供足够的耐久性和稳定性。 我们使用Stratasys的ABS-ESD7为汽车显示屏3D打印出胶合夹具,这让我们拥有了内部定制的快速、安全、防止静电释放的解决方案。这不仅能确保连续快速的生产,也说明我们是如何为制造难题找到技术解决方案。事实上,Fortus是唯一一款能够在很短时间内生产出静电耗散部件的3D打印机。 ——Stefan Kammann CES样品和机械解决方案负责人 可以说,有了Fortus 450mc,大陆集团的汽车零部件生产水平得到了全新提升——在快速生产高质量零部件的同时也降低了成本,进而满足更为严苛的生产需求。 Fortus 450mc与我们的产品生产和服务解决方案进行了无缝衔接。我们看到客户对3D打印零件的需求正在不断增加,因此我们将继续扩大对这项技术在设计和生产中的应用,以确保不断优化我们的服务。 ——Yann Rageul Stratasys制造事业部负责人
了解更多
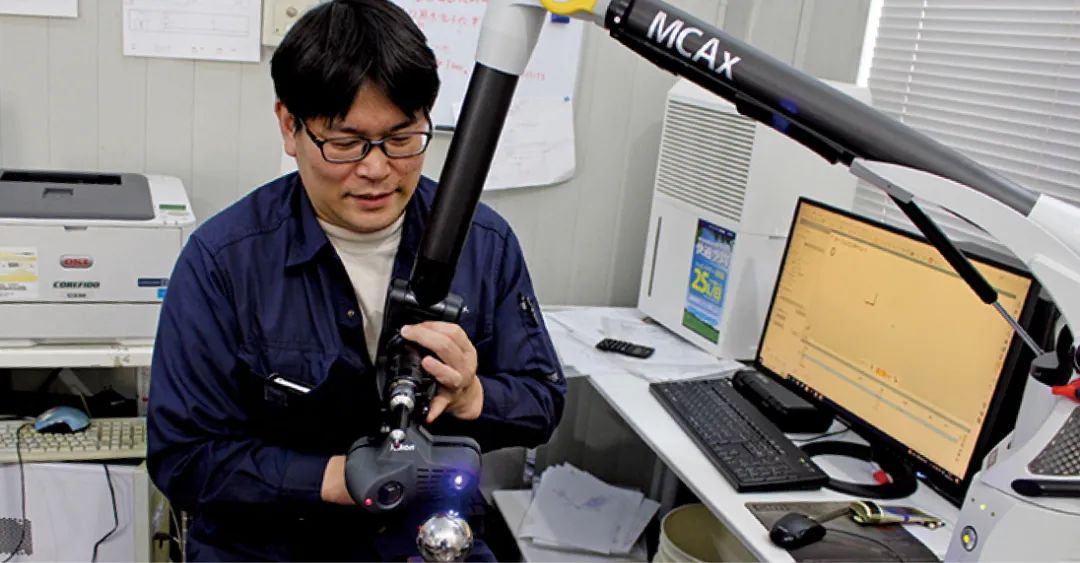
加藤精工:逆向三维技术开辟汽车领域新天地
总部位于日本名古屋的加藤精工是一群专注于冲压模具的金属加工专业人员。该公司的主要产品是汽车冲床刀具和模具,但它也以其用于从钢材到树脂的多用途加工技术而闻名,这些材料可以进行机械加工或车床加工。近年来,该公司将重心转向逆向工程,利用3D扫描仪和Geomagic Design X,使其成为新的核心业务。 为了更好地了解工程情况我们采访了在加藤精工领导这些活动的石黑文也 问: 为什么加藤精工采用逆向工程,这个过程是如何运作的呢? 石黑表示: 汽车零部件制造商在设计阶段需要具有特定角度槽的零件,会在设计阶段创建这种形状的3D数据。然而,由于以这种方式制作的样品会手工刮削以满足较小半径的需求,最终产品将具有无法量化的自由形状。因此,当以后需要相同的零件时,我们别无选择,只能精确测量和量化零件本身,并制作具有相同形状的新零件。 面对这一挑战,加藤精工在近15年前开始探索逆向工程技术。然而,优质的结果并非一夜之间就能实现。 “我们从轮廓加工开始”石黑解释说: 当我加入公司时,我们获得了一个3D扫描仪并开始了一种新的方法。在最初的几年里,由于精度不佳,该过程变得困难。我们从3D扫描仪获得的网格数据不够准确,机械加工零件的表面呈现出斑驳的图案,因此我们不得不手工抛光每个零件的表面。 手工抛光是公司逆向工程过程中最大的瓶颈,石黑专注于提高准确性并消除这项任务。经过多次研究,他发现了Geomagic Design X。他立刻对该软件进行了测试,但他并没有立即确信结果已足够准确。然而,他一直密切关注这个产品,十年后,Design X成为加藤精工逆向工程工作流程的一部分。 Design X和加藤精工的工艺满足了日本最高精度要求 石黑说: Design X本身得到了很大的改进。我不知道如何描述我想做什么,但Oqton的团队立即表示理解并为我们制定了解决方案。这非常重要,即使软件具有你需要的功能,但你不知道这个功能存在,那就等于没有。 Design X使石黑能够快速编辑3D扫描的网格数据这极大提高了逆向工程工作流程的效率除了更好的数据准确性之外多年来一直困扰石黑的“抛光”不再是必要的机械加工和机床操作变得更加高效总体机械加工速度大大提高 加藤精工所在的东海地区是许多为主要汽车公司提供服务的金属加工公司的所在地。竞争激烈,客户在日本有着最高的要求。 石黑说:“过去一毫米的误差是可以接受的,但逐渐容差变成了三分之一,然后是十分之一毫米,现在我们正在与百分之五的容差竞争。” 石黑补充道:“这是主要制造商可以通过他们顶级机器实现的精度水平。我们的机器无法与它们相媲美...我们必须不断提高我们的技能,以免输掉竞争。” 加藤精工的业务也随着对3D逆向工程测量相关产品的新订单而不断增长。 石黑热情洋溢地说 “我们赢得了客户的信任,工作开始涌入。如果汽车生产恢复,我们将能够进一步扩张。这真的是一个新的起点。”
了解更多
ZEISS 三维扫描仪 | 3D打印 普立得科技
普立得科技成立于2004年,专注于工业级3D打印机与三维扫描,同时我们也是ZEISS GOM代理商,并提供3D打印及扫描的代工整合服务,特此加值整合相关软体,包含拓扑优化设计 、医疗影像分析、逆向工程 、3D检测等,期望推进积层制造的使用习惯为生产带来更多价值。





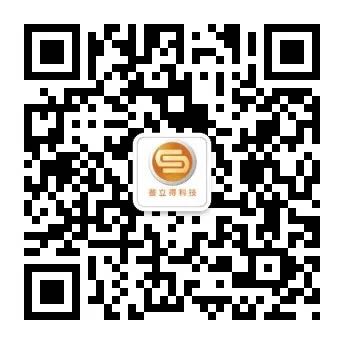
微信公众号
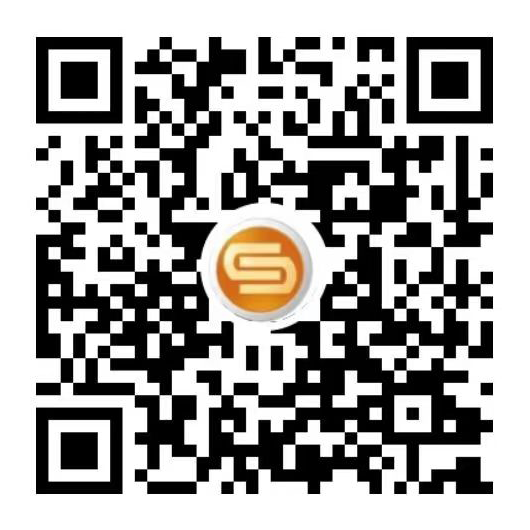
视频号
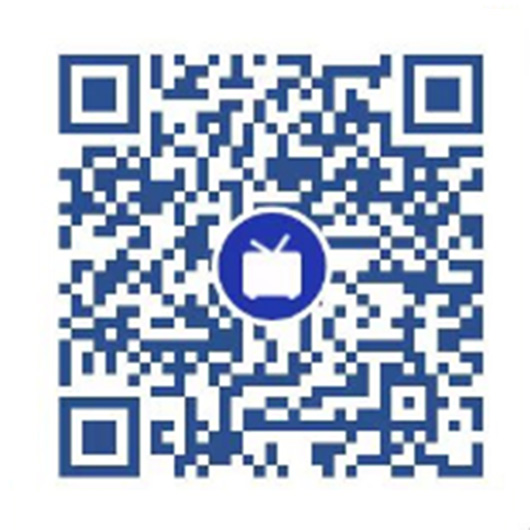
哔哩哔哩
您有什么疑问,或想咨询我们的产品与服务,请留下信息,我们会及时与您联系!
© 2021 普立得科技有限公司 All Rights Reserved 粤ICP备19059200号